Some companies have already reached the
limits of the traditional manufacturing model, in other words the Manufacturing Resource
Planning (MRP II) model. This means that, if a company and its competitors have achieved
the same goals – in terms of customer service level or on-time deliveries – the company
needs to find other methods of improvement in order to be more competitive from a
manufacturing point of view. Also, because the continuous improvement philosophy is now a
common rule in the manufacturing environment, when a company has reached a limit it needs
to find a solution to progress further.
From a manufacturing point of view,
Continuous Flow Manufacturing (CFM) seems to be a good alternative to the MRP II model.
Testament to this are the results of a CFM implementation which have been both significant
and impressive. CFM gives you a real manufacturing competitive advantage.
This article introduces the concepts of
flow manufacturing and it explains why flow methods may become the ultimate means for
improving production and Supply Chain performance. This article is a summary of a white
paper – Flow manufacturing: a breakthrough business strategy – written by Industry
Directions in collaboration with American Software.
Introduction
During the past decade, companies have
spent billions on new systems, equipment and information technologies. However,
manufacturers have yet to gain the breakthroughs in market responsiveness, operating
efficiencies or greater profitability they have sought to achieve. For many companies,
on-time deliveries are still at 95 percent, production costs haven’t improved,
productivity hasn’t gone up and annual inventory turns are still below ten. What is
the solution? Some now think they have found the answer in CFM principles.
Flow manufacturing is a pull-driven
strategy. At its core is the principle that demand can be synchronized with a daily
production rate by properly sequencing items on a flow line that is replenished frequently
by suppliers. In this way, inventory is kept to a minimum, goods are made to demand, cycle
times fall within the required order-to-deliver response times and constraints are
minimized.
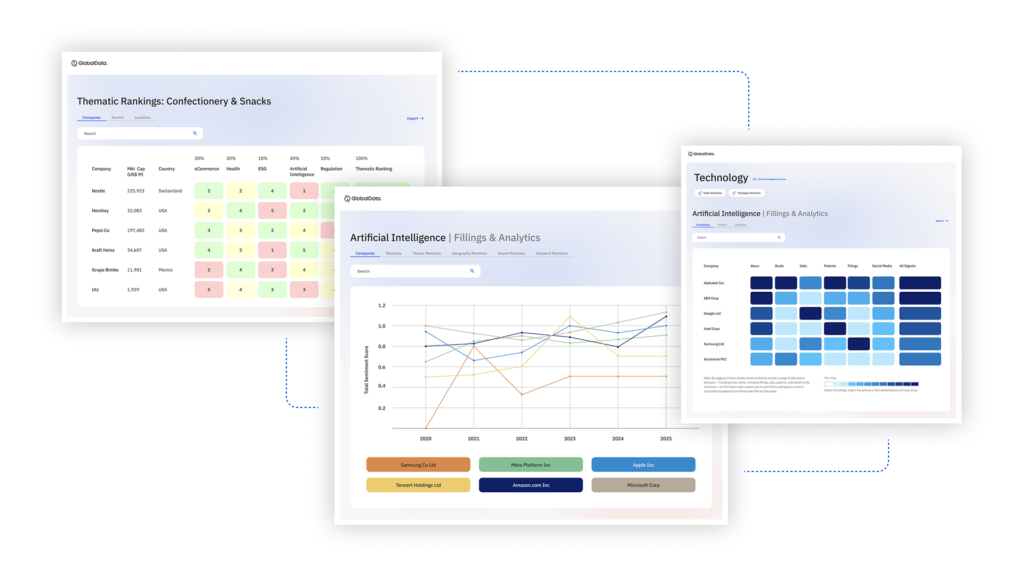
US Tariffs are shifting - will you react or anticipate?
Don’t let policy changes catch you off guard. Stay proactive with real-time data and expert analysis.
By GlobalDataIn the next few years, what has been a
quietly growing trend will emerge as a mainstream approach. For those companies that seek
a competitive advantage, the time to apply flow manufacturing techniques is now. Today,
nearly 50 percent of the Fortune 500 companies are learning about and testing these
principles in their own plants. The automotive, aerospace and electronics industries are
also in the process of educating their suppliers. We believe that the concepts of
continuous flow will change how manufacturing is done across all industries.
