Despite the smooth lines and simple appearance, the cockpit is one of the most complicated and tightly packaged assemblies in a vehicle. Matthew Beecham reports.
Fully-loaded
The cockpit may contain 50% of the total vehicle wiring system and most of the vehicle functions are controlled from this area. With several hundred individual components, it is also one of the most common sources of quality problems. The standard of design and manufacture is therefore critical.
The space occupied by the cockpit is restricted by the requirement to provide good visibility and leg room for front seat occupants and by the intrusion allowed into the engine bay. Within this restricted area an increasing array of systems must be accommodated. The problem is particularly acute in smaller cars where airbags, air conditioning and driver information systems are becoming increasingly common and complex. Even in larger vehicles, new multi-media technologies are jostling for position, adding to the number of systems requiring mounting space and wiring routes. In a novel attempt to free-up more space in the cockpit area, Delphi developed a unique underfloor climate control system for the new Renault Espace MPV, offering greater levels of air circulation within the cabin and increased storage area. The climate control module has been designed to fit below the front passenger seat, liberating 50-litres of space normally taken up in the instrument panel. This location also makes servicing easier as the dashboard does not need to be removed for access.
Cockpit competitors
The main co-developers and assemblers of cockpits include Calsonic Kansei, Collins & Aikman, Delphi, Denso, Faurecia, Johnson Controls, Lear, Intier, Siemens VDO and Visteon
CalsonicKansei assembles cockpits, instrument panels and clusters at plants dotted across the US, UK, Mexico, Taiwan, Indonesia and Japan. Nissan is still the company’s main customer.
Collins & Aikman is another major producer of cockpits and instrument panels. The US supplier recently launched cockpit and instrument panel programmes for DaimlerChrysler, GM and Ford in deals worth $1 billion
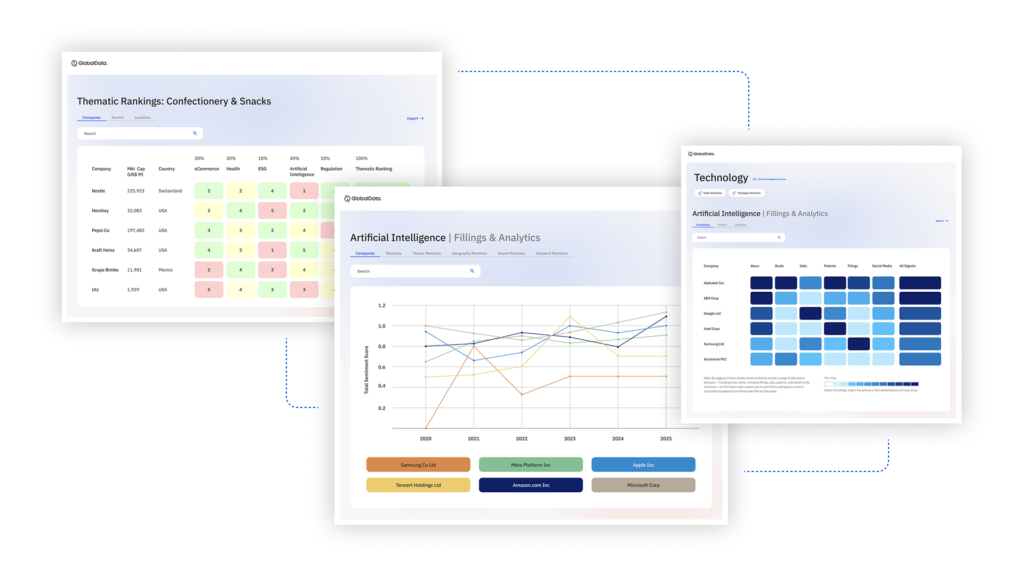
US Tariffs are shifting - will you react or anticipate?
Don’t let policy changes catch you off guard. Stay proactive with real-time data and expert analysis.
