Mahle Powertrain, formerly known as Cosworth Technology, is to refocus on niche engine production and engineering services, signalling a major change in the British supplier’s strategy. Julian Rendell hears about the new company’s capabilities and plans.
The company has two factories – a casting facility in Worcester and a machining and assembly facility in Wellingborough – that will concentrate on low-volume and prototype business.
Wellingborough can make up to 100 engines per day – 24,000 a year – on two separate lines. While Worcester can cast up to 20,000 heads and blocks per day on one line, a second line is limited to just 2000 engines for specialised or prototype applications.
Together with 400 engineers based at its Northampton HQ, Mahle Powertrain will try to fill capacity at its two factories with complete engine programmes – design, calibration, certification and manufacture – particularly from developing countries.
“All the OEMs are loaded with product development work and they need more and more turnkey solutions,” says Prof Heinz Junker, Mahle Group Chairman.
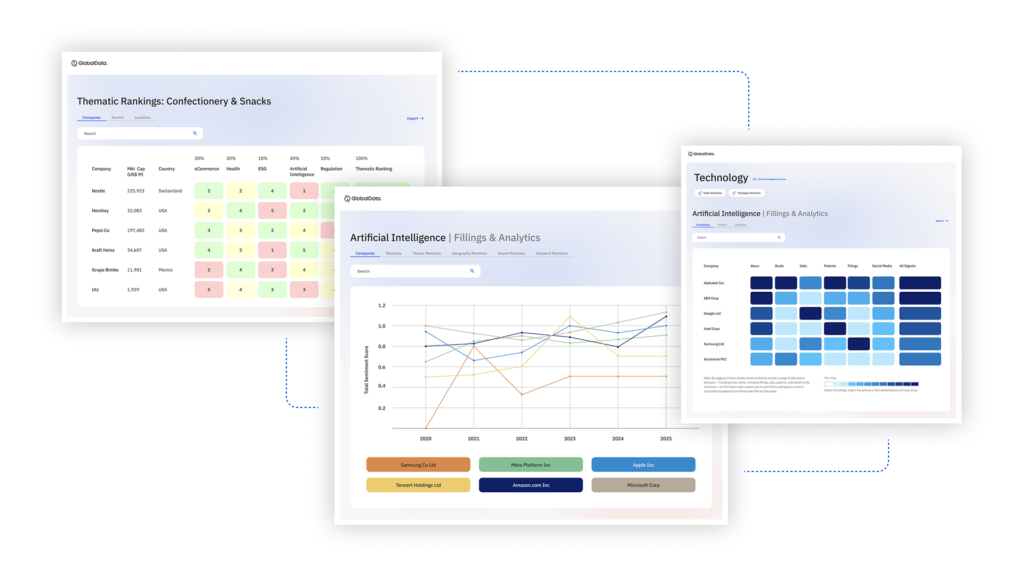
US Tariffs are shifting - will you react or anticipate?
Don’t let policy changes catch you off guard. Stay proactive with real-time data and expert analysis.
By GlobalData“We’re confident of announcing at least one major new project very soon, maybe in a month or so’s time,” he adds.
With 70 production plants on four continents, 38,000 employees and sales of 3.76b Euros in 2004, Mahle Group is a top 30 global supplier. It also claims to be the number one in engines and powertrains.
![]() |
Prof Heinz Junker |
The company bought Cosworth Technology from Audi in January and has spent six months formulating a strategy for the business. It bought Cosworth Technology for two main reasons – to fulfil increasing global demand for engine and powertrain engineering and to increase its workforce of skilled engineers to bid for third-party engineering work.
But Cosworth also has skills in calibration and electronics and its casting factory and assembly lines can be tied-in with Mahle’s Product Line Valve Train Systems to offer a complete cylinder head module.
However, because the Cosworth name wasn’t part of the deal – it belongs to the motorsport-business Cosworth Racing bought by US entrepreneur Karl Kalkoven – the name was changed on July 1 to Mahle Powertrain.