Manufacturing improvements
The three critical success factors for
manufacturers moving into the millennium, as observed by Industry Directions, are customer
responsiveness, greater efficiencies and retained profitability. Responsiveness has moved
up in importance as the competitive playing field has squeezed companies to out perform
their rivals in speed, flexibility and reliability or lose their standing. Most
manufacturers, however, have yet to achieve the reductions in cycle time, inventory and
costs, or gain the productivity improvements and quality performance that they hoped to
reach.
Major shift under way in industry
Call it flow, lean, agile or CFM, it has
been the hidden secret of a great many manufacturing companies considered leaders in their
industry. Industry Directions estimate that nearly half of the industrial Fortune 500 and
many other leading companies are now deploying continuous flow production strategies in
one form or another. Most notable are OEM companies in the electronics, aerospace and
automotive industries that have pushed their Supply Chains to adopt Just-In-Time (JIT) and
lean manufacturing practices for the last decade. However, there is evidence that
regardless of industry or production style, manufacturers across the board are trying flow
manufacturing. In most cases, the results are immediate, measurable and significant.
Companies report doubling capacity in less space; on-time deliveries in excess of 98
percent; cycle time reductions from weeks to days or days to hours; decreased
work-in-progress and finished goods inventory worth millions of dollars; decreased cost of
quality and increased productivity. Those that have achieved these kinds of results are
quick to admit they have a long way to go to fully adopt the continuous flow principles
and meet their ultimate goals.
CFM – basis of competitive
strategies
Regardless of industry, type of
manufacturing environment or product volumes, continuous flow principles can be
implemented quite successfully. Most challenging is deploying them in a shop that does
highly configured or engineered-to-order products, yet it is being done with almost as
much success as found in high volume, more repetitive make-to-demand operations.
The principles of flow manufacturing are
based on eliminating waste, streamlining processes, building to demand and implementing
continuous improvement – concepts learned from Japanese best known methods and exhibited
in the Toyota Production System.
The underlying concept is based on the
theory that by properly designing production lines and balancing the mix of products to a
daily demand rate, quality goods can be produced as ordered – and at a rate that falls
within the required order-to- deliver response cycle time. As a result, the entire supply
process is pulled (and sequenced) from actual demand; it is not pushed (or rescheduled) to
meet scheduled due dates. It takes more than moving equipment around to support product
family production lines, creating flexible workstation teams, establishing quick
changeovers and introducing Kanban signals – steps often taken to set up cells or JIT
processes. It requires:
- specific flow training and continually
maintained disciplines - a mechanism for defining and refining
optimal line design - Kanbans and mixed model production sequence
- a mathematical model for synchronizing the
daily production rate to actual demand - agreements and signals with suppliers, and
the ability to quickly reflect product engineering changes in the line design - Kanban calculations, operator instructions
and production reporting
All companies face three challenges in
adopting flow practices:
- untrained people who resist change
- inconsistent discipline
- a lack of integrated systems and the tools
needed to support the new business strategy
Fig.1 Flow line design and balance
Fundamentals of flow
techniques/flow-driven line design and synchronization
The most critical element of CFM is
establishing the correct design of each flow line. The first step is to identify your
manufacturing processes and determine process commonalities as a basis for product
families that will be built together on a given line. Based on demand patterns, and what
is known about future growth expectations, a line is designed so that processes and
materials flow at a consistent rate to meet the daily demand objective.
Make-to-demand line smoothing
Demand smoothing across lines is a
procedure used to calculate the daily production rates for every product on flow lines,
based on a given day’s demand, not on a fixed daily production rate. Using the new
rates for that day, the appropriate mix of products for each line is determined and
sequenced. The result is considerable flexibility on the line to match changing demand
characteristics in the marketplace.
As daily demand varies, the items produced
vary and the resources, such as operators, move around. For companies that produce high
volume, highly repetitive products, the demand smoothing process is fairly
straightforward. For those that produce configured and engineered items in lower volumes,
or items with more demand seasonality and volatility, the process requires additional
considerations.
