Along with the engine and transmission, a vehicle’s chassis system is the determining factor when it comes to handling characteristics. The chassis construction influences vehicle driving dynamics, comfort, safety, and road holding ability. This feature, extracted from just-auto’s third edition survey of chassis engineering and systems, considers chassis systems definitions and current developments in the field.
Chassis systems definitions
In the early days of vehicle design and manufacture, the chassis was the frame above which the body was mounted, and below which the axles were mounted by means of their springs, together with any associated steering and braking systems.
During the 1920s, pioneers including Budd in the US and Lancia in Europe began to study the implications of eliminating the chassis frame, attaching the wheels – whether mounted on axles or independently – directly to the body. It quickly emerged that to achieve similar orders of stiffness in bending and (especially) in torsion, a load carrying body could be made lighter and more compact than an unstressed body mounted on a chassis frame. By the 1950s the stress-carrying “unitary” body had become the industry standard. The term “chassis” had not disappeared, but had rather been transferred to those systems between the body and the road surface – the suspension linkages, springs and dampers, and the wheels themselves – together with the closely associated steering and braking systems essential for control of the vehicle.
Some observers regard chassis systems and suspension systems as synonymous, but this disregards the interdependence of suspension, steering and braking systems and the fact that they are integrated to an increasing degree, especially at the electronic level. It may also be argued that even in the early days of motoring when complete chassis were delivered to coachbuilders for body installation, the steering and the brakes (such as they were) were already installed.
Current scope
In present-day terms, therefore, the terms “chassis engineering” or “chassis systems” embrace a hierarchy of technologies and features that may be outlined as follows:
- Suspension: embracing the choice of basic geometry for optimum wheel location, the mounting of suspension members to the body (including the use of sub-frames), the springing medium and the provision of damping of vertical wheel movement.
- Steering: the optimisation of front suspension geometry for steering, the choice of steering system, the provision of power assistance, the satisfaction of safety requirements, and the provision of “augmented stability” through interaction with the braking system.
- Braking: the choice of friction system, the design of the operating linkage, the provision of servo assistance, the satisfaction of safety requirements, the provision of anti-lock braking and other enhancements such as emergency brake assist.
- Wheels and tyres: choice of wheel and tyre size, choice of wheel material and tyre configuration, choice of spare wheel configuration or “run flat” technology.
New materials
From a materials point of view, steel conglomerate Corus has unveiled a novel design for a supermini which cuts body weight by 20%, halves the number of body components and yet offers class-competitive crash and rigidity ratings. Dubbed the ISC (Innovative Small Car), the design demonstrates to vehicle manufacturers seeking vehicle weight savings that steel is capable of structural lightness, making the move to expensive lightweight materials such as aluminium unnecessary.
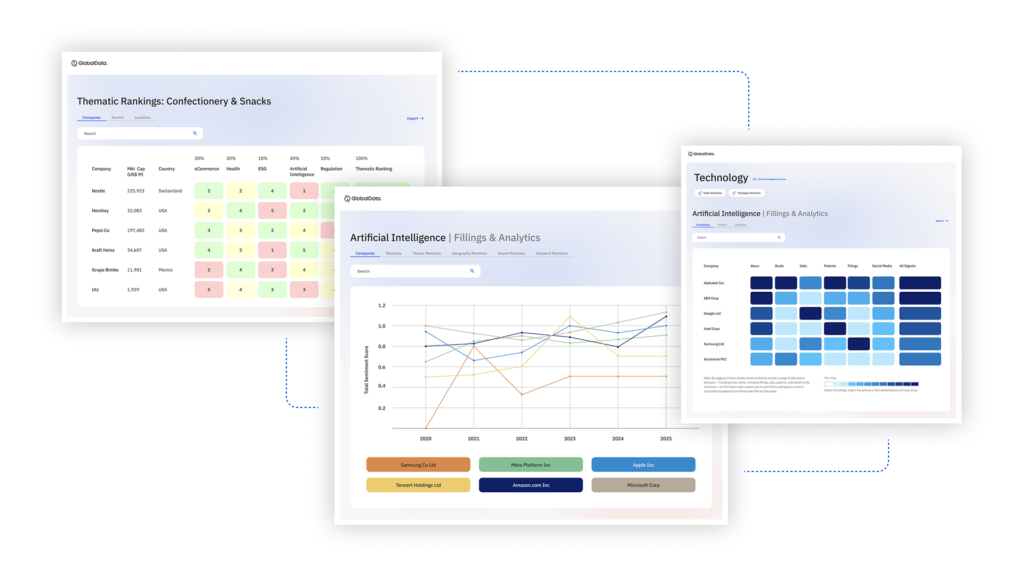
US Tariffs are shifting - will you react or anticipate?
Don’t let policy changes catch you off guard. Stay proactive with real-time data and expert analysis.
By GlobalDataDesigned by a small team at Corus’ International Automotive Research Centre in Warwick in the UK, the ISC introduces a revolutionary kind of chassis construction called the Structural Ring Concept in which the body-in-white assembly is based around two structural rings with major centre sub-assemblies (roof and centre sections) welded in place between them. The structure simplifies chassis construction, reduces the number of components, and improves safety.
European steel giants ThyssenKrupp Stahl and Arcelor are jointly developing new steel alloys to offer greater strength and light weight to assist OEMs.
