
The UK has a long history of innovation and invention. What it’s not been so adept at traditionally is commercialising its inventions. For example, the lithium ion battery was invented at Oxford University in 1980, but commercialised first in Japan. Similarly, the super material graphene was first isolated at Manchester University in 2003, but commercial application patents have been ‘stockpiled’ by Samsung of Korea.
The UK’s relative lack of success in commercialising technology has led to its R&D efforts being identified as being affected by the ‘valley of death’ – the situation where startups or new inventions struggle for mass adoption or commercialisation.
To continue to encourage and ‘derisk’ invention and innovation in the UK’s automotive industry the Advanced Propulsion Centre (APC) was established in 2013 as a result of intervention by the UK government and the industry (the UK’s Automotive Council). The APC has been funded with GBP1bn, with half of the fund stemming from the government and half from industry. Its brief is simple, but complex: support the UK industry’s move to low carbon solutions and create an ecosystem that supports R&D, thus ending the dreaded ‘valley of death’.
As part of this brief, the APC this week published The Roadmap Report: Towards 2040 a guide to automotive propulsion technologies. Among many reasons, the APC created the roadmaps to provide a common understanding of opportunities and threats and to promote investor confidence in the technologies they have invested in (and presumably to assist in future funding rounds).
Although conceived in the UK as a result of conversations with 139 entities across the automotive value chain, the roadmaps are global in outlook. In all, the report contains eight separate roadmaps, three in the vehicle sphere and five in technology. The roadmaps are:
- Passenger car
- Bus
- Commercial and off-highway
- Electrical energy storage
- Electric machines
- Power electronics
- Thermal propulsion systems (internal combustion engines by another name)
- Lightweight vehicle and powertrain structures
In processing the roadmaps six common drivers or megatrends were identified, with the usual suspects lining up as the major influencers: emissions legislation; localised regulation; wider energy system; connected and autonomous; MaaS and lifecycle regulation. Indeed, in respect of the latter, the APC already believes that well-to-wheel analysis, long-held to be the next staging post for emission regulation focus – after the current focus of regulation on wheel-to-wheel has passed – will be bypassed by a movement straight to the entire lifecycle analysis of emissions.
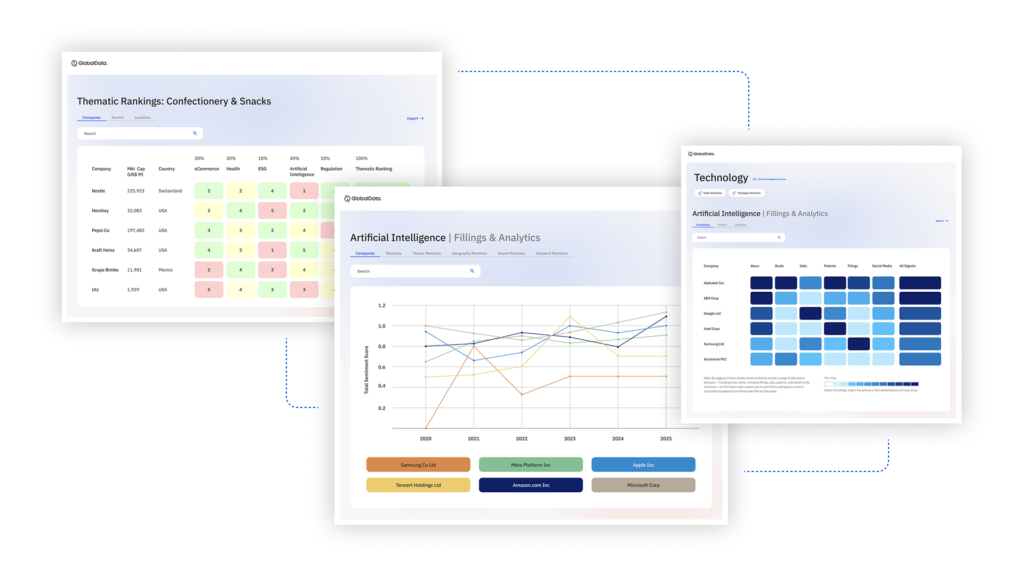
US Tariffs are shifting - will you react or anticipate?