Kanban management
Kanbans, by definition, are visual methods
for replenishing materials as they are consumed during the manufacturing process. Also, by
definition, they limit the amount of inventory kept in raw-in-process or on a line. There
are multiple types of material Kanbans, some of which have been mentioned earlier.
Replenishable Kanbans are replenished when
line stock is consumed by demand and a signal is given. Non-replenishable Kanbans are
replenished only when orders are booked, not when materials are consumed. In-process
Kanbans are added to a line to buffer operations (or ‘wet the line’) between
feeder and primary flow lines or to add capacity to a process as needed. It is quite
common to have inventory on the flow lines, and to have approximately a week’s worth
of work-in-process stock, which is maintained in a two-bin system. When one bin is empty,
the second is used while the first is replenished by suppliers – often directly to the
line. In that way, the line doesn’t run out of materials and a Kanban mechanism – an
empty bin – triggers the signal for replenishment.
Revision level control
Engineering change control is not new to
manufacturing systems, although it is different with flow environments. Instead of
associating the change directly with an end item, it is associated with processes involved
in producing the item. In other words, the engineering change is tied directly to a
process definition (sequence of events, associated resources and operational method
sheets). As a result, when the change goes into effect – say in material -just the
associated process is changed, and that information is rolled up into the end item for
production reporting.
Operational method sheets
Method sheets are essential for producing
high quality products. They are graphically produced work instructions for line operators.
Unlike traditional work papers created for a given work order, method sheets are created
for a specific process performed on the flow line. They are also designed to be more
visual than work papers, to provide more guidance and to direct proper quality control and
verification procedures for each process event. Method sheets are based on engineered
product specifications and drawings, and they must be updated when a process undergoes
engineering changes. Integrating the creation of method sheets with the Bill of Materials
(BOMs) and engineering change functions produces considerable time savings and quality
measure improvements.
Line Reporting
A continuous flow environment makes
production reporting fairly straightforward. When products move from the end of the line
as finished goods, they are reported as complete. All the materials consumed in producing
those finished products are automatically deducted from raw and in-process inventory
through backflushing techniques. Any exception issues are handled with a scrap code.
Backflushing techniques very often accommodate multiple product revision reporting,
regardless of when or where they occur, to address the engineering changes. Exception
reporting is always needed, whether it refers to products or process variances. Flow lines
are no different; they are just easier to monitor. Deviations from the daily rate are
reported as linearity (production variances), and line bottlenecks are reported as
production exceptions.
How can IT help you to implement
flow manufacturing techniques?
Flow manufacturing is based on various
techniques and tools in order to design a production environment able to provide a
consistent flow of products. Even if the principle is simple some of these techniques are
complex to implement. Therefore, it requires tools in order to facilitate the
implementation and the management. For example, the purpose of the demand line smoothing
technique is obvious. However if a company produces various items on the same line it
needs to determine the best sequencing pattern for an optimal throughput in order to meet
the demand. This calculation could be complex, especially if the company produce
configured or engineered items.
In addition, if you need to design a new
line – or balance a line – with a PC-based module, this can be easily completed with the
help of the Graphical User Interface (GUI). This allows you to underline the part of the
line – or the process – you need to improve in order to design a proper line.
Also, these tools allow you to support
Kanban management when required. They help you for size calculations, the quantity per
container and the number of containers. Some software also includes the workflow
capabilities to support the electronic Kanban management.
In summary
The use of flow manufacturing strategies is
no longer confined to a few innovative companies. In the last few years, a large number of
manufacturers – representing all the industrial sectors – have taken a serious interest in
demand-driven processes and flow manufacturing techniques. They see this approach as the
means to achieve significant gains in production throughput, order cycle times, product
quality, inventory reduction and customer responsiveness.
Copyright March 1998 by Industry
Directions, Inc. All rights reserved
Patrick Cunin is product marketing
manager for Manufacturing. His responsibilities include coordinating JBA’s
Manufacturing Sector Focus Team. The team defines the improvements of the manufacturing
product as well as the new functions required in order to address the market.