The combination of extrusions, castings, and technologies like roll bonding and friction stir welding are central to the light weight and high strength of Ford’s GT chassis.
By Christopher A. Sawyer, Executive Editor, Automotive Design & Production.
There was never any question that the chassis of the 2005 Ford GT would not resemble that of the 1960s-era original. A stamped-and-welded steel monocoque may have been well ahead of the welded tube racing car spaceframes of the day, but it’s nothing special today. Nor would carbon composites, with their hand-labor and exotic curing regimen, be used because the build process is too slow and expensive. There was only one realistic choice: aluminum extrusions, a proven technology made popular by the Lotus Elise. Only the six-person chassis team–lead by Huibert Mees of Ford’s Special Vehicle Team–went a few steps farther by including large aluminum castings, roll-bonded sheets, and an exotic joining technology.
According to Mees, “The more we thought about it, the more we realized that it made sense to combine the extrusions with a casting at each corner in order to make the attachment locations for the suspension extremely stiff and accurate.” (There is a fifth casting at the end of the passenger compartment tunnel on the rear bulkhead. It ties this structure to the rear of the vehicle.) Mees says the suspension attachment points are within +/- 0.75 mm, while the tub is within +/- 1.0 mm diagonally. Not only does this enhance the car’s on-track performance, it also helps control road noise and impact harshness, since–unlike the original Ford GT–this version will spend most of its time posing on Rodeo Drive than in pitched battle on the Mulsanne Straight at Le Mans.
![]() |
It may look like the original, but it certainly isn’t built like it. Aluminum is the material of choice for the 2005 Ford GT, in the form of castings, extrusions, and sheet. But it’s how the materials are utilized that sets this car apart. Despite a tight timeframe, the chassis makes use of adhesives, friction stir welding and roll bonding without adding excess weight, sacrificing rigidity, or impairing repairability. |
The castings are sourced from Ramsden Industries, Ltd. (London, Ontario) and Citation Corp. (Birmingham, Ala.), while Hydro Aluminum North America (Baltimore, MD) provides the extrusions. “The castings are A356 heat treated to T6, and the extrusions are a combination of 6061 and 6063, also heat treated to T6,” says Mees. Where weight is more important than strength, the 6063 is used. In those areas that first must be bent–like the roof and rear “sport bar” (“roll hoop” to non-lawyers)–the material is delivered in T4 form, then heat treated to T6 level after forming. “The nice thing about extrusions,” says Mees, “is that every wall can have a different thickness.” And in many cases–the rocker panels are but one example–they do. “Three millimeters is about the limit if you want repeatable, effective welds with no material burn-back,” says Mees, “while 8 mm is the thickest section we use.” Side crash forces are fed through the rocker panels into the main structure, with support from the extruded aluminum door beam that ties into the main structure through the hinge and lock plates.
How well do you really know your competitors?
Access the most comprehensive Company Profiles on the market, powered by GlobalData. Save hours of research. Gain competitive edge.
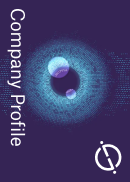
Thank you!
Your download email will arrive shortly
Not ready to buy yet? Download a free sample
We are confident about the unique quality of our Company Profiles. However, we want you to make the most beneficial decision for your business, so we offer a free sample that you can download by submitting the below form
By GlobalDataMilford Fabricating builds the chassis up in modules for Ford. The first station assembles the front from the dash panel forward. The next handles everything from the rear bulkhead to the rear bumper. Then these sections are joined together along with the greenhouse, rocker boxes and some minor elements. Finally, there is an off-line assembly station where the crossmember for the steering rack, bumper assemblies, etc. are welded into place. “The extrusions are robotically cut to length, mounting holes are drilled, and these pieces are clamped into fixtures before being robotically welded,” says Mees. Seams that are inaccessible to the robots are then welded by hand. “Each welding station is designed for a cycle time of one hour,” says Mees, and the overall cycle time is tied to a production rate of 1,500 GTs per year.
The floor section is made up of two 0.7-mm roll-bonded aluminum sheets. A thin graphite pattern in laid on one sheet before they are pressed together between high-pressure rollers. “The effect is similar to hammer welding,” says Mees, “because the two pieces are metallurgically bonded together in those areas where there is no graphite.” The graphite line includes an area at the edge of the panel through which air is injected at high pressure. This inflates the graphite-covered pockets to create voids. As a result, the weight of the panel is equivalent to that of two 0.7-mm aluminum sheets, but its strength is much greater. “Tower Automotive provides this technology, and they are able to inflate those panels up to 5.0-mm apart. And by getting creative with the graphite layer,” he continues, “they also were able to emboss the letters ‘GT’ in the floor.” The floor panels are then glued in place, and riveted to prevent peeling under high loads.
Another Tower Automotive technology is used to bond the center tunnel to the extrusions running down the center of the car. The U-shaped aluminum sheet that forms the tunnel top and sides is placed atop the extrusions, then friction stir-welded. A small mandrel–about an inch in diameter and sporting a nub no larger than ½-in. on its lower face–is spun to 10,000 rpm, then plunged through the clamped sheet and extrusion. The heat generated by the mandrel causes the two materials to briefly reach their melting temperature and combine. This introduces heat in a confined area and creates a homogenous sealed seam. “We considered gluing the pieces together,” says Mees, “but felt this was a better choice, especially since the tunnel houses the fuel tank.”
Front crash forces are fed through a specially designed removable structure. Impacts up to 2.5 mph are taken by the foam located between the bumper beam and fascias, and the beams are attached to extruded rails that extend to the castings. Once the foam is crushed, the beam becomes the next sacrificial element, followed by the longitudinal rails that bolt to the castings. “Structural repairs after a low-speed impact are relatively simple,” says Mees. “You just unbolt the old, damaged structure and bolt on a new one.” How repairs of a more catastrophic nature will be handled in the field is still being determined.
Unlike every other Ford, engine decking is from the top. This allowed Mees and his team to keep the greatest amount of structure possible beneath the massive 5.4-liter V8 and Ricardo-designed gearbox, while reducing to a minimum the superstructure necessary to attach the powertrain to the chassis. “Four extruded tubes go across the top of the engine,” he states, “and they’re easily unbolted in case there’s a need for major service.”
The completed chassis is loaded into a giant CNC set-up that has a gantry arm with a 12-foot span. A majority of locating holes–including those for the superformed aluminum body panels–are cut into the structure at this point, and accuracy approaches 0.0001-in. “Not only does this give the greatest control over the suspension mounting points,” says Mees. “it also guarantees exceptional panel fit.” The “bow tie” roof panel (so named for the shape created by the door cutouts in the roof) is glued into place, while the fenders and doors are bolted to the main structure. “The chassis becomes a giant fixture,” he says, “which controls the relationship between the sections of bodywork.” When complete, the chassis weighs just 205 kg. and reportedly has bending and torsion numbers well above 10,000 lb-ft/degree. (Ford has not released the official figures.) Not bad for a chassis design that went from concept to prototype in a little over seven months.