By GlobalDataDelphi has an 18% share of the North American instrument panel market. The company manufactures instrument panels and cockpits at its plants in the US, Mexico and Spain plus a joint venture in China. Delphi supplies ‘fully-loaded’ cockpits for a variety of vehicles, including the Mercedes-Benz M Class and GM’s Malibu and Grand Am.
Japan’s Denso is a major supplier of instrument clusters, claiming a 15% share of the global market, 39% share of the Japanese market and 12% share of the North American market. Denso produces instrument clusters in Japan, the US, Mexico, South Korea, Australia and the Philippines.
The French group Faurecia claims to lead the European outsourced assembled cockpit market, through its joint venture with Siemens VDO. Faurecia also co-develops complete cockpit architectures with carmakers. The company recently opened a new R&D centre in Germany, home to 550 engineers developing instruments and cockpits. Last year, Faurecia won a contract from the Chrysler Group to supply complete seats, standard seat frames, instrument panels, centre consoles, door panels and exhaust systems for various models. The contract will boost Faurecia’s North American business to around $1.8 billion a year by 2006, and is a clear warning to rival US suppliers Lear and Johnson Controls that they cannot rest on their laurels. Chrysler is said to have been disappointed with some of its traditional US suppliers, while Faurecia has been actively courting the DaimlerChrysler subsidiary. Although Faurecia’s share of the North American vehicle cockpit business is currently less than 1%, the French group expects to gain a bigger slice of the market by 2007. “We are moving very fast in North America,” said Olivier Fidry, Faurecia’s sales and marketing vice president for interior systems. “We have won a lot of business in Mexico with Volkswagen, GM and Chrysler. In addition, we now have two or three development programmes underway for Chrysler in the US. The US market is evolving as the customer is thinking more features.
Johnson Controls supplies cockpits to a number of North American and European carmakers. With a 5% share of the global cockpits market, Johnson Controls is developing a systems engineering approach to modules, with the aims of reducing development time, cost, mass and yet improve performance. “On the one hand, we are developing our capabilities on the instrument panel side of the business whereas on the other we are strengthening our electronics know how,” said Dr Dirk Blomeyer, Johnson Controls’ product business manager for cockpits and floor consoles. “If you then combine those two competences, you can deliver up to 50% of the value of the cockpit. As a global supplier capable of independently managing half the value content of a very complex system that puts us in an excellent position to co-engineer cockpits with the OEMs.”
Lear is the world’s largest automotive interior systems supplier, operating 289 facilities located in 34 countries. Its products span five auto interior segments: seats, flooring and acoustic systems, door panels, instrument panels and cockpit systems, and overhead systems. Since 1994, Lear has steadily increased its automotive interior capabilities to the point where it can now offer total automotive interior capability. The company has transformed itself from a seat maker to an integrator of complete automotive interiors. Ken Rudnick, Lear Corp’s vice president of intertronics, believes that Lear is uniquely positioned as the global cockpit market evolves. He said: “As more cockpits become outsourced, we can really add value to the customer because of our integration capabilities. As the cockpit displays more things and becomes more complex, we can integrate more modules in order to provide that much more value to the OEM.”
Magna’s Intier produces a range of components for the cockpit, including instrument panels, consoles and glove boxes. Intier has a strong presence in the European automotive instrument panel market. The company is also present in the North American instrument panel market.
Siemens VDO’s Interior & Infotainment product portfolio ranges from components and modules to complete cockpits and includes the commercial vehicle sector. The company supplies cockpits and instrument panels for Audi, BMW, DaimlerChrysler, MCC Smart, Ford, Opel, MG Rover, PSA Peugeot Citroen, Seat, Skoda and Volkswagen. The German supplier recently expanded its 50:50 joint venture with Faurecia, SAS Autosystemtechnik Verwaltungs GmbH to focus its activities on just-in-time assembly of cockpit modules.
