Every three years, the (former) Big Three
and the United Auto Workers negotiate a new “pattern” contract. The current
contract expires September 14, and the vehicle manufacturers are now negotiating with the
union which represents 388,500 of their employees.
It has been a very good year for the
industry, with record sales and record profits — and record salaries for automaker CEOs.
Understandably, the union sees little reason for a cutback in the workforce.
As in past years, the primary goal of the
UAW this year is to stabilize and, if possible, increase union membership. The UAW (see
table) has been shrinking for the last two decades. The percentage of auto assembly
workers in the US who are members of the UAW has been declining ever since the Japanese
vehicle manufacturers set up shop in North America with non-union labor. And while
employment in parts-making suppliers has increased by 40,000 people in the last twenty
years, the actual number of workers in vehicle and body assembly has fallen.
The UAW’s position is that it has been
losing membership recently because of out-sourcing from unionized workplaces to
nonunionized suppliers paying substandard wages.
According to the UAW, unionization is not
only good for unions; it’s good for business. The union cites a study that indicates that
unionized firms are 16% more productive than non-unionized firms. Further: that companies
which have installed joint labor-management quality programs — as at the three majors —
achieve 210% better productivity than non-union firms without the programs. Therefore, the
industry needs more, not fewer unionized workers.
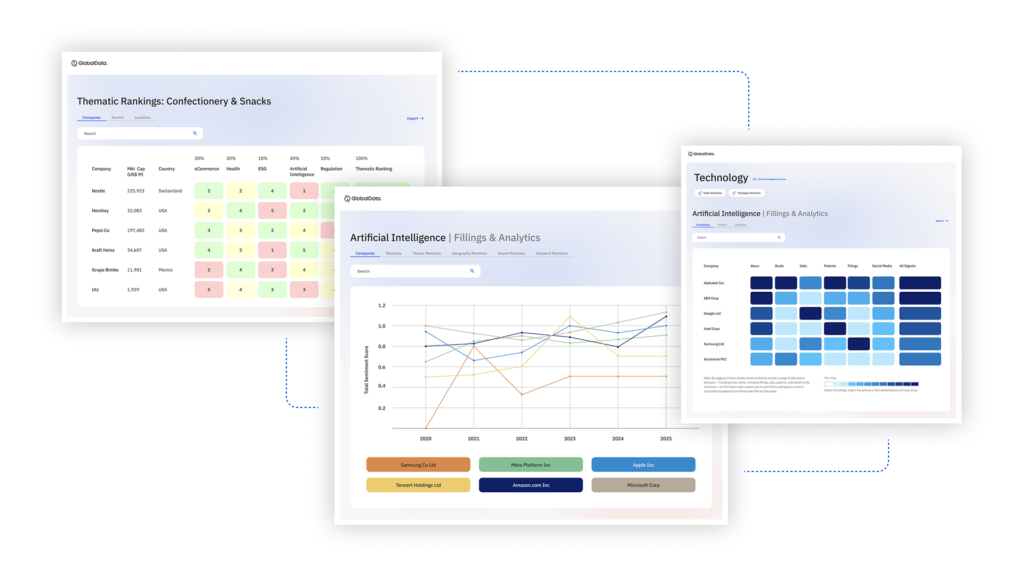
US Tariffs are shifting - will you react or anticipate?
Don’t let policy changes catch you off guard. Stay proactive with real-time data and expert analysis.
By GlobalDataThe companies’ position is that their
payroll is too big to be competitive. Today, they still lag the Japanese and NAM assembly
plants in efficiency, because compared to their transplant counterparts they are still
overstaffed by tens of thousands of workers. And they point out that it is no coincidence
that its record profits are occurring during the country’s longest postwar economic boom.
This year’s record profits cannot be sustained: the automotive industry has a record of
being very cyclical, and a large “war chest” of cash during good times allows a
company to better survive the lean times that inevitably follow. All three corporations
ran into tough times in the early 1980s and again ten years later; two of them nearly
filed for bankruptcy. As the VMs see it, if they are not allowed to make money now, how
can they be expected to keep employees when times are tough?
Despite their fundamental disagreements,
negotiations between the VMs and union have proceeded politely this year, probably due to
the booming auto market and a strong disinclination of both labor and management to
disturb the party. Both sides now seem to have come to the conclusion that the Flint GM
strike solved nothing and helped nobody. GM lost money and (at least temporarily) market
share, while the UAW lost wages and perhaps credibility.
