The next five years will see major changes in the way OEMs source their doors. The trend is already strongly towards modular – and lightweight – designs. And the indications are that, in terms of modularity, doors are following the same development path as seats. Anna Kochan reports.
Two pioneering car assembly plants set up in the mid 1990s point the way to how car door supply systems are likely to develop in future. At Skoda’s sparkling new plant in the Czech Republic, which started Octavia production in 1996, the fitting out of the painted door was done alongside the main assembly line by an external supplier. The groundbreaking Smart plant at Hambach in France took an even more daring approach by contracting an external supplier to manage the entire construction of the door and deliver the fully-equipped structure directly to the assembly line, on a just-in-time basis. Within the next five years, a number of similar projects are due to come on-stream, according to the leading companies in the door supply market.
![]() |
Faurecia is breaking into German doors |
One of the first new phase of projects will start operating at an assembly plant in Germany (one of the Big Three) in early 2002. It is French company Faurecia, through its recent acquisition of Sommer Allibert, that has won the contract to supply and fit the door systems. Faurecia is setting up a new JIT facility alongside the German assembly plant specifically for this purpose. According to Norbert Bonhoff, development manager for door systems at Faurecia, the door will be taken off the car after it has been painted and be sent to the JIT plant via a conveyor system where Faurecia will put in the module and send the door back to the assembly line. “Not only will we fit the door module, but we’ll also assemble the mirrors and other components and mount the seal which seals the door to the body,” he says. “To win this contract, we had to validate all the materials and components,” he adds.
Faurecia’s solution for the German project involves a new style of door system backing plate. Conventionally, the components of a door system (window regulator, mechanism for raising and lowering the window, latch mechanism, loudspeakers, cable harness, and other components) are mounted on a metal backing plate. Faurecia’s, however, is an injection moulded plastic part, made from glass fibre reinforced polypropylene. Although this gives a 10-15 percent weight saving, there are other more important reasons for its adoption, as Norbert Bonhoff explains: “The injected moulded plastic has the potential for very high integration because it can be moulded to integrate clips and cavities and features that assist the assembly of other components as well as handling. As a result of the integration levels, the economics of a modular door become more attractive.”
![]() |
Smart Car possesses the capability to make the plastic external panels which are hung onto the metal frame |
The future, adds Norbert Bonhoff, will see further integration of components into the backing plate. The metal window guidance rails are one area being looked into. Faurecia, he says, is also working on making a ‘marriage’ between the door trim and the door module, to create a trimmed module that can almost be fitted as a single element. “This raises integration levels, making the door cheaper and increases the economic viability of a module.”
Norbert Bonhoff estimates that today when an OEM moves from conventional door assembly to door modules, the time to assemble the door falls from about 25 minutes to a maximum of 5 minutes because only one element has to be assembled rather than 10 or 15. In addition, materials handling is reduced. Although the cost benefits may seem obvious to a supplier such as Faurecia, not all OEMs are quite so convinced. Norbert Bonhoff reckons that, in Europe, two out of every three new models are launched with doors that incorporate modules. “It varies from OEM to OEM. About half of all car doors in Europe are now assembled in this way, and the percentage is increasing. With increasing model diversity, modularity becomes more and more attractive,” he comments.
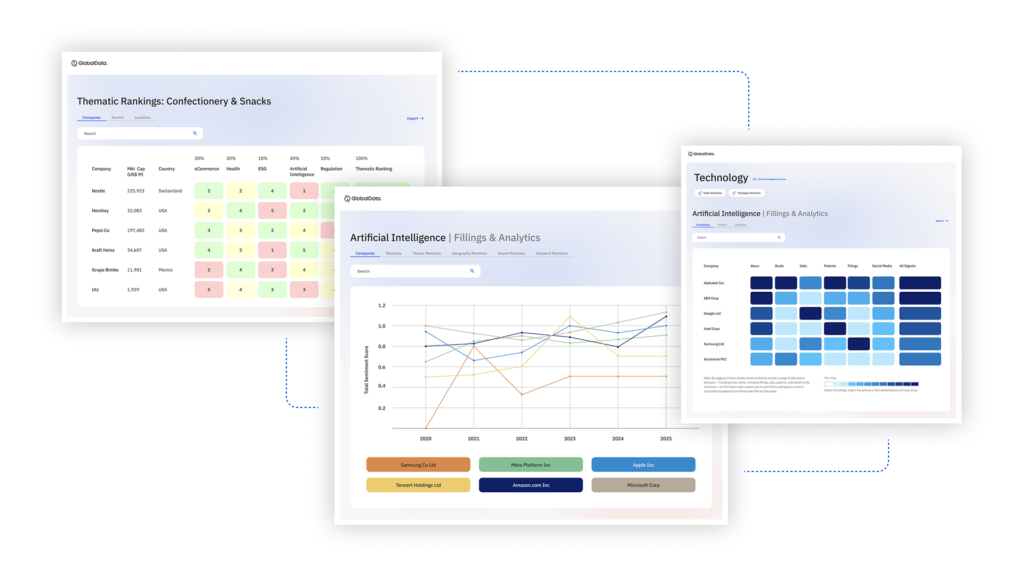
US Tariffs are shifting - will you react or anticipate?