The partners are developing a new high-manganese content flat carbon steel product that will have high strength but will be easy to stamp, allowing OEMs to use thinner and lighter panels in structural parts. The new steel will help reduce a car’s overall weight by as much as 20%. Arcelor and ThyssenKrupp Stahl will market their own versions of the steel separately and say the first supplies will begin in 2006, with quantities sufficient for full-scale production available a year later.
Basic suspension system requirements
The most basic objective of the suspension system is to allow each wheel to move vertically, for the sake of ride comfort, while constraining its movement in other senses so as to maintain stability and control. Vertical wheel movement from the datum position compresses a spring, which in most cases keeps wheel movement within limits, although bump and rebound stops are provided should the limit – normally set by the space constraints of body design – be reached. A damper ensures that the subsequent spring movement (an oscillation) is quickly reduced to zero.
Generally speaking, the most important secondary aim of suspension design is to keep all four wheels as nearly upright as possible at all times, not only when travelling across uneven surfaces but also when the body rolls during cornering. A conventional car tyre delivers optimum grip for cornering, braking and accelerating when it is upright. In practice it is impossible to achieve this ideal constraint without resorting to extremely costly and space-consuming measures, and current suspension systems are in most cases concerned to approach it as nearly as possible.
In some cases, as with the use of trailing arms at the rear of front-driven cars, the inevitable camber change and reduced grip during cornering is exploited as a means of reducing understeer – but overall cornering grip is also sacrificed as a result.
A further and still important requirement is that the weight of the wheel, tyre, hub and suspension assembly at the “road” end of the spring should be as low as possible. The lower the weight is relative to the weight of the body (the lower the ratio of unsprung to sprung mass), the less the body will react to any wheel movement, and the better the tyre will be maintained in contact with the road surface, to the benefit of both ride comfort and road holding.
Recent notable technical advances in this area include one from Bose. The German company, famous throughout the world for its acoustic systems, has produced a radical electromagnetic suspension system that smoothes out the bumpiest roads and minimises roll and pitch during cornering and braking. The system is the result of more than two decades of research to combine the ride and handling qualities of luxury sedans and sports cars.
Several other companies, including ZF, Delphi Automotive, Bosch and TRW, have also developed similar suspension packages.
Meanwhile, ThyssenKrupp Automotive has revealed a novel design for an independent front suspension system for heavy trucks. Independent front suspension is not currently used on trucks, but could have major handling and safety advantages over existing systems. ThyssenKrupp’s design features an integral subframe on which the axle, suspension and steering gear are pre-assembled, and over 80% of the componentry is manufactured by ThyssenKrupp subsidiaries.
Suspension linkages
The basic principles of suspension engineering are eternal. The task of the suspension linkage which attaches each wheel to the vehicle body is to keep the wheel as nearly upright as possible in all circumstances (zero camber angle) and pointing in the desired direction (nominally parallel to the vehicle centre line, except when the front wheels are being steered), regardless of the unevenness of the road surface which causes the wheels to move vertically, and of the attitude of the vehicle body which may move in pitch, roll, and heave (pure vertical movement) according to the forces acting at its centre of gravity.
The importance of keeping the wheels as nearly vertical as possible is that this gives the tyres the best chance to operate efficiently, with minimum rolling resistance. Many competition cars deliberately run positive (top-inwards) camber to achieve maximum cornering grip but the rate of tyre wear and the additional rolling resistance when running in a straight line are unacceptable in most road-going cars.
The ideal can never be achieved in practice but modern technology allows it to be more closely approached. In addition, chassis engineers now deliberately exploit the small remaining changes that occur when the car rolls and/or the wheels are subjected to a sideways load, to improve grip, stability and handling.
While smaller high-volume cars have continued to use simple solutions (front MacPherson strut or double wishbone, rear torsion beam) refined in detail, more expensive models, both front and rear-driven, increasingly use multi-link suspensions in which each link performs a specific role within the overall task of maintaining the wheel precisely in alignment. The design of such linkages has only become practicable with the use of CAD.
While the mechanical linkage remains the principal means of controlling wheel movement and alignment, the behaviour of the flexible suspension arm mounting bushes is also now recognised as important, and is now more or less completely understood. In a rather parallel fashion, subtle changes to the geometry of suspension mounting points are now exploited. It used to be accepted for example that the hinge-points of a suspension wishbone (in a double wishbone arrangement or at the bottom end of a MacPherson strut) should lie on a line parallel to the car’s centre-line.
Today, that line is rarely parallel, as chassis engineers create anti-dive and anti-squat effects to minimise body pitching during braking and acceleration.
Examples of multi-link rear suspension can be found in recent models from BMW, Jaguar, Lexus, Mercedes-Benz, Nissan, and Renault. Renault provides a good illustration of the “crossover” point, since its D-segment Laguna retains a sophisticated torsion beam rear suspension but the E-segment Vel Satis uses Renault’s multi-link “Trigon” system (and this despite the fact that both models are built on the same basic platform).
In one sense, therefore, suspension design is becoming standardised, with one solution for smaller, essentially front-driven cars up to the C/D segments, and another for the luxury car market. Technical interest therefore lies in:
- The exceptions to this general rule, and the vehicle manufacturer’s stated reason for the choice;
- The refinements to, and adaptations of, the standard layouts to achieve particular stated purposes. An example is the trend, begun by Honda in the late 1980s, of using double-wishbone front suspension in which a long upward extension of the wheel hub enables the upper wishbone to be installed above the wheel itself, bringing a number of geometric advantages in exchange for a small increase in unsprung weight.
|