Direct injection is the technology of the near future for both gasoline and diesel engines, say Bosch engineers. It will keep the internal combustion engine clean, powerful, and efficient during a period when hydrogen power is more dream than reality. By Christopher A. Sawyer, Executive Editor – Automotive Design and Production.
Recently, Bosch executives said out loud and in public what many auto industry executives will only say in whispers to one another: Fuel cells are, at best, a marginal play in the industry for the foreseeable future. Even with continued research and investment, it will take at least 17 years before hydrogen drive reaches mass production, and even then hydrogen-fueled internal combustion engines will lead the way. “Optimized internal combustion engines will remain the dominating power source for passenger cars for some time to come,” says Dr. Bernd Bohr, member of the Board of Management at Bosch, “with market shares of more than 95% through 2015, and 85% through 2025.” Improved fuel injection strategies, he believes, are the key to implementing an optimized engine strategy.
Gasoline Direct Injection (GDI) technology is front-burner research in Europe, but not as hot a prospect in North America. Tight nitrogen oxide (NOx) emission standards have caused many to overlook GDI for the American market since these emissions are greatest when this technology is at its most fuel efficient; that is, during stratified charge running. However, GDI also can be used to produce a homogenous air-fuel mixture that meets proposed U.S. emission standards, and yield a broader torque and power curve. Because the mixture is homogenous, the compression ratio can be increased without fear of detonation, and there is no need for a throttle valve in the intake air stream. This technology was used on both the Le Mans-winning Audi R8s and Bentley Speed 8s.
![]() |
The anatomy of a piezoelectric inline injector. Variations on this technology can be used for diesel or gasoline direct injection engines. |
“A homogenous mixture GDI engine fitted with a conventional three-way catalyst will meet the 2004 SULEV emission regulations,” says Dr. Rolf Leonhard, vice president Development, Bosch Gasoline Systems. Catalyst light-off is improved by splitting the injection between the intake and compression strokes during engine warm-up, and by igniting the mixture later than normal to produce very hot exhaust gasses that bring the catalyst up to operating temperature more quickly. “It takes about half the time it would without this step,” says Leonhard, “and does so without the risk of uneven running or ignition failure.” A more recent strategy, “High Pressure Stratified Charge Start,” injects all of the fuel into the cylinder at high pressure just before ignition, when combustion air is at more than 100º° C. This stratified charge is used on homogenous mixture GDI engines during the start-up cycle, “and reduces hydrocarbon emissions between 30% and 50% compared to a GDI engine with a lower pressure homogenous start-up mixture,” says Leonhard.
Convinced that a stop-start function will provide real fuel savings, but cognizant of automakers’ unwillingness to pay to integrate a separate electric drive starting system, Bosch created “Directstart” for GDI engines. It starts a combustion engine by igniting a fuel-air charge without engaging the starter motor. “Fuel efficiency is improved by up to 5%,” says Leonhard, “and the starting is cleaner, quieter, and faster, while lessening the effort that would have to be exerted by the starter motor in extremely low ambient temperature conditions, or on motors with a large number of cylinders.” OEMs have the option of downsizing their current starter motors, or using a more frequent stop/start schedule with their current designs.
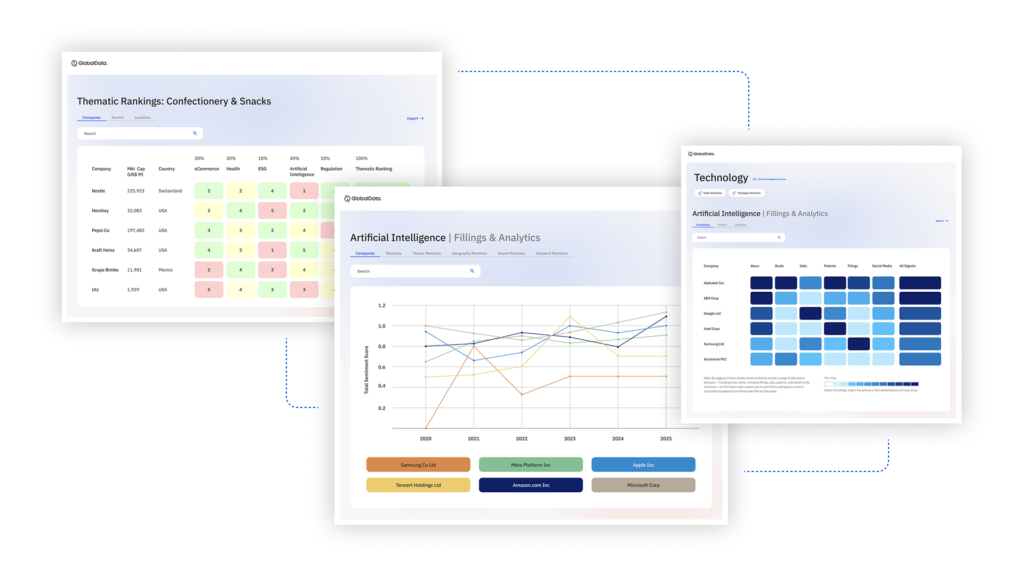
US Tariffs are shifting - will you react or anticipate?