Don’t let policy changes catch you off guard. Stay proactive with real-time data and expert analysis.
By GlobalDataNorbert Bonhoff does not rule out the possibility that Faurecia will take on projects to develop complete car doors, including the metal structure. This, he says, will be done in partnership with a specialist for the metal structure. However, Faurecia may find itself with a greater role to play in those sectors of the market that are likely to follow the trend set by the Smart car as Faurecia possesses the capability to make the plastic external panels which are hung onto the metal frame.
The French company is indeed already working on pre-development projects for complete car doors and could move into the full development phase of a volume car door for a customer by the end of this year, says Norbert Bonhoff.
![]() |
ArvinMeritor is more ambitious than most in its plans for future door projects |
ArvinMeritor, the Meritor part of which was created through a spinoff of Rockwell International’s automotive business, also has ambitions to take on complete door projects. It was, in fact, Rockwell which originally won the Skoda contract. And, it is ArvinMeritor which continues to operate it. Now ArvinMeritor is pursuing further contracts of a similar nature that should be running within five years, according to Robert Marty, vice president and general manager, door systems. “The OEMs have been offloading more and more of the door assembly activity over the years. It is an evolutionary process that started with components, moved on to modules and is now starting to encompass the whole door. We are seeing more and more OEMs moving in this direction, particularly in non-union labour-intensive production environments,” he says, adding that South America is one region where a supplier has already been contracted to take responsibility for the complete door, from stamping to painting to assembly and trim. The main advantages of building doors off-line include a major reduction in quality problems and in warranty problems, he says. But economics also come into the equation. “Everyone is looking to reduce investment in capital equipment and tooling and to improve their return on net assets. It is both a financial and quality decision.”
ArvinMeritor is more ambitious than most in its plans for future door projects. Robert Marty believes that, within a five-year time frame, his colleagues will have made the technological advances necessary for the company to supply a colour-matched painted door. The new door structure will benefit from the results of a project ArvinMeritor first revealed about one year ago (See WAM March 2000) which aimed to develop colour-matched roof modules. The roof module was proposed with an aluminium, steel or plastic outer skin, to which paint wass applied with a film carrier by a coil coating method. The company claimed that the surface quality of the paint could be even better than sprayed paint. “Working with Dupont, we found that matching colour was doable,” said Heinrich Wied, director of engineering at Meritor Light Vehicle Systems.
![]() |
Wagon is another supplier that is actively pursuing contracts for complete door projects |
If the ArvinMeritor approach to colour-matching meets with success then, like the complete door solution used on the Smart, it would avoid the need to paint the door with the vehicle body. French company Ymos, that won the Smart contract in 1995, has since been acquired by Wagon which is another supplier that is actively pursuing contracts for complete door projects. However, Axel Schulmeyer, managing director of Wagon Automotive, believes that the colour-matching problem means that the OEM will still be responsible for painting the door, at least for upper segment vehicles. The mass production segment, though, could still go the Smart way, he adds.
