Un-phased by the furious activity surrounding alternative propulsion systems at other manufacturers, BMW has remained focused only on the task of improving its combustion engines. BMW is pushing technical boundaries with a new range of advanced petrol and diesel engines. Jesse Crosse reports.
This autumn, three new advanced engines will appear on the scene all of which are set to take centre stage in their respective classes. The first is the new 5.0-litre M5 V10 engine, a wholly spectacular device producing 507bhp and 520Nm (384lb ft) torque. The second is a new 3.0-litre straight-six petrol with a lightweight composite magnesium-aluminium crankcase producing 258bhp and 300Nm (221lb ft) and the third, a ground breaking, 3.5-litre, 272bhp straight six diesel aspirated by twin turbochargers and developing an impressive 500Nm (369lb ft) torque from a mere 1,250rpm.
The V10 is touted by BMW as the first ‘high revving’ V10 engine fitted to a production car, capable of a maximum of 8,250rpm. Apart from the number of cylinders, the design of the V10 may be of premium quality but in broad concept at least, holds few surprises. It has four valves per cylinder, bi-VANOS variable valve timing and individual throttle butterflies for each of the 10 cylinders. Like its predecessor, the 4.9-litre M5 V8, lubrication has been taken very seriously and the V10 has no less than four oil pumps driving the ‘semi dry-sump’ system. There are two pumps mounted fore and aft inside the sump and a further two electrically-operated duo-centric units for scavenging oil from the cylinder heads during extreme cornering manoeuvres in excess of 0.6g. The cooling system is equally sophisticated, water flowing transversely across the engine, minimising pressure losses and maintaining equal temperatures on all five cylinders in each bank.
The V10 crankcase is cast at the BMW Landshut foundry from hypereutectic aluminium-silicon alloy containing a minimum of 17 percent silicon. The liners are created by the precipitation of hard silicon crystals so pistons run directly within the uncoated aluminium bores and cylinder banks are arranged at 90 degrees with a longitudinal offset of 17mm to create a compact package. This lightweight crankcase forms the basis for a power unit whose weight-saving features ooze sophistication. Pistons are of iron-coated lightweight aluminium, connecting rods of lightweight high-strength steel and the crankshaft, of forged, high tensile steel. It’s supported by six bearings split between an alloy ‘bedplate’ or ladder frame – a familiar feature on four cylinder engines but a first on a vee engine like this. Cast-in grey cast iron inserts carry the bearing material, supporting a crankshaft which is not just low in weight but short and extremely rigid.
Cylinder heads are also cast at Landshut in light alloy and carry lightweight valves whose stems are a slender 5mm in diameter allowing a reduction in the diameter of inlet tracts. The angle between the valves is quite narrow, just 24 degrees, the exhaust valve being inclined at 11 degrees to the vertical and the inlet valve, 13 degrees. As a result, the camshafts are mounted close together making the cylinder head as compact as possible for neat packaging below the bonnet. There’s no Valvetronic system on this engine, it simply revs too high, but the weight saving efforts extend even to the hydraulic tappets which are prevented from rotating by keys, allowing a narrower bearing surface and reduced weight.
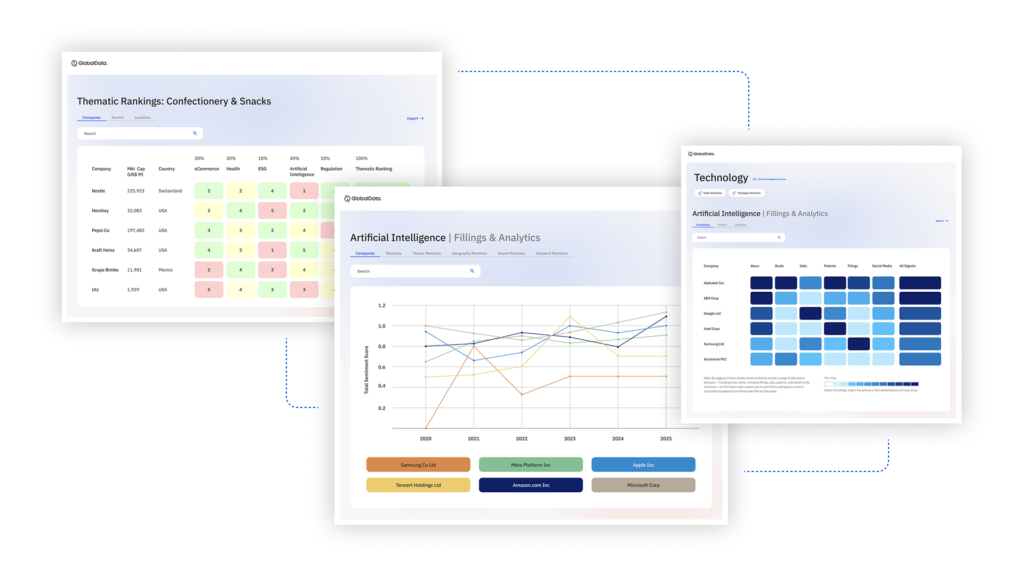
US Tariffs are shifting - will you react or anticipate?