Visteon’s product range includes cockpits, instrument panels and clusters. The company recently won cockpit and instrument panel and instrumentation business from Blue Diamond Trucks, DaimlerChrysler, Fiat, Ford, Nissan and Renault. It was also recently honoured by the Society of Automotive Engineers for its fully recyclable olefinic instrument panel. Jim Fleming, senior manager for Visteon’s interiors product marketing, has a clear idea of what carmakers look for in a cockpit supplier. He said: “OEMs are looking for an understanding of how all the four elements of integration, engineering, design and assembly interact. They are looking for expertise in all cockpit-related technologies ranging from plastic structures to electronics. They also want to see the end product as seamless rather than merely a collection of different technologies. It must be homogeneous and integrated.”
Keep it simple
For some time, cockpit designers have been working on ways in which to display more information yet make the dash appear less complex. The general approach is to ensure that only the most essential information is displayed while remaining features are available in the background or brought up at will. But the increasing fitment of sophisticated mobile multimedia systems, as well as safety and security items suggest that this part of the interior is still in its infancy in terms of development. The challenge is to find more space in the instrument panel to fit yet more features. “It is certainly true that this whole area is still youthful,” said Pearce Keane, senior product manager for Visteon’s electronics development. “We’re learning from other industries, such as military aircraft. We are already seeing a proliferation of electronic displays inside cars. The next step is more centralisation of those displays. The next step will focus on how to prioritise that information and deliver it to the driver. We are probably at that threshold now. But the next step is a little unclear as to which way the industry will go. We may see more use of head-up displays to highlight priority messages to the driver. But I think we will continue for the foreseeable future to see large centralised displays with potentially more use of audio warning and text to speech.”
The desire for a spacious interior, something always equated with luxury, is prompting interior designers to use new combinations and package of electronics and mechanical functions to modify or move pre-existing systems like air distribution, glove box, heating/cooling and audio facilities. In terms of controls, touch-screens offer space-saving possibilities, but designers are faced with the problem of distracting the driver’s attention too much. Some designers are looking to voice recognition devices to enable them to eliminate many controls that have traditionally been manually operated. “People are certainly open to the idea of using voice recognition in their cars,” said Philippe Aumont, Faurecia’s product planning vice president. “Their readiness, however, may have more to do with the fact that they have never actually experienced it. However, we think that voice recognition is a must for the long term. In the meantime, we focus on perceived quality, occupant feature integration and system integration, and we expect to see more touch screens or touch surfaces on the seat and door arm rest.”
Although voice recognition systems continue to develop, they are proving more complex than originally thought, due to the complex ambient sound environment of the car. A major problem facing developers is in getting a clean audio signal for the driver’s voice and not from a passenger. More complex solutions require more powerful processing capability are still under development.
Material matters
The majority of designers have accepted plastic in its own right and now design to bring out its unique attributes rather than trying to make it appear like something else. Ken Shaner, Lear Corp’s vice president of cockpits integration, said: “The leather-look dash is becoming less popular these days. The trend is moving back towards making plastic look like plastic. And some of the latest designs with new grains actually look very appealing.”
The general appearance of fascias is a complete series of curves to continue the design shape from the cockpit through to the doors and also to flow into the centre console. “There are a lot of themes such as continuous flow from the cockpit to the doors,” added Shaner. “We’re seeing a lot of that on next generation models to make it appear as if you are sitting in one continuous flow of harmony, grain, colour and trim lines.”
Vinyl (polyvinyl chloride or PVC) has been used to make automotive instrument panel skins since the 1960s. It is versatile, cheap and available in a wide variety of forms. Apart from the fact that it can cause fogging under high UV light loading, the main problem of using PVC is that it is environmentally unfriendly, posing major problems when it comes to disposal. Consequently, alternative materials have been used, such as polyurethane (PU) and thermoplastic polyolefins (TPO).
