What do shock absorbers do?
The term ‘shock absorber’ is a misnomer because the device does not, in the strictest sense, absorb shock at all. The shock absorber is designed to dampen the movement of the springs—be they coil, leaf or torsion bar—limiting the road shock transmitted through the tyre, wheel, hub and spring mount. Bushings absorb the rest. The spring must also support the weight of the vehicle. The sole purpose, however, of the more accurately named ‘damper’ in any suspension system is to control the spring’s oscillations. If they are damped, the tyre is able to stay in contact with the road surface. The net result is a more comfortable ride, precise handling, efficient braking and smooth acceleration.
How do they work?
There are many types of shock absorber, but the most commonly used work with hydraulics (oil). There are two examples of this type—mono-tube and bi-tube. The low-pressure gas type, launched in 1985 by Monroe as ‘Gasmatic’, combines the features of both.
In the bi-tube, oil is forced by the piston into a reserve tube through a series of compression valves. Since this requires considerable force, there is resistance to any rapid movement and the bouncing movement of the springs is dampened. The bi-tube shock absorber is found on 90% of vehicles today. It can be adapted to all suspension types (conventional and strut) and increases resistance to external influences.
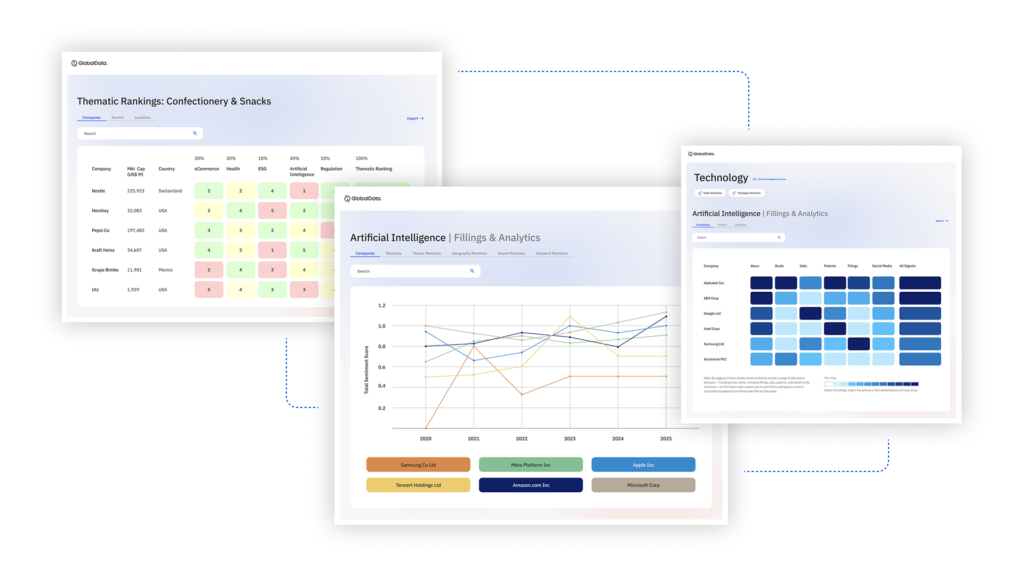
US Tariffs are shifting - will you react or anticipate?
Don’t let policy changes catch you off guard. Stay proactive with real-time data and expert analysis.
By GlobalDataIn the case of the mono-tube the reserve tube is replaced by a high-pressure cushion of gas, which is compressed to make room for displaced oil. Bump and rebound is controlled by valves in the shock absorber pistons. The main advantage of the mono-tube shock absorber is that it can operate in all directions: horizontal, vertical, head at the top and head at the bottom. On the other hand, it is more susceptible to wear and more fragile than a bi-tube shock absorber. The rod on the bi-tube shock absorber is actually protected by an interior tube and runs less risk of deformation caused by shock.
|
The Monroe gasmatic is a twin tube design, but the reserve tube, instead of being at atmospheric pressure, is sealed under a low-pressure cushion of gas. The twin tube cycle is thus modified in that oil quickly flows back from reserve to compression tube, reducing the risk of air bubbles forming.
Superior ride control is governed by a vehicle’s suspension system, including its shock absorbers and struts. Shock absorbers and struts help maintain vertical loads placed on a vehicle’s tyres to help keep the tyres in contact with the road. A vehicle’s ability to steer, brake and accelerate depends on the contact between the vehicle’s tyres and the road. Worn shock absorbers and struts can allow excess weight transfer from side to side, which is called ‘roll’, from front to rear (‘pitch’) and up and down (‘bounce’). Variations in tyre-to-road contact can affect a vehicle’s handling and braking performance and the safe operation of a vehicle. Shock absorbers are designed to control vertical loads placed on tyres by providing resistance to vehicle roll, pitch and bounce. Thus, by maintaining the tyre to road contact, ride control products are designed to function as safety components of a vehicle, in addition to providing a comfortable ride.