Don’t let policy changes catch you off guard. Stay proactive with real-time data and expert analysis.
By GlobalData![]() |
Bosch’s latest diesel particulate filter is made of sintered metal instead of ceramic, and features wedge-shaped slices packed in a cylinder. They are thinner at their leading edge, and the circumference of the cylinder decreases in the direction of the exhaust gas flow for more even filling. It should last for the life of the car. |
In 2006, the Bosch DI-Motronic/stratified charge combination will be modified such that a centrally located injector in the roof of the combustion chamber will spray an exceptionally fine stream of fuel into the cylinder that can be ignited immediately. Called “Spray Guided Combustion,” this GDI strategy will require advanced fuel injector designs. One version under development has magnetically operated valves with multiple aperture jets. The other uses piezoelectric actuation.
The multiple aperture injectors atomize the fuel through a disc with six to ten holes at its tip. The geometry of these openings can be altered to work with multiple cylinder designs, which should make it relatively easy to adapt this combustion technology to current engines. Plus, the combination of multiple holes and magnetic actuation makes it possible to produce compact, quick-acting injectors that are relatively low cost.
On the other end of the scale sit piezoelectric injectors. They can cycle twice as often as magnetically triggered injectors, so short duration injections can be used to generate mixture flows that are easily ignited. Plus, this injector’s circular side opening creates a cohesive cone-shaped stream flowing from the top center of the combustion chamber, and can be timed to produce a charge of varying density. Its big disadvantage is that it is larger and more expensive than magnetically operated, multiple aperture injectors.
Piezoelectric injectors, however, may prove to be invaluable in future clean diesels because the quick on-off feature gives engineers greater leeway in spray timing and density, which has a tremendous effect on the noise and pollution emitted by compression ignition engines. “Intervals between individual fuel injections can be reduced,” says Dr. Ulrich Dohle, president Bosch Diesel Systems, “which gives greater flexibility in meeting power, economy, and emission goals.” The advanced diesel piezoelectric injector locates several hundred thin crystals within the injector body. The movement of the piezo wafers–they expand in the presence of an electric field–is transferred to the nozzle needle in less than 0.0001 seconds, and its inline design means very little fuel return flow is needed. This reduces the delivery rate and energy required from the high-pressure fuel pump.
“The key to improving fuel consumption and reducing emissions from a diesel engine,” says Dohle, “is to reduce internal engine emissions through optimization of the basic engine design, and improvements in the injection strategy itself.” Adding one or two pre-injections stops smoke generation just after a cold start, which also reduces combustion noise. A post-injection immediately follows the main injection to lower soot emissions, and a further injection can be added to regenerate the particulate filter. Compared to existing magnetic or piezoelectric systems, Dohle expects a common-rail system with piezoelectric inline injectors to cut internal engine emissions by as much as 20%.
![]() |
Directstart adds a stop-start function to GDI engines through the injection and ignition of an air/fuel mixture without engaging the starter motor. It should be on the market by 2006. |
“Heavier passenger vehicles won’t be able to meet the tighter emission standards without systems like particulate filters and a NOx catalyst,” says Dohle. And the injection events must be matched to the requirements of these systems, which is a specialty of the fast-acting piezoelectric injector. Bosch’s latest diesel particulate filter–it enters mass production in late 2005–is made of sintered metal and is designed to fill evenly. This not only increases the filter’s storage capacity, but its condition can be determined more reliably. And unlike ceramic filters, the life of the sintered metal filter equals that of the vehicle itself. Regenerating the filter requires altering the amount of air and fuel fed into the engine, and can be supplemented by feeding unburned fuel into the NOx catalyst during the expansion stroke. This raises exhaust temperatures above the 600°º C necessary to burn the ash trapped by the filter.
|
“The cost penalty for all of the piezoelectric common-rail technology,” says Dohle, “is about 10% to 15%. However, it also improves performance by 5% to 8%, and increases fuel mileage, so we think this is an increase that we can sell to the consumer on its benefits.” With more than 40% of the European new car market–66% in Austria and France–buying diesel cars, luxury automakers offering high-performance V8 versions, and diesel-electric hybrids on the drawing boards for mass production, the market for this technology is secure. But Bosch looks longingly toward the U.S. market as well. “Diesel engines,” says Dr. Bohr, “are perfectly suited to the U.S. market with its long distances, large vehicles, and high-torque engines. And we think there will be an increasing demand for them once they meet future emission standards.” Whether U.S. consumers with their low-cost, low yearly mileage, short-term ownership mindsets agree is yet to be determined.