In October 2000, Ford launched an all-new Mondeo at its assembly plant in Genk, Belgium. Ford of Europe chairman Nick Scheele commented, “The significance of the new Mondeo to the future of Ford Motor Company here in Europe cannot be overstated.” Analysts and journalists, optimists and pessimists alike all agreed. But the Mondeo’s success isn’t just crucial to Ford. There are suppliers to think of, as well.
“Here’s the deal. We really like you. You’re both good suppliers. But we want you two to form a joint venture to build this enclosed conveyor bridge. In fact, we want you to invest 25 million Euros of your own money to fund the project. See, this conveyor is much larger than anything we’ve ever done like it before. We want it to run between the facilities in the new supplier park behind our plant and the assembly hall. Besides paying for it and building it, however, we want you to run it. That’s right, it will deliver 35 different parts from four different suppliers, just-in-time and in-sequence for this redesigned model we’ll be producing. For your efforts, we will pay you-but only on a per-piece basis for every car that we produce. And we’ll give you no guarantee as far as volume and duration of this contract beyond 12 months. So what do you think? It sounds great, doesn’t it!?”
![]() |
The conveyor bridge as it was nearing completion. The structure snakes along for 900 m, from the supplier park to the assembly plant. It contains 8,000 m of track, elevated six meters from the ground, with 101 switches for routing. Thirty-five different parts are transported on 477 carriers, from eight collection points to 23 drop-points within the assembly hall. |
Vis-à-vis
Consider that CSG is handling 35 different parts in Genk, while a similar conveyor bridge in Saarlouis delivers just six. Furthermore, the CSG conveyor is twice as long as the one at the German facility. The parts being transported in Genk include such diverse modules as engines, IPs, front corners, cooling modules, headliners, door panels and seats from suppliers Lear, Textron, SML, and TDS-Essers. Each supplier has purchased space in Ford’s supplier park, but as part of its agreement, the supplier will be forced to sell if its contract with Ford is cancelled. That said, suppliers are not restricted from supplying other non-Ford plants from their facilities.
The point here is that the supplier park and its dedicated material handling system have gone from being something of a trial for Ford to a full-blown strategy. And if suppliers like CSG-a company that exists solely to carry Ford’s burden of infrastructure investment and logistics-are willing to sign up for a contract that guarantees them little-to-nothing, what does that mean for component suppliers? Prepare to risk more on future vehicle programs. . .and just hope that you’ll be able to share in their success.
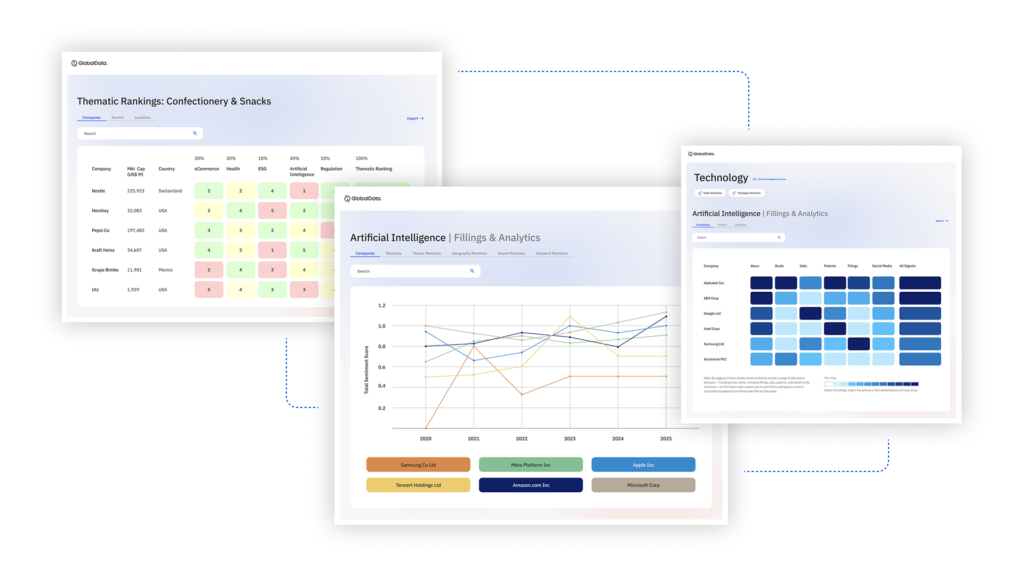
US Tariffs are shifting - will you react or anticipate?
Don’t let policy changes catch you off guard. Stay proactive with real-time data and expert analysis.
By GlobalDataThis is an example of the carrier, or “hanging frame” used to transport parts from suppliers’ production lines for Ford’s 45-second cycle time. Ford retains ownership of 80% of these carriers, while the other 20% belong to the suppliers. In order to ensure reliability, controls and electronics for the system of track is localized, such that portions of track can operate independently during maintenance or in the case of a breakdown.
Lean?
While the initial impression of this monstrous conveyor system might lead one to the conclusion that it’s a bit much (Why not deliver the parts just-in-time and in-sequence with a less-costly, more flexible solution, like, say, trucks?), operations manager Dennis Profitt would disagree. Ford Genk has been consolidating and localizing its supply base to reduce storage space, inventory, and material handling while allowing faster resolution of capacity and quality issues. Hand-in-hand with this initiative, Proffit says that his team looked at a multitude of ideas for better integrating suppliers’ operations with the assembly line. (Among them, Ford even considered moving suppliers into the assembly plant, however, this plan was dismissed as being “too much of a bite at one time,” largely for-you guessed it-labor relations reasons.)
Profitt explains that in the transition to more JIT and in-sequence parts, it’s often very difficult to maintain the discipline necessary to make these systems work. The conveyor imposes its own discipline. Even more so, the conveyor system solves a rather complicated logistics issue: even if parts were to come in via trucks or some other more flexible delivery system, getting them to the line in the right spot would be problematic and involve its own material handling cost. The point is, Ford Genk (est. 1964) wasn’t really designed for line-side delivery as many newer assembly plants are. Thus, says Proffit, the supplier bridge makes lean sense. That is, at least for now.
The Almighty Euro
The obvious key to the decision to build the conveyor bridge was the fact that it isn’t costing Ford anything up front. Surely, Scheele, Proffit, and Company love the idea that they’re protected from investment risk and certainly don’t mind sharing their piece of the booty if the Mondeo does well. CSG, of course, figures that the Mondeo, once one of the best selling cars in Europe, will be a cash cow, as skyrocketing demand will cause production to increase, meaning more money for it.
But in talking about production levels and capacity at Genk, Proffit explains that one of the mistakes Ford made with the first-generation Mondeo was to pump out too many, too soon. He says that Ford had little chance of keeping demand for the vehicle high in the later years of the program because there were just too many three-year old used Mondeos kicking around. Part of Ford’s strategy with the new version is to level production to keep demand up for the life of the program. What this means for CSG, which gets paid only as the vehicles are built (Ford calls it “POP,” Pay on Production), is that it’ll be carrying its investment longer. Instead of earning much of its money in the first couple years of “overproduction,” its payments will be spread more evenly over the duration. However long that might be.
By Jeff Sabatini, Instigator
![]() |
To link to a related feature article, please click here.
To view related reports in the just-auto.com Knowledge Store, please follow the links below:-