The use of electronics in vehicles has seen a considerable rise over the last decade. Can the current wiring and multiplexing harnesses within today’s vehicles cope with so many electrical components? What are the alternatives? Matthew Beecham reports.
The amount of electrical and electronic content per vehicle continues to grow as installation of powered accessories and new features increases. Systems such as ABS, navigation and control systems for engines, transmission and exhaust emissions require computers and software. At the same time, many vehicle functions, which had previously been hydraulically or mechanically-activated are being replaced by electrical/electronic actuation resulting in a higher number of circuits and electromechanical and electronic controls and switches per vehicle.
For manufacturers, the increase in the content and complexity of electrical and electronic components also requires a broader overall design perspective. This shift in design philosophy is, as Lear Corp describes it, “moving from the wire itself to the wire ends”, reflecting a view that design should include both the wiring and the electromechanical and electronic devices to which they are connected. Tom Russell, Vice President of Advanced Products for Lear, said: “There are two main factors driving change in the vehicle electrical and electronic distribution systems market. The first relates to the cost pressures that are inherent in the industry. This is driving us to offer more creative solutions providing added value for the consumer. The second aspect driving the market is consumers’ insatiable demand for added features to cars such as memory seats and GPS.”
As the complexity of the wiring harness design moves into uncharted territory that inevitably impacts on the supplier’s design and development capabilities. “When you think about the conventional wiring system architecture, adding a device means adding a new wire,” said Russell. “But we are now seeing more and more inter-connects which are basically protocol based. That means as you add more devices you’re also adding electronic modules. So if you are a wiring harness manufacturer, you need to better understand vehicle electronics as well as electrical distribution. For Lear, that is an advantage because we play in both ends of that game.” Lear Corp’s electronic and electrical distribution systems include wire harnesses, wireless systems and interior control systems. Last year, these products collectively accounted for about US$2.6bn (equivalent to 16% of Lear’s turnover).
“The key is to be flexible,” added Len Tedesco, Vice President of Electrical and Electronic Engineering, North America for Lear. “We understand both levels of technology from the simple state of joining wires together to the more complex high speed communications and wireless systems. Although wireless systems are still costly, we see it as playing a major role in the future.”
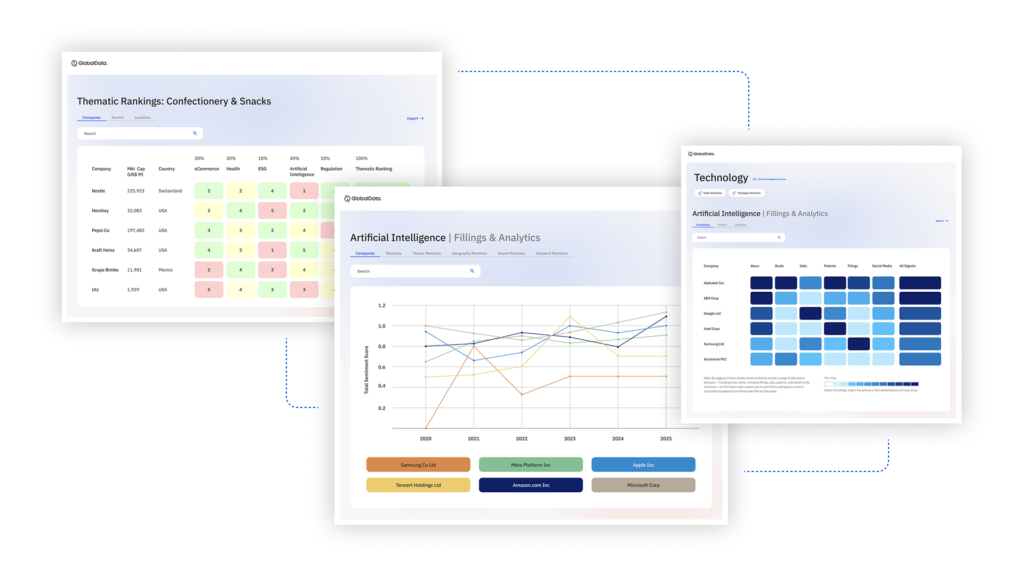
US Tariffs are shifting - will you react or anticipate?
Don’t let policy changes catch you off guard. Stay proactive with real-time data and expert analysis.
By GlobalData“Our OEM customers are looking for a low cost, highly reliable electrical system that is easy to build in their vehicle assembly plants,” said Nick Cassudakis, Director of Engineering, Delphi Corp. “They also want strong engineering support. The better suppliers know how to design products and processes to provide the lowest cost. It is not necessarily about who can thin out the margins the most, but who can come up with the lowest cost process and design. Reliability is crucial. You need to understand the rigours that your electrical system will endure. Unlike a radio or a steering wheel, we don’t want our customers to see the wiring. It just has to work, first time, every time. We pride ourselves in being able to have the design capability that gives you that. That is why we view ourselves as more than just a build to print supplier.” Delphi recently strengthened its position in the global electrical/electronic distribution market by booking more than US$8bn in new business with vehicle makers, of which US$3.6bn relates to new European business.
