The contrast between PSA’s two Mercosur plants is great – yet they are both earmarked to play a key role in PSA President Christian Streiff’s emerging markets growth plans. Mark Bursa takes a plant tour or two.
A tour of PSA’s two Mercosur plants is something of an eye-opener. Here are two very different plants – one in Argentina and one in Brazil. The Argentina plant, at Palomar, is a suburban plant built in the 1960s. Buenos Aires’ suburban sprawl has grown around the plant, making logistics difficult and limiting future expansion possibilities.
The contrast of the Brazilian Porto Real plant could hardly be more marked. Built on a Greenfield site near Rio de Janeiro, and only opened in 2001, Porto Real is a model 21st century emerging markets plant: flexible and lean, and with minimal high-cost capital equipment – there are only 25 robots, all welding robots in the body shop. Labour remains cheap in Mercosur, and replacing humans with robots is hard to justify. “Robots are more expensive and they lose you flexibility,” said Porto Real plant manager Tarcisio Telles. “There has to be a technological reason to replace people with robots.”
Yet as PSA plans to expand Mercosur production from around 300,000 this year to 500,000 by 2010, it is the venerable Palomar plant that will take as much of the strain as Porto Real. With its clanking overhead conveyors, Palomar brings to mind East European plants such as FSO in Warsaw – and of course the two have much in common, having been built with similar Fiat technology.
Yet Palomar is every bit as flexible as Porto Real – in fact more so, as it produces a wider variety of different models on its assembly lines. And there are more robots – all of them for bodyshell and floorpan welding. Many of the robots were supplied by Fiat’s automation arm Comau – a legacy of Fiat’s past involvement in the factory. Despite this, almost 1,100 people work in the body-in-white shop. Much of the welding is still manual, while there are no framing robots – body side panels are manually swung into place from unpowered roof-mounted conveyors.
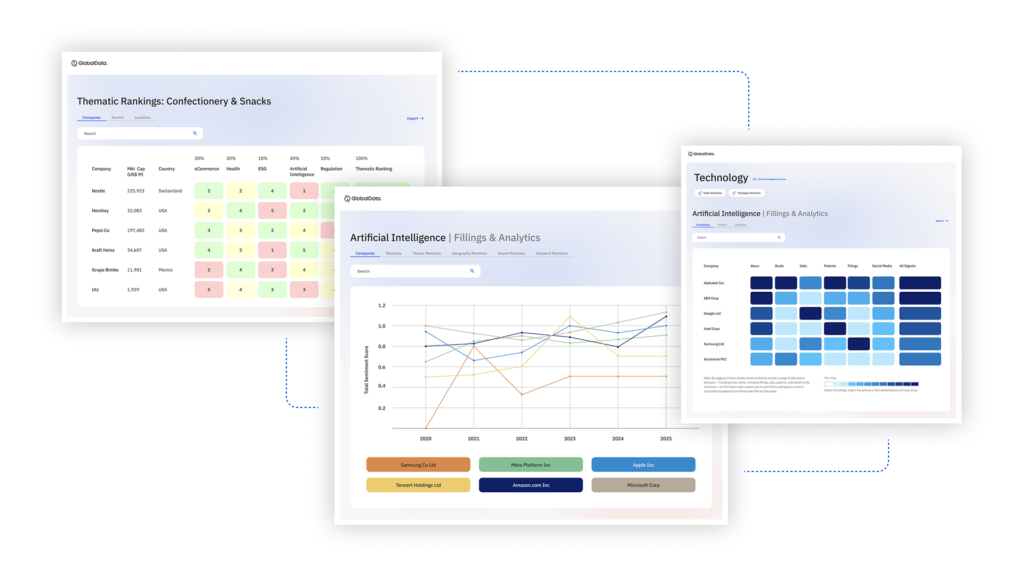
US Tariffs are shifting - will you react or anticipate?
Don’t let policy changes catch you off guard. Stay proactive with real-time data and expert analysis.
By GlobalDataIn the body shop, Peugeot 307 sedan and hatchback bodyshells trundle down the line alongside Citroen Berlingo vans and Citroen C4 Pallas sedans. At Porto Real, two flavours of Peugeot 206 – hatchback and SW – are built alongside the Citroen C3 hatchback, though the Citroen Xsara Picasso is built on a separate line.
A third shift has just gone on stream at Porto Real, and this will boost capacity from today’s annualised level of 110,000 to “a little over 150,000” in 2008, said Telles. The third shift has upped employment at Porto Real from 2,650 to 3,400 workers, and triple-shifting will raise output to 27 cars per hour. Not bad for a plant originally designed to build just 80,000 vehicles a year.
Telles wants to expand the plant without major building work – some construction is currently under way to add a machining shop for cylinder blocks and heads to the engine shop, but he said “there is no plan to add square metres to the assembly line.” Under these circumstances, adding up to 100,000 further units of capacity will present a major challenge.