By 2010, however, some manufacturers believe that vinyl will no longer be used for covering instrument and interior door panels in the new vehicle programmes in North America. PVC will be replaced by TPO as the skin for instrument panels and door panels, because a growing number of proponents consider TPO better than PVC except for price. TPO maintains its colour and softness longer than PVC, is up to 15% lighter and far more recyclable. That is important in Asia and Europe where carmakers have been phasing out vinyl and shifting to TPO or other plastics because of pressure from environmentalists. As American manufacturers become more global, they are standardizing processes with their Asian and European units and affiliates. GM is thought to be leading the TPO push in North America.
Instrumentation trends
The number of instruments has increased over the years as vehicles have become more complex and the instruments themselves have become cheaper. Few cars in the 1960s had a tachometer but it is now almost a universal fitting. Similarly, legislation has now made the use of tachographs obligatory in trucks. The big increase, however, has been in event-controlled indications, such as lights which actuate to show warnings for indicators, low oil pressure and high lighting beam. A typical car now would have two large instruments showing speed and engine revolutions plus two smaller instruments showing engine temperature and fuel gauge. All other instruments are either incorporated in the larger instruments (odometer and trip meter) or separated from the main cluster and displayed as event warnings.
While conventional displays and gauges incorporate back-lit panels with incandescent lamps as light sources, and pointers that have been treated with phosphorescent additives to glow in the dark, there is a major shift toward the greater use of LEDs as light sources. The major benefits of LED lighting include longer life expectancy, which is generally the life of the vehicle, the flexibility and availability of different colours, and the fact that the illumination does not change with voltage variation such as dimming the headlights.
Another trend is the increasing use of self-illuminating displays based on organic and inorganic materials which eliminate the need for separate back-lighting. There is also a move toward positioning the instruments at the centre of the dashboard, partly for stylistic reasons and partly for safety reasons. The trend started in Europe with the new Mini and BMW Z8 and spread to the Toyota Yaris and Smart and is now appearing in the US.
According to Denso, one of the major changes in recent years is that instrument clusters have been increasingly connected to vehicle local area networks (LAN) to share information with other electronic control units, which enhance electronic control of the instrument clusters. Denso points out that another design change is that stepper motors have become de facto standard for movements that convert the data into a readable form on the dashboard, improving performance of the instrument clusters.
In terms of volume growth of reconfigurable displays, manufacturers report a surge in demand in the US, following Europe. Although reconfigurable displays are still a feature of some upmarket cars and light trucks — featured in less than 1 million US new-build vehicles — fitment rates are expected to accelerate through this decade.
For some time, Denso has been developing reconfigurable instrument displays. A spokeswoman for the company told us: “Reconfigurable displays have been adapted to provide a larger amount of information. For instrument clusters, Denso launched the world’s first electroluminescent (EL) display in 1998 and the world’s first transparent EL display in 1999. [Our] 5 – 6-inch TFT liquid crystal display is used for luxury car’s reconfigurable displays. We expect that these technologies combined with analogue displays will be more popular in the next 5 – 10 years because they can show a larger amount of information.”
Delphi has also developed a line of reconfigurable displays. In fact, the world’s largest auto parts supplier will soon supply the auto industry’s first OE colour-configurable instrument cluster. Available on the 2005 model year Ford Mustang, the feature allows the driver to modify the instrument cluster to provide a personalized colour combination using three LEDs. The driver can mix and blend the intensity of five levels of red, green and blue to create 125 different custom-coloured backgrounds.
While superficially instruments may appear much the same today as they did 30 years ago, they have changed extensively in that time and they are likely to change even more through this decade.
![]() |
Expert Analysis
|
![]() |
![]() This added-value intelligence set contains our instrumentation and cockpits report (2nd edition), plus 9 expanded supplier profiles of Collins & Aikman, Delphi, Denso, Faurecia, Johnson Controls, Lear, Magna, Siemens VDO & Visteon. To find out more about this report and to order your copy, please follow this link. |
![]() |
![]() |