For Yazaki, the complexity of the wiring harness design has required it to work with the OEMs to develop new tools that allow its engineers to capture even earlier up-front vehicle requirements and information. David Scheffler, product manager for Yazaki North America, said: “Other tools have been developed in-house optimising the manufacturing and logistic strategies to support the OEMs just-in-time and sequenced parts delivery requirements. These strategies include setting up final assembly and warehousing next to the vehicle assembly plant.”
A spokesman for Intedis said: “The increase of complexity in the future is dependent on the increase of available functions with the respective development time. In future, only harness suppliers with good tooling support will be attractive partners for the carmakers.” In 2001, Hella and Leoni formed Intedis (INTegrated Electronic DIstribution Systems), a jointly owned company based in Wurzburg, Germany.
Alternative solutions to the traditional wire harness loom include multiplexing, fibre optics and flexible printed circuit boards.
Multiplexed systems need fewer wires, thereby reducing bulk and weight. Information is shared rather than duplicated, improving service repair, diagnostics and the flexibility to change options.
Fibre optic systems transmit information and data throughout the vehicle for signaling and communication. Claimed advantages of using fibre optics over copper wires include weight saving and higher data quality, reliability and integrity. Not only is it possible to send large volumes of data through the network at the speed of light, it also guarantees excellent electromagnetic compatibility. On the downside, however, fibre optics is more expensive than traditional wire harness technology as it requires more parts to convert electrical signals to light pulses and back again. Nonetheless, with the growth of mobile multimedia features, fibre optic technology is said to be the best method to support bandwidth application, albeit for European applications.
“Our European operations have considerable expertise in fibre optics and are active in applying it in the areas of video and audio transmission,” said Russell. “In the US, however, it is extremely rare to find it in cars. We are simply not pumping this kind of data stream around the car requiring that bandwidth.”
Yazaki sees the current trend in America and Japan, is copper-based physical layer systems while Europe has led the fibre optic based initiative. “Europe will continue to use fibre based systems for some time,” said Scheffler. “There still seems to be some hesitation from America and Japan on truly embracing fibre optic based systems for vehicle networking. American OEMs still have concerns with plastic optical fibre because of the perception that copper-based systems are more robust. We have been developing a next generation optical physical layer that addresses many of the concerns of plastic optical fibre.”
Another novel departure in wiring materials is the flexible printed circuit (FPC). FPCs enable larger sections of the wiring harness to be made in a flat printed circuit board (PCB) configuration. Because of its PCB construction, FPCs can integrate switches and LEDs.
Benefits of FPCs include weight and space saving, increased automation of production, improved consistency of performance and added value through mounting components on the harness. Flexible circuits are said to be more expensive than the wire harnesses they replace, although they can save cost elsewhere in the vehicle’s electrical system. They can also reduce the number of connectors required.
However, given that FPC connectors have current capacity of a few amps, applications are limited. Most applications have been confined to instrument clusters and headliners. Other applications include door wiring, seat wiring, HVAC, antenna and mirror systems. Given that flexible circuits cannot tolerate high temperatures, their use in the engine compartment is ruled out altogether.
Over the past few years, a number of industry groups have emerged aimed at developing common standards in the vehicle electrical and electronic arena. For example, AUTOSAR (AUTomotive Open System ARchitecture) was set up by carmakers and automotive equipment manufacturers to develop a standardised international electric/electronic architecture concept for vehicles. AUTOSAR’s core partners include BMW, DaimlerChrysler, Ford, PSA Peugeot Citroen, Volkswagen, Toyota and component makers Bosch, Continental and Siemens VDO. Its ‘premium’ members (i.e. without a vote) include Delphi, Denso, Hella, Hitachi, Honda, Infineon, Lear, Magneti Marelli, Mazda, Nissan, Porsche, Renault, Valeo, Visteon, Volvo, ZF, and most recently, Johnson Controls. The partnership’s objective is to define and establish a standardised software component specification by August 2006.
|
Since the formation of AUTOSAR in May 2003, other alliances have formed at a national level. For example, Nissan and Toyota recently announced the formation of JASPAR (Japan Automotive Software Platform and ARchitecture). The partners plan to develop network and software specifications, including AUTOSAR specifications.
So is the industry ultimately moving toward ‘plug-and play’, as seen in the computer industry? Taking the idea of multiplexing to its logical extreme, a carmaker could potentially wait until relatively late in the vehicle’s development cycle before committing to specific electronic hardware yet avoid having to delay – or worse, tear up – its electrical architecture in the last minute. “The plug and play approach seen in the computer industry is one we would like to see in the automotive industry,” added Delphi’s Cassudakis. “The AUTOSAR consortium could certainly become the enabler to help us achieve that. But it will take some time to get there. In the meantime, we’re offering a so-called distributed architecture approach. It involves combining electronic modules with power distribution blocks strategically located throughout the vehicle to help optimise wiring to its fullest extent. It is one approach to reducing the number of wires. We are implementing that style of architecture on vehicles that should be launched in the next few years.”