As before, the UAW’s strategy is to work
toward a pattern contract with the VM with most to gain from continued labor peace. For
the last two contracts it has been Ford. UAW saw Ford as the most cooperative of the three
VMs, and Ford, for its part, saw distinct competitive advantages in trying to tailor a
pattern contract to its own advantage (and to the disadvantage of GM).
WHO’S IT? It is not clear
at this writing which VM will be the pattern target. Until recently, Ford seemed like the
odds-on favorite to lead the negotiations with the union for the third consecutive time.
Recently, however, DaimlerChrysler has emerged as a contender, with 69,400 workers under
its UAW contract.
DAIMLERCHRYSLER. DC does
have some flashpoint issues with the union. DaimlerChrysler has reduced the number of
parts and systems it produces in-house and moved these jobs to suppliers, typically
non-union. Ford and GM have done this too, but not to the same extent. High on the UAW’s
list of demands is unionization of the Vance, Alabama, Mercedes-Benz plant and the
Gastonia, North Carolina, Freightliner plant, both of which were part of the Daimler-Benz
empire before the merger. Since both plants are in the anti-union South, and their workers
are paid very well, any attempt to unionize them by negotiation faces formidable
obstacles. DC may well decide to keep them union-free, but nobody expect the issue to be a
permanent obstacle to a settlement with DC.
DC’s chances were hurt when the UAW’s chief
DC negotiator, a man highly respected by both sides, died suddenly. Nevertheless,
DaimlerChrysler would be comfortable setting the pattern contract. It operates with a
relatively slim workforce. It is used to bargaining for tough contracts: Daimler
negotiators convinced IG Metall to streamline its German operations, for instance. Also:
DaimlerChrysler is the only automaker to add jobs since the last contract was negotiated,
and the only one to have a UAW representative on its board — something the union wanted
in its last two contracts.
FORD. In addition to
playing host to the UAW for the past two contracts, Ford continues to have the best
relations with the union of the three majors, thanks to Ford’s recent support of the UAW
on supplier issues. In fact, Ford’s last strike was more than a decade ago.
The wild card is Visteon. Current industry
thinking has Ford preparing to unhook its captive supplier and merge it with Lear. Were
things to remain the same at Visteon, that is, if it remained a unionized supplier paying
VM union scale, the problem wouldn’t exist. But the UAW fears losing membership and good
wages. It received a strike authorization vote on August 17 on the Visteon issue.
GENERAL MOTORS. GM remains
as the UAW’s least likely target for these negotiations. In the automotive doldrums of the
early 1980s, Ford and Chrysler downsized their workforce, and because of the extremely
weak auto market at the time, the UAW had no choice but to go along. GM, however, saw the
potential to grow market share at Ford and Chrysler’s expense, and kept its headcount
high. According to current thinking, GM now needs to shed 50,000 more workers to be as
competitive as the most efficient automakers. Therefore, in spite of the fact that GM,
chastened by its damaging Flint strike, is seriously trying to improve its labor
relations, workforce reduction remains a very serious potential obstacle for GM-UAW peace.
While unionization of DC’s Southern U.S.
plants, Ford’s Visteon and GM’s Delphi are particularly crucial issues, there are four
general issues on which these negotiations will turn: outsourcing, modularity, layoff
insurance and overtime.
I. THE SOURCE OF TROUBLE.
The one issue where union and automakers are sure to lock horns is outsourcing, for which
the UAW saved its longest and most detailed list of demands. The union seeks to prohibit
any outsourcing and subcontracting without mutual agreement, and then only if the work is
fully replaced by new or additional work with no net loss of jobs. Its list of demands
also includes VM commitments that work won’t be moved from UAW to non-UAW suppliers, that
work lost to market-driven reduction is replaced by insourcing work that was previously
outsourced, and that VMs won’t whipsaw local unions into bidding wars for product
allocations.
Since it probably realizes the outsourcing
can’t be completely stopped, the UAW wants to organize the workers at Tier 1 and 2
suppliers. Visteon and Delphi, with their inherited Ford and GM contracts, seem to be the
perfect starting point for this move. The two captive suppliers have been covered under
the VMs’ contracts, and now need to negotiate their own contracts.
Similar to the problems GM has faced
recently, Ford anticipates troubles with the spin-off of Visteon Automotive Systems. But
there is a difference. The spinoff of Delphi by GM has so far been handled amiably because
both company and union were motivated to make it succeed. The safety net agreed to is
broad and deep, guaranteeing pensions plus first crack for Delphi people at new openings
at GM.