What is driving innovation?
A number of companies have been developing active suspension systems that would give a perfect ride whatever the road conditions. The problem with developing a genuine active suspension is the system’s high power consumption and cost. Both Citroën, who have the Activa system, and DaimlerChrysler have come close to the concept of active ride, while the latest Land Rover Discovery has an active roll control system. Mercedes-Benz has spent 20 years developing their ABC (Active Body Control) system that will appear on the Mercedes-Benz CL coupé. Mercedes abandoned the idea of a full active ride control and developed a system with limited authority in terms of frequency response and wheel movement to reduce power consumption and cost. With ABC, the hydraulic system only controls suspension movements at a rate of up to 5Hz, conventional shock absorbers and coil springs are used for higher-frequency vibrations. ABC is said to reduce body movements by up to 68% when starting from rest, cornering and braking. The Lotus Active Suspension system, which has been used on experimental cars, is one in which springs and dampers are replaced with high bandwidth electro-hydraulic actuators under digital control. Meanwhile, the MagneRide system developed by Delphi uses magneto-rheological (MR) fluids and valveless dampers instead of more expensive electro-mechanical valves. The system can achieve a much broader damping range and respond more rapidly without generating noise. MagneRide will be seen on production vehicles from 2003.
What are the latest technical advances?
There have been some advances made to shock absorbers which may be referred to as trends. Notably, the increasing use of aluminium in shock absorbers used on luxury vehicles with MacPherson struts in an effort to reduce weight. Manufacturers claim that by using aluminium instead of steel, they can shed 20-30% of the shock absorber’s weight. To improve ride comfort without adding to cost, manufacturers are creating a longer shock absorber movement. Some up-market passenger cars are also being fitted with electronically assisted pneumatic shock absorbers.
In March 2002, ArvinMeritor’s Commercial Vehicle Systems Ride Control division launched its new Gabriel electronic stability control system and load-sensitive pneumatic adjustable shock absorbers, both designed for North American heavy-duty applications. Manufactured at the company’s production facility in Toronto, Canada, these systems are being offered to North American vehicle makers. The company’s new shock absorber allows the air spring pneumatic pressure to automatically optimise damping under varying load conditions. In addition to providing improved vehicle handling and driver comfort for different load conditions, it isolates road inputs from the vehicle’s chassis and reduces the possibility of vibration damage.
Beginning with the 2003 model year, Ford Motor Co sports utility vehicles will go to an integrated shock-and-spring module to be assembled by PASA Modules LLC, the joint venture between Piston Automotive and Sachs Automotive. Sachs and Ford will be involved in the module design/engineering work and PASA will carry out the manufacturing/ engineering. A shock module would mean better tuning ability and a lower vehicle step-in height via the altered suspension geometry.
‘Green’ shock absorbers
Tenneco Automotive (Monroe) recently introduced its ‘green shock’, a new oil-free shock absorber. Since there is no use of oil, it is not temperature-dependent and the green shock absorbers can be mounted in any position. The product, which is undergoing validation confirmations through durability testing in the lab and on the road, is expected to be released in the market in the 2004 model year.
‘Off-road’ shock absorbers
For off-road vehicle applications, Monroe also recently introduced a new aftermarket shock absorber for all-wheel drive vehicles named the ‘Adventure’. The Adventure is said to be capable of delivering off-road performance without sacrificing on-road capability. The mono-tube design allows maximum airflow to the shock absorber to reduce the heat that commonly reduces the performance of liquid dampers, by losing rigidity, reducing rebound damping and damaging seals. The design also allows the use of a larger than usual piston which is more sensitive to wheel movement, with a further floating piston that separates the oil from a chamber filled with nitrogen pressured at 360psi. This arrangement eliminates contact between gas and oil, which conventionally results in foaming and uneven operation. During the compression stroke the man piston reduces the area available to the oil which compresses the nitrogen; on the rebound stroke the piston rod moves out again and the gas gently pushes the floating piston back.
Japan’s Unisia Jecs has also developed a new shock absorber that absorbs all vibrations that conventional hydraulic shock absorbers cannot control. A rubber ring is fitted inside the piston cylinder and when the piston is moving slowly, friction created by the rubber ring absorbs tiny vibrations and when the piston movement is faster, the rubber ring stops producing friction and enables conventional hydraulics to work.