Don’t let policy changes catch you off guard. Stay proactive with real-time data and expert analysis.
By GlobalDataElectronics match the sophistication of the mechanics, with a new, MS S65 control unit containing three 32-bit microprocessors capable of processing 200 million calculations per second. This level of performance exceeds that of the M3 unit developed four years ago by a factor of eight. As well as being capable of extremely complex engine mapping, the system also delivers driver selected ‘normal’ and ‘sports’ maps at the press of a button. The V10 is also equipped with ionic knock control and misfire detection by using the spark plugs as sensors to form closed loop monitoring of the ionised gasses within each cylinder during combustion. Conditions change during the onset of knock or misfire, providing the opportunity for the engine management system to take action. Saab has been using something similar for a number of years.
Overall, what makes this engine capable of such outstanding performance while remaining durable, is attention to detail. Its design may be remarkably straightforward in a basic sense, but advanced computer aided design techniques, manufacturing (components machined to a tolerance of 1/1000mm) and materials make such sophisticated engineering possible. That’s not the whole story, though. As one senior engineer reminded us, “we’ve gained quite a lot of experience during the years in developing high performance engines.”
Bespoke transmission
However, no great engine would be much use without a great transmission so there’s an all-new SMG sequential gearbox to go with it. BMW has set the pace with automated manual transmissions (AMT) whose appeal has stalled somewhat of late due to performance barriers set by relatively slow and fragile synchromesh in the base manual transmissions and also the improvements in conventional autos such as the ZF HP26 transmission. The DSG, dual clutch concept pioneered by VW/Audi and its supplier, Borg Warner, almost provided a final nail in the coffin for the AMT concept allowing uninterrupted torque delivery through each gearshift.
BMW has managed to cling on with its SMG transmission, however, raising the game continuously with every version. The shift speed of most AMTs is limited by several things such as the ability of the synchromesh to react quickly enough, its robustness, speed of processors and actuators and inertia in the engine and transmission. The new M5 will be equipped with a seven-speed SMG (sequential ‘M’ gearbox) designed especially for the job and equipped with both paddle and stick shifting as well as fully auto modes. So dedicated is the new transmission that strictly speaking, the term ‘automated manual’ no longer applies. Although still of a layshaft design, the shift pattern is optimised for sequential, robotised operation and if a conventional mechanical gearlever were installed, drivers would find the layout of the gears very odd indeed.
The transmission has three selector rails rather than a single one, and carbon synchro hubs to enable high-speed gear selection. No less than eleven driver selectable programmes form the ‘Drivelogic’ programmable functions, five of which relate to fully automatic operation ranging from extreme comfort to extreme sport modes. The transmission’s controller works in conjunction with the engine’s MS S65 computer to deliver complex shift functions. For example, in automatic mode the driver can still influence the shift point by modulating the throttle pedal position.
The launch control function in sport mode has grown in sophistication when compared to the M3 6-speed SMG too. For race starts, the driver selects the appropriate programme and holds the gearstick forward to essentially disengage the twin-plate dry clutch. The next step is to floor the accelerator, whereupon the powertrain management systems will set optimum revs for launch which follows when the driver releases the stick. The computers will then modulate the throttle to control slip and shift through the gears as long as the accelerator remains hard down. In previous SMGs it was up to the driver to control launch rpm, wheelspin and gear shifting during launch. Whether or not the new regime is a response to excessive customer abuse with previous models (the subject of a stern health warning in the M3 driver’s handbook) only BMWs warranty department will know.
