Original Equipment Manufacturers (OEMs)
must ensure that suppliers who support them are instructed specifically on what to supply
and when. In addition, the high volume of transactions associated with producing, for
example 30 units per hour, 24 hours per day, lends itself to a mechanism for automatically
handling the data transactions that mirror this process. The compulsion for using EDI is
for both transactional efficiency and control of manufacturing. The make-to-order process
can only be made practical using EDI. To ensure the effectiveness of a closed loop system
between OEM and supplier, it is essential that EDI is implemented and integrated.
The ability and success by which OEMs
achieve this has a direct bearing on their future competitive position. It is no surprise
then that OEMs want EDI messaging, and mandate integration with the supplier’s ERP system.
The ability to coordinate materials flow and concurrent processes accurately and
responsively throughout the supply chain is a challenge for Lean IT. Managerial control
can only be achieved through the flow of accurate information where it is required, and
when it is required. EDI is the most effective method of achieving direct transfer of data
between computer applications, in different parts of the supply chain, without any manual
intervention.
Why EDI? Why not e-mail or file
transfers?
The transfer of any data between applications requires an agreement by both parties.
E-mail is unstructured. While file structures can be agreed locally, the automotive
business has thousands of suppliers, supplying many different factories. These suppliers
and OEMs use systems that will always be different. Therefore, internationally prescribed
file transfer standards have been adopted. The internet still cannot handle the high
volumes demanded or guarantee the security levels provided by EDI. However, the internet
is emerging as a way for smaller companies to get EDI.
The anatomy of EDI
EDI is the interchange of data, structured in accordance with recognized EDI standards,
sent electronically between computer applications. Figure 1 illustrates the data transfer
bridges between organizations, and shows that they are comprehensive in nature. The
standards of EDI relevant to the Automotive Industry are:
- UN sponsored EDIFACT (Electronic Data
Interchange for Administration, Commerce and Transport) - US sponsored ANSI X12 (American National
Standards Institute) - European sponsored ODETTE (Organization for
Data Exchange by Tele-Transmission in Europe) - German sponsored VDA (Verband Deutscher
Automobilhersteller)
EDI standards parcel into messages by
coding in accordance with syntax (see Figure 2). Syntax is the punctuation, layout and
content rules used in the construction of the message.
EDI and Lean IT
For planning and preparation purposes, EDI is used to detail the forward schedules of
components required. These requirements are generated from the OEM’s Material Requirements
Planning (MRP) system on a weekly basis. This lengthy timeline enables the supplier to
procure the raw materials needed to support the program. The details show the planning
data of volumes and the execution data, which includes packing requirements and time of
delivery.
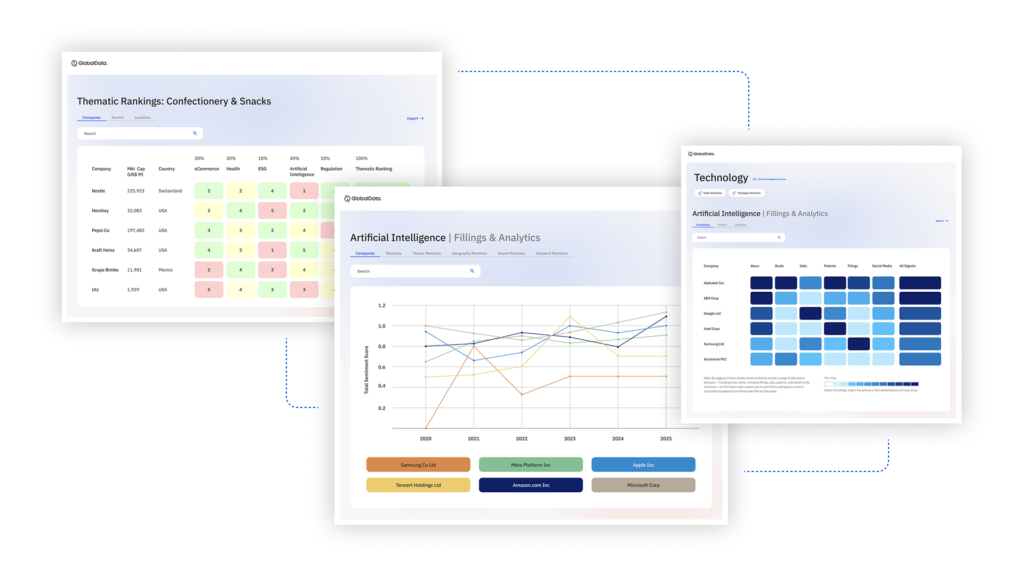
US Tariffs are shifting - will you react or anticipate?
Don’t let policy changes catch you off guard. Stay proactive with real-time data and expert analysis.
By GlobalDataThe move to make-to-order by OEMs is
facilitated by the use of EDI. The delivery call of a component/part in a coordinated way
is prompted by the vehicle assembly process or by a signal to replace some stock (such as
an empty bin or Kanban card). Using this data, an EDI message is broadcast every hour to
the supplier for the requisite quantity. By allocating a unique serial number for this
delivery call, the supplier labels the goods with this number for the OEM to account for
the delivery call upon receipt. Using specific locations, trackside deliveries are made
practical.