Indeed, despite strong lobbying from Brazilian authorities, it looks likely that the lion’s share of the additional 200,000 units of capacity will go instead to Argentina – simply because there is more available space. “We can restart empty capacity at low cost in Argentina – it’s not so easy in Brazil,” said PSA Peugeot Citroen president Christian Streiff. Palomar may be surrounded by urban sprawl, but its site is large – 73 hectares –and it has 248,000sq m of buildings. It employs more people than Porto Real – around 3,500 – and produces more cars per hour – 30. Logistical access is the biggest problem – though new road and rail links are planned.
The plant has earned praise from Christian Steiff – but it was not always so successful. A look at Palomar’s history and output figures over the past decade and a half prove just what a rollercoaster ride it’s been for PSA’s Argentina plant. It was originally built by Fiat in 1960, and 20 years later PSA became involved when it formed a JV called SEVEL with Fiat – a programme unrelated to the European LCV venture of the same name between the same partners.
The Latin American SEVEL was a lot less successful, and was dissolved in 2000. As part of the divorce settlement, Fiat retained its massive Betim plant in Brazil, while PSA took over Palomar. But by then, Mercosur was in the grip of an economic crisis, and production tumbled from 142,018 units in 1993 to just over 30,000 in 2000. A recovery in 2001 was short-lived, and output plunged to just 17,820 in 2002, when an even deeper economic crisis and raging 41% inflation in Argentina limited working to just 6 hours a day, 10 days a month.
Only now is Palomar getting back up to its 1993 levels. It’s projected to reach 121,253 units in 2007, and PSA is forecasting 164,865 units in 2008. PSA has invested steadily in the past two years adding new models – €61.3m in adding Peugeot 307 hatch and sedan in 2006, and a further €86.2m adding the C4 Pallas sedan in 2007. The C4 Pallas and 307 sedan are also made in China.
Palomar is a big site, and Japanese-style Hoshin improvement programmes have contributed to making production lines shorter and faster. “We saved the Berlingo project through doing this and we have freed up more than 2,000sq m of floorspace,” said Gabriel Schwarzbaum, bodyshop manager at Palomar. “Now we are trying to make sure we have enough space to add a new model next year.”
The Hoshin continuous improvement programmes are heavily used at both Mercosur plants. The programme is based on Japanese methods and originated within Faurecia, PSA’s in-house components arm. Under Hoshin, groups of ten workers work together for five days identifying problems, deciding on solutions and putting them immediately into practice.
At Porto Real, it has been extremely successful, with more than 50 initiatives implemented in the past two years, resulting in big savings. Productivity has increased by 17% in 2006 and 56% in 2007, while available floorspace gains totalled 1,565sq m in 2006 and 964sq m in 2007. Defects reduced by 55% in 2006 and a further 50% in 2007. More than 160 specific improvements in workstation ergonomics were made in each of the two years and efficiency improvements meant 32 line workers could be transferred to other areas, reducing the need to recruit additional new staff. Current efforts are centred around de-bottlenecking the paint shop in order to maintain growth.
One advantage Porto Real has over Palomar is an integrated, in-house engine facility. PSA does have an engine plant in Argentina, at Jeppener to the south of Buenos Aires. Palomar is west of the city. Jeppener has recently received a €15m investment to add upgraded diesel and large petrol engines; it currently makes DW8 and DW10 diesels, as well as suspension parts.
While Jeppener specialises in diesels, Porto Real engine plant, opened in March 2002, makes only gasoline and flex-fuel engines that can run on ethanol or gasoline. In 2007, flex-fuel engines were the most popular, accounting for 62% of output against 38% gasoline. The two plants cross-supply both the assembly plants, though the engines are unsuitable for export to Europe as they do not meet current Euro 4 standards, being a mix of Euro 2 and Euro 3.
Porto Real is a lean plant employing just 195 workers building two types of engines– TU3 (1.4-litre) and TU5 (1.6-litre). Both come in gasoline or the increasingly popular flex-fuel guise, though the two ranges are unrelated and share no major components. Output this year is expected to be 163,000 – 80,000 TU5s and 83,000 TU3s. In February 2008, output will be upped to 220,000, and the new machining shop, which will go on line in 2009 will allow cylinder heads and blocks to be machined on site.
Local Mercosur content is currently85% on TU5 and 42% on TU3, and this will increase when cylinder blocks are sourced from Argentina rather than France in the near future. Quality levels are high – 99.5% of engines come off the line without needing any remedial work. The only hiccoughs have come when production has been increased and these are “not catastrophic”, according to PSA.
Mark Bursa
‘Coolbear’
See also: EMERGING MARKETS ANALYSIS: PSA empowers its local managers in Mercosur