Visteon negotiations may not be so smooth.
The UAW is concerned that any arrangement outside the Ford contract would inevitably
reduce membership and cut wages. The UAW wants to cover Visteon under the same contract as
Ford. According to Ford, that could potentially make Visteon less competitive in the free
market, once the supplier pushes for more non-Ford clients, competing with lower-cost
non-union suppliers, not to mention suppliers in developing markets.
II. MODULE BUILDING.
Publicly, at least, the union is unequivocal in its view of the modularity trend: for the
UAW, modular assembly is simply another word for outsourcing, and a way to destroy
high-paying jobs and benefits.
Modularity is an especially explosive issue
at GM. Its plan to become more competitive included until recently the “Yellowstone
Project,” as the key element in its future factory development. Under this plan, GM
would move more of its vehicle assembly down the supply chain to (presumably) non-union
suppliers in the form of “modules,” which would be delivered to the GM plants
and assembled into a full vehicle, thus requiring fewer UAW members at GM to produce the
same number of vehicles. GM claims the approach will lower costs and increase flexibility.
The union is afraid modularity is the “same old low-road strategy” to use
low-wage, nonunion suppliers. Its (present) position is that modularity would hurt both
the corporation and its workers in the long run, costing both UAW jobs and corporate
profits — especially if the automaker loses control over vital design, engineering and
production processes which could compromise quality in the name of cost.
But it is possible that the union — in the
face of general industry opinion that modularity is technically and financially the most
efficient way to build a vehicle — may not be unalterably opposed to modularity. As
suppliers continue to increase their level of final assembly of vehicles, they become a
new target for the UAW, and its position on modularity could change substantially if the
unionization picture at suppliers changes in its favor.
III. THE PRICE OF LAYOFFS.
The UAW’s job security strategy is simple: keep layoff costs high enough to keep its
people working. Therefore, it wants to reduce the number of allowable market-driven,
volume-related layoffs, and extend workplace closing moratoriums. It demands substantial
advance notification of plant closings, partial closings, transfers of operations,
spin-offs, phase downs, changes in products and anticipated layoffs of any size.
IV. OVERTIME MUST HAVE A STOP.
For the UAW, today’s major obstacle to job growth is overtime, which the union
characterizes as a “maldistribution of hours worked”. Overtime seems to have
been built into VMs’ planning: long-term and continuous overtime allows the automakers the
ability to keep plants producing at high volumes without the costs associated with hiring
new employees.
In the current light vehicle market, North
American plants are logging record overtime. According to the UAW, if U.S. assembly plants
had worked 40-hour shifts in the last three years, the VMs would have hired another 86,000
people. During the current sales boom, auto industry overtime has risen to a post-war
high, and now averages over seven hours a week. The union position is that its members
like the overtime paychecks — but they “don’t want to meet themselves coming
home.” The union wants to cut the overtime and improve wages so that its members
don’t need the extra paycheck, thereby increasing the number of union workers hired.
PLANNING IMPLICATIONS.
Once upon a time, Big Three-UAW agreements defined the industry, set its tone and
determined its future. That period in auto history may have passed completely, as the
industry has undergone fundamental changes.
With VM consolidation, supplier
consolidation and the rapid globalization of the industry, the UAW sometimes seems to be
fighting a rearguard action. The union realizes that it must still find a way to grow
membership, in order to regain its financial and political strength. Getting the three
majors to hire more assembly workers seems unrealistic, as does unionizing the transplants
— especially in the South. Therefore, as outsourcing continues, the union has already
begun eyeing the suppliers as their next target for unionization.
Some experts have even suggested that in
its present relatively weak bargaining position, the UAW should consider aligning with
another union or unions to bring membership up to a more respectable level or, failing
that, to mimic the VMs and globalize, creating an international auto workers union which
crosses continental boundaries and bargains for contracts with the leverage of a million
workers.
For supplier companies, with added
responsibility comes additional pressure. As outsourcing widens, they can now expect
heightened labor pressures to go along with the pressure from the VMs to cut costs.
Vehicle manufacturers, competing with foreign and transplant manufacturers with more
flexible labor situations, are faced with balancing labor relations against competitive
imperatives. They will need all the labor peace they can bargain for if they are to gain
the efficiency needed to continue to compete.
But whatever comes out of the present
negotiations, the real test of how they succeed or fail in establishing peace and
productivity for corporation and union alike will come with the next serious slump in auto
sales, or the next economic downturn.
Sam Fiorani, PricewaterhouseCoopers