This solution completes the supply chain,
with the end-consumer at the head of the chain. This places great demands on data
processing and the communications network. EDI provides the means to connect the different
computer systems across a supply chain network with minimal fuss.
Labeling
Supply chain visibility relies on labels as vital elements in the ability to track the
movement of materials at all stages through their life cycle. By providing a unique
identification for the delivery call, a bar-coded label for the goods can be produced
that, when scanned, will automatically confirm receipt of the items. The comprehensive
nature of the labels requires many fields of data such as:
- consignee
- delivery address
- delivery call number
- number of packages
- weight
- product description (including product
classification) - supplier identity number
- unique serial number
- article number
- date of manufacture
EDI and administration
In an Industry of high volumes and repetitive transaction, the labor-intensive, manual
techniques for document transactional administration are eliminated by the use of EDI (see
Figure 4). However, a prerequisite for this is an ERP system that is capable of
integrating EDI messages routinely into its database files for seamless processing. The
billing and payment process for thousands of components is handled daily, effortlessly and
without error.
OEMs routinely receive the goods into their
system and can therefore generate an EDI invoice message. This is similar to getting a
credit card statement at the end of the month. The OEM produces the invoice and
automatically pays, based on this amount. The supplier can check and reconcile the amounts
within their own system.
Dispatch advice
For monitoring and control purposes, suppliers transmit ‘Advance Shipping Notes’ (as used
by Volvo). This dispatch advice informs a manufacturer that goods have left the supplier’s
premises and are in transit. From this, the OEM gets notice of any potential supply
pipeline shortages. Knowledge of goods in transit is practical as the dispatch advice
message is transmitted and received by the OEM before the truck arrives. Upon arrival,
this message, having been integrated within the OEMs system, facilitates a simple
receiving process without having to re-key the data.
As goods are prepared for transit, bar code
labels are attached. Corresponding transport documentation is also generated, including
any dispatch or delivery notes that may be required. Bar codes can be used for identifying
goods throughout the transport chain, including the check-off and check-in stages.
Conclusion
Prior to the introduction of EDI, paper schedules and information created a bureaucratic
nightmare. Without doubt, the initial adoption of EDI changed the capability of the
Industry to transmit and respond to schedule changes and remove the intensive labor levels
required for mundane administration. EDI generates documents automatically from a computer
application. These documents are then transmitted directly to the component supplier’s
computer via a telecommunications network. The whole procedure is electronic and avoids
manual processing, re-keying or checking of documents. With EDI, the cost of processing a
document is dramatically reduced, sometimes by well over 50 percent. Errors caused by
manual intervention and re-keying are avoided.
EDI can be viewed as an enabling technology
that facilitates computer- to-computer communications. It may be better described as a
component of ‘Advanced Communications Systems’.
OEMs used to mandate that to qualify as a
supplier, EDI must be adopted as part of the supplier process. This view has now been
modified to insist that EDI messages be automatically integrated and generated using the
supplier’s ERP system. Furthermore, Chrysler, Ford and GM have collaborated on the
development of a common set of EDI requirements, with mandatory implementation dates.
These are:
- Tier One suppliers will send Advanced
Shipment Notification to the OEM via EDI - Tier One suppliers shall receive planning,
shipping and sequencing messages via EDI and mechanically integrate these messages into
their ERP system - Tier One suppliers will transmit planning
schedules to the Tier Two suppliers at the least on a weekly basis - Tier One suppliers will have the capability
of sending daily delivery requirements to their Tier Two suppliers - Tier Two suppliers will use EDI to transmit
planning schedules no less than once per week
These mandates reinforce a strong
‘multi-level’ communications methodology between the Tiers of the automotive supply chain.
Therefore, a strong level of trust must be established throughout the chain.
Over-inflating requirements to ensure adequate supply is a common practice in the supply
chain and to a degree is system generated. However, most of this is a ‘protection’ buffer
against changes in demand and supply. The reality of EDI requires thorough planning using
ERP solutions that are capable of integrating EDI.
Strategies for Advanced Communications
The power of OEMs that force suppliers into the world of EDI can lead to a parochial
adoption of EDI, in order to eliminate paper and reduce cost. This misses out on the
opportunities to raise business performance substantially. As part of an overall strategy
for IT, EDI should be implemented and used to introduce new and improved methods of
working.
When exploited to its full potential, EDI
can facilitate new methods of conducting business, from ‘Just in Time’ (JIT) in the
production chain to concurrent engineering. A comprehensive strategy should define the
company’s ambitions. It should line these up with the Automotive Industry’s ambitions from
every viewpoint, from application and technical requirements to trading partners and time
scales. What is required is a strategy for advanced communications to ensure companies’
software is ready for the changes that are inevitable within the Automotive Industry.