Don’t let policy changes catch you off guard. Stay proactive with real-time data and expert analysis.
By GlobalDataIn a 130+ page report the APC has highlighted key findings in its eight roadmaps. For example:
- Batteries: in the field of batteries (electrical energy storage) it foresees power density in kW/kg quadrupling from the current baseline of 3kW/kg to 12kW/kg by 2025. Similarly, energy density will nearly quadruple from its current level of 280Wh/l to 1,000Wh/l by 2035. These performance improvements will be accompanied by a fall in price from US$280 kWH to US$100kWh by 2035. However, to deliver these targets battery chemistry will have to change with new anode (cited were transition metal oxides, metallic anodes and novel additives) and cathode technologies (sodium-ion, magnesium-ion and lithium-sulphur) being necessary
- Electric machines: costs are forecast to decline from US$10 per kW to US$4.5 per kW by 2035, while power density will quadruple from a current 7kW/l to 30kW/l by 2035. Key to this step change is seen to be the introduction of alternative winding materials, while there’s potential for additive manufacturing to remove the need for dedicated winding processes
- Internal combustion engines: brake thermal efficiency for light duty engines is seen as improving from a current best-in-class of 42% to 53% by 2035, with heavy duty engines improving from 47% to 60%. For the ICE, the key message from the APC is that it’s the system that counts, calibration tools that evaluate the entire system efficiency rather than individual strategies in isolation will be the way forward
Underpinning many of the roadmaps is the sizeable electrification opportunity for UK companies. The APC calculates that the market will be worth EUR30b by 2030 due to 90% of light vehicles requiring some form of electrification. However, the window of opportunity is small as in 2018 we’re just two full vehicle lifecycles away from this date.
Accompanying the launch were presentations from several companies that have benefited from collaborating with the APC in bringing projects to fruition and who have benefited from the roadmaps in identifying opportunities. Among them were JLR, Prodrive, GKN and the UK Battery Industrialisation Centre (UKBIC).
UKBIC is a plan to bring a 20,000 sqm facility battery prototyping plant into operation in the UK by 2020, with the aim of attracting to the UK a battery giga factory. UKBIC will be equipped to be able to manufacture all lithium-ion anode and cathode materials being manufactured today and will be future-proofed to be able to handle all the most promising chemistries of the future such as solid state, sodium iron and silicone-based electrodes. Flat out UK BIC will be able to manufacture up to 20,000 packs a year. In reality volume will not be at that level because it’ll be batch manufacturing many prototype products.
In the case of JLR, the APC provided match funding for its High Volume E-Machine Supply (HVEMS) project. HVEMS was a GBP11.1m project that ran from April 2015 to March 2018, with the aim of investigating what is required to manufacture electric machines in high volume in the UK or Make Like Production (MLP) in JLR’s terminology. As well as JLR there were a further eight consortium partners on board including SMEs like motordesign Ltd and Horizon Instruments, a tier one in the form of Tata Steel and academics at Warwick and Newcastle universities. The key benefit of the project was the upskilling of the consortium partners in understanding what it takes to manufacture e-machines in high volume, with a long-term aim of putting the learning into practice to establish JLR’s very own high-volume e-machine facility as the company increasingly electrifies its fleet.
With Prodrive, the APC provided funding of GBP4.7m for a project to convert a diesel-engined Ford Transit into a PHEV using Ford’s 1.0L Fox engine as the ICE. The PHEV’s CO2 output is rated at less than 50g per km, with a pure battery range of 50km on the NEDC and a total range of 500km. This vehicle is on trial in London presently and Ford has plans to put the PHEV into series production in 2019. While the economics of the PHEV (due to on-cost of battery and e-machine) may be hard to justify for fleet operators presently the movement against diesel use in cities and increased congestion charging are rapidly changing the business case for PHEVs light duty vans.
While the APC was originally conceived as a project with a 10 year shelf-life, discussions are already ongoing between government and industry to sustain the APC beyond 2023 because it’s demonstrated its benefits in ‘derisking’ innovation and helping the UK’s auto R&D from avoiding the dreaded ‘valley of death’.