As well as Faurecia, ArvinMeritor and Wagon, others such as Dura Automotive and Oxford Automotive are also competing for the new wave of complete door system projects in Europe. Having taken over the German company Schade, two years ago, Dura has acquired an expertise in body-in-white door construction. As a result, it too is now in discussion with an OEM for a complete door project. “This is a project whereby we would manage the development and sourcing of all the components, including the structure, the interior parts and the trim,” says Burkhardt Vogt, research and development manager with the body and glass division, based in Plettenburg, Germany. It has not been decided yet whether this will be done from a supplier park or from within the OEM’s assembly plant.
A final contender in the market is US company Oxford Automotive which has recently announced a joint development agreement with Johnson Controls to formalise initiatives already under way to design and develop modular door integration solutions including full-door system solutions.
More than 18 months ago, Oxford Automotive and Johnson Controls collaborated on an integrated door system that was displayed at the 2000 North American International Auto Show. Johnson Controls had designed and developed the trim and hardware module for the door while Oxford Automotive had optimised the sheet metal door structure, adding strength and reducing weight. “This relationship will enable Johnson Controls and Oxford Automotive to develop, manufacture and deliver complete door systems ready for installation on a vehicle,” said Steve Abelman, president and CEO of Oxford Automotive. “We view supplying door systems as ‘evolutionary’ not ‘revolutionary’,” added Lou Kincaid, group vice president, product and business development for Johnson Controls. The two companies believe that their door system designs could ultimately result in reduced cost, complexity, weight and warranty issues to OEMs. According to Kincaid and Abelman, optimising the door structure will not only increase automaker throughput, but it also will provide the opportunity to reconfigure conventional packaging space.
![]() |
Johnson Controls and Oxford Automotive have recently announced a joint development agreement |
The OEMs which are more likely to opt for the most comprehensive form of door supply system are those which are not already well equipped with press shop capacity. According to Dura’s Burkhardt Vogt, “If customers have existing infrastructure then they tend to follow their current strategy. But if they are building a completely new model in a completely new plant, then they inevitably think about how to reduce assembly lines and cut down on workforce. They then start to look at more and more modules.” Conventional stamped doors are mainly the core competence of the OEMs, he adds, indicating that the greatest potential for the supply industry is where structured doors are concerned.
Often made up of a combination of extruded profiles, die cast components and pressings, structured doors are today witnessing a very strong trend away from steel and towards aluminium. Wagon is the pioneer in this area, having supplied aluminium door sub-assemblies for the last 15 years. Uptill now, the major customer has been Audi. Now, however, Wagon has won the contract to supply body-in-white door structures for Jaguar’s new aluminium vehicle, the X350. Axel Schulmeyer says that the Jaguar door will be different from anything Wagon has supplied before. “We have come up with some unique ideas,” he claims. Press reports have described the door as having a spaceframe structure.
It is in the medium to luxury segment where the trend towards aluminium is strongest, according to Axel Schulmeyer. From a total cost point of view, the Wagon approach is a solution for low volume vehicles, he explains. “In particular, it saves on press tools, which are very costly to make.”
![]() |
Dura is also finding a niche in the market for body-in-white structures for aluminium doors |
Dura is also finding a niche in the market for body-in-white structures for aluminium doors. The company’s first project for a 100 percent aluminium door structure, including internal and external panels, will be revealed later this year when the car they will be fitted on is launched. And, adds Burkhardt Vogt, “we have a lot more projects under development that are based on aluminium.”
Ford in the US is also anticipating using aluminium on doors in the not-too-distant future, according to Andy Herbert, plant manager at Ford’s stamping plant in Hamburg, New York. “In North America, our doors today are still all steel. We do, however, see a movement towards aluminium for the entire door in the future because of weight reduction factors,” he comments. The earliest that such technology could be introduced would be on 2005 models, he adds.
The cost and the ability to execute a manufacturing process are the factors holding back the aluminium door today, according to Earl E Kansier, vice president of engineering and program management, at the Budd Company’s Stamping & Frame Division in the US. “Within the next five years, we do expect to see complete doors made in aluminium because of the interest that there is from the OEMs,” he comments.
It is clear that Europe is far ahead of North America, both in the way that aluminium is being adopted on door structures as well as the uptake of modules for door assembly.
Magnesium is a material that will definitely help to reduce the weight of doors further in future. Wagon recently demonstrated that it had developed a technique for welding magnesium, thereby moving one step forward towards its adoption as part of the structure. Dura is also developing applications with the material.