When Samsung established its ill-starred production plant in South Korea, they set it up with capacity to build 240,000 cars a year, but with the option to extend that to 500,000 if demand dictated. Outsiders understood that to mean that a second assembly line could be built on the site, but Renault have confirmed that all the plant needs in order to build half a million cars a year is a paint shop. The automotive industry is littered with examples of where production capacity being limited by the ability of the paint shop to cope.
BASF can’t eliminate the paint shop today, but they are actively working on their coil-coated steels with the automotive industry in mind, and are tackling the obstacles, both the obvious and more obscure, one by one. The aim is to remove the paint shop capacity bottleneck.
Two years ago, BASF were 7th in Europe in the field of coil coating, and 13th in the world. Then they bought Hydro which moved them up to 3rd in Europe, and followed that by buying Morton, which moved them up into second place in the world behind Akzo Nobel, and with market share now above 10%, BASF Coatings is within 3 points of the leaders. On October 1st 2000, a 50/50 joint venture with NOF Corporation of Japan will be incorporated, and that, coupled with organic growth and the possibility of other strategic acquisitions, has set BASF firmly on the path towards market dominance.
Currently coil coated steels find greater applications in the building industry and the white goods sector, but the potential for the automotive sector is enormous, providing specific problems can be overcome. But BASF is not in a rush, they recognise that major changes in the automotive industry can still take eight or nine years to effect.
Coil coated steel – well over 90% of which would be galvanised for the automotive sector – has now been designed so that steel coils can be run through rollers that paint both sides of the steel at the same time at rates of 200 metres a minute. Generally the outside surface of the steel first receives a layer of zinc, then a pre-treatment layer, followed by a primer and then a thick top coat. The underside of the coil receives the zinc coating, pre-treatment and then a backing coat of foam-adhesive protection paint.
The paint has been designed to act like the steel under extrusion. Thus even the toughest design requirement means that the paint will not crack or split. That is a big breakthrough. So is the fact that the coil coated steel can also be bake-hardened at temperatures of 180ºC. Bake-hardening is an important process in today’s car manufacturing but yesterday’s paints would not have been able to cope.
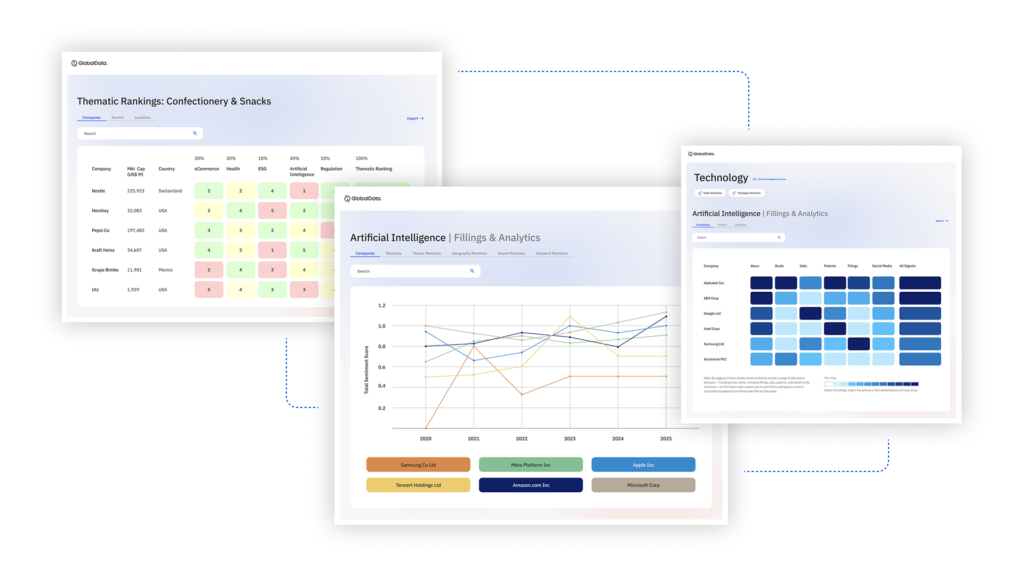
US Tariffs are shifting - will you react or anticipate?
Don’t let policy changes catch you off guard. Stay proactive with real-time data and expert analysis.
By GlobalDataAnother perceived problem concerns spot welding, but BASF points out that aeroplanes do not fall apart in the sky, and they are mainly bonded. Laser welding could be an alternative, but BASF is concentrating on developing bonding techniques that will satisfy the needs of the automotive industry.
Coil coated steel is already finding its way into the automotive industry, finding use on commercial vehicle bodies or mobile homes, but with cars they are mostly restricted to the cladding of the B column or car spoilers, and have not yet found their way into body parts.
Lead times in the motor industry are shortening all the time and there is even talk of just three days being required from the time of an order being placed to delivery to the customer. BASF says that lead times on steel can be four to six weeks, but that any colour can be produced and supplied within twenty-four hours. By situating the paint-making facility alongside the colour coating coiler, BASF believes that even that ambitious three day lead time could be met.
Another potential problem concerns crash repair, a growing need in today’s ever more crowded cities and towns. BASF has already tackled that problem and assures that every colour can be matched perfectly.
Straight edges after stamping create a separate problem, and BASF is working on means to both eliminate or hide straight edges, and also reduce the risk of corrosion. Apart from the straight edges, BASF says coil coated steels already work to prevent corrosion and stone chip problems, and the use of UV curing, and sol-gel systems are even creating paints that self cure scratches and chips once the vehicle is subject to direct sunlight.
BASF points out that many tier-one suppliers now operate from within the assembly plants of vehicle manufacturers, supplying major assemblies on a just in time basis. They believe it is a question of when, not if, the coil coaters take over the steel component stock control for their clients.
BASF is establishing global operations that will enable the company to take advantage of the growth in demand for coil-coated steel (or aluminium) as it becomes evident. Already well-established in Europe and North America, BASF has also set up new operations and joint ventures in South America, South Africa and Asia. Pre-coated materials allow for improvements in quality and also extend warranty agreements. E-commerce allows for customers to monitor the progress of their orders through all stages. There is already a move towards avoiding welding for engine hoods and truck lids. Radiation curing means that there are no emissions, and ovens and cooling sections can be eliminated by curing within seconds on a cold substrate.
BASF lists so many advantages and stresses that they are working to overcome the perceived disadvantages, and they are confident that the next few years will see a huge shift towards coil-coated materials. It is hard to disagree with them.