Overblown diesel
The idea of improving the air supply on diesels to achieve greater output is well understood and seen as a priority now that direct injection systems have come of age. The principal is straight forward enough; increasing the air supply to the lean burn diesel yields more power without sustaining a fuel consumption penalty. That doesn’t mean there are not other hills to climb, particularly the impairment of low speed response through the use of a larger turbine and the cost of overcoming that. One way is to move from a variable geometry to a fixed geometry, electrically assisted turbocharger at about the same or slightly higher cost. The bigger compressor delivers the extra air needed and electrical assistance compensates for the reduced performance of the larger turbo at low engine speeds when exhaust pressure is low. This low speed independence of the compressor also makes it possible to run higher levels of EGR than would normally be possible, significantly improving NOx emissions.
However, though Ricardo and others are experimenting with electrically assisted turbos, they are not yet in the public domain so BMW turned to established technology in order to achieve the same result. It chose a two-stage turbocharger system which it calls ‘Variable Twin Turbo’. Confusingly, neither of the turbochargers are variable geometry but fixed – ‘Variable’ referring to the way the turbos are synchronised to work together both sequentially and simultaneously. Under the control of bypass valves, all the exhaust gasses initially flow through both turbines and air passes through both compressors. At lower engine speeds, the fast reacting smaller turbo provides almost all of the boost while the larger one is gaining speed. But as engine speed increases and the smaller turbo ‘runs out of breath’, a bypass valve progressively redirects most of the exhaust gas through the larger turbine leaving the smaller one to spin in standby mode. At high engine speed, both exhaust gasses and fresh air are directed exclusively through the larger device, a wastegate coming into play as usual when maximum boost has been reached.
It’s an elegant solution, bearing in mind that the mother engine is based on the existing 24-valve, 530d straight-six with second generation common rail injection running at 1600 bar and achieving EU4 emissions. Now though, the 535d produces 500Nm (369lb ft) torque at 1,250rpm rising to a maximum of 560Nm (413lb ft) at 2,000rpm. Maximum power is 272bhp at 4,400rpm, 90 percent of which (245bhp) is retained at a heady 4,800rpm. Thus equipped, the 535d will accelerate from 0-62mph in just 6.5 seconds while achieving fuel consumption of 35.3mpg on the combined cycle.
Lightest six-cylinder petrol
In petrol engines, the emphasis is on power to weight ratio and the new 3.0-litre, R6 engine has the world’s first magnesium-aluminium alloy crankcase which, claims BMW, makes the engine the lightest six-cylinder power unit in the world. At 161kg it is seven percent lighter than the engine it replaces, giving it a power to weight ratio of 1.6bhp/kg and specific power output of 85bhp per litre. At 258bhp, maximum power output is up by 12 percent and yet fuel consumption is down by 12 percent.
The key component in the new six is the composite magnesium/aluminium crankcase. It couldn’t be made entirely from aluminium because magnesium is not suitable for cylinder liners, neither can it carry cooling water without suffering severe corrosion. So the cylinders are formed in a one-piece aluminium insert which is cast into the magnesium shell. The crankshaft is located by a bedplate, or ladder frame, which helps create an extremely rigid, lightweight structure. Weighing just 57 percent of a conventional grey cast iron block, this hybrid is also 24 percent lighter than a cast aluminium block.
The R6 is the first six-cylinder engine to get the Valvetronic valve gear which has already enabled BMW to run first the four-cylinder engine and now it’s V8s unthrottled, variable valve lift controlling the volume of air ingested by the engine. The advantage is a reduction in pumping (throttling) losses which BMW claims gives an improvement in fuel economy of 10 percent in the combined cycle. This second generation Valvetronic can cope with higher rpm than previous versions allowing the R6 to spin freely up to 7,000rpm.
Other features of the R6 include lightweight, hydroformed, chain driven camshafts, a three-stage intake system and electric water pump which conserves energy by operating only when needed. An oil-water heat exchanger raises the oil temperature more quickly thereby shortening the inefficient warm-up phase. BMW claims this to be the first use of an electric pump. Consuming just 200W instead of the usual 2kW, it works completely independently of engine speed and means only one ancillary drive belt is needed instead of two.
All three engines represent a major breakthrough in their respective categories. The V10, exotic though it may appear, is actually more a product of bringing refined engineering techniques to bear on the fundamentals of engine design. With the new turbo diesel, innovative thinking has delivered the next generation while sticking to simple, affordable and well tried components. The R6 combines advanced use of materials and manufacturing techniques with several progressive features, like the electric water pump and the now well-proven Valvetronic system, to punch well above its weight. What all three have in common is that they set new standards in engine design that most competitors can only aspire to.