Under Audi’s ownership, Cosworth started the process of concentrating on low-volume manufacture by closing a high-output, low-pressure aluminium casting facility, Cos IV, with a capacity of 250,000 units a year, taking the company out of mainstream Tier1 component supply.
Currently Mahle Powertrain is searching for projects to replace capacity lost as major contracts with VW, Audi and Ford finish. Mahle is assembling 12,000 VW group 2.8-litre V6 engines a year, mainly for the Skoda Superb and also makes V12 blocks and heads for Aston Martin’s flagship supercar, the Vanquish, but only in limited numbers.
![]() |
Aston Martin V12 engine |
Full-time assembly of the V12 engine has been transferred to a new Aston Martin factory in Ford’s Cologne plant. However, Wellingborough continues to assemble and supply aftermarket replacement V12 engines.
Mahle Powertrain’s other main piece of business is an oil-pan assembly with balancer shafts for Ford’s 2.3-litre engine.
Contracts to assemble the Audi RS4/RS6 V8 and twin-turbocharged V6 at a rate of about 5000 per year and Ford Focus ST170 engine have both stopped, leaving spare capacity.
Mahle also faces an end to royalty payments from licencees of its patented low-pressure casting technique, developed in the mid-1980s. The patent runs out in 2007.
One supplier in Windsor, Canada is currently making up to one million castings a year with this manufacturing technology.
“Output is stagnant,” admits Junker, “but in the last six months we are already getting significant customer interest for new business.”
Although Audi kept its business with Mahle after the sale in January, it didn’t sweeten it with guarantees of new business. “If we want to win more business from Audi, we’ll have to win it in open competition,” says Warren Roberts, manufacturing director.
Mahle will also hope to get a big increase in engineering consultancy work for its 400 engineers. When Vickers owned Cosworth before it was sold to Audi, the company had a successful third-party engineering business.
But Audi’s ownership frightened other OEMs from putting contracts the company’s way, because of fears that technology would transfer to a competitor. “In the past it was impossible to get independent engineering contracts because of the links with VW Audi,” says Junker.
Junker also says Mahle plans to re-organise its R&D skills between the UK, Germany, the US and Asia. Some R&D engineers will move to the UK and some move out: “We’ll transfer certain activities. But we’re lucky that the UK and other operations use the same software tools.”
The details of this re-organisation are currently being finalised as Mahle prepares its 2006/7 R&D budgets.
“We feel we want to do more in-house R&D,” says Junker, “and the Cosworth acquisition will help with advanced engineering and our long-term strategic approach.”
The most successful Tier 1 suppliers, like Bosch, have pioneered technological breakthroughs that then open-up into huge supply contracts for high-value components.
Another development that is certain, is more business for Mahle’s UK dyno test cells, which will get business transferred from other Mahle companies. “We didn’t have enough capacity in test cells,” says Junker.
In the future Mahle will also look at more diesel technology and transmission.
The price paid for Cosworth Technology in undisclosed and although of strategic value, the company has yet to give Mahle’s bottom-line a major boost.
![]() |
Piston Manufacturing |
Mahle has had five very good years, sales rising from 2.39b Euros in 2000 to 3.76b in 2004. It forecasts 4.00b Euros for 2005.
In the same period, its spread of business has widened, too. In 2000, it generated 66 per cent of its revenue in Europe, 32 per cent in the Americas and just two per cent in Asia and the Rest of the World.
Last year Asia/ROW grew to 16 per cent and the Americas to 32 per cent, while
Europe dropped to 59 per cent
Asian business is likely to increase further with the Cosworth Technology acquisition.
“There’s a huge part of customer interest coming from the Asian region, including China, for engine and powertrains,” says Junker.
Last year, Mahle built its first complete engine, a three-cylinder race car unit, as a showcase for its technology.
Julian Rendell