Look through the annual accounts of any automotive company, be it carmaker or supplier, and one of the interesting figures to look out for is the research and development spend as a percentage of turnover. Although it varies from company to company, the percentage is generally within a few points of each other, and it adds up to billions of dollars a year. This feature, written by Chris Wright, is extracted from the bi-monthly Lotus Engineering newsletter, proActive.
But it is a spend that by and large goes unrecognised by the consumer or indeed by the legislators or environmental lobbyists around the world. The automotive industry is regularly hung out to dry whenever there is talk of greenhouse gases, pollution or road safety issues.
None of this takes into account the great strides the industry has made in all these areas over the past couple of decades – always at its own expense and on its own initiative.
A large proportion of the R&D spend in this time has gone on propulsion systems and how to squeeze the greatest number of miles to the gallon while causing the least damage to the environment. While diesel currently remains the best option, the search for the Holy Grail – an alternative to oil-based fuel – continues.
Car makers and suppliers have joined forces in the task of researching and developing fuel cells, the industry’s best hope of being able to sustain individual mobility in the new millennium by delivering ‘clean’ energy to power automobiles.
How well do you really know your competitors?
Access the most comprehensive Company Profiles on the market, powered by GlobalData. Save hours of research. Gain competitive edge.
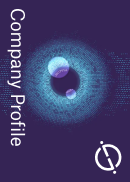
Thank you!
Your download email will arrive shortly
Not ready to buy yet? Download a free sample
We are confident about the unique quality of our Company Profiles. However, we want you to make the most beneficial decision for your business, so we offer a free sample that you can download by submitting the below form
By GlobalDataThe rapid depletion in global stocks of crude oil over the next fifty fifty years, harmful pollutants in the atmosphere – principally Carbon Monoxide (CO) and Nitrogen Oxides (NOx) from the combustion of fossil fuels – and the cost of energy, all pose a threat to the traditional internal combustion engine.
Studies by automotive analysts Frost & Sullivan forecast the automotive fuel cell market will gather pace up to 2008 when revenues will reach up to a sizeable €47.7 million. Small series production could start around this time, gathering momentum to reach revenues of €18.5 billion by 2020 and €52 billion by 2040.
The main competitive arena at the moment is research & development. Frost & Sullivan says: “For companies choosing to be at the forefront of this revolution in automotive powertrain technology, research and development will be imperative, it is where the long term competitive advantage will be created.
“As the race heats up key players are vying to deliver a credible fuel cell powertrain to market within the next two years.”
The US Big Three all have big fuel cell programmes running as do the majority of European automakers. One such programme is Xcellsis, a joint venture set up by Ford, Daimler Chrysler and fuel cell company Ballard Power Systems to produce fuel cell engines.
The road to mass-market depends on a number of things, not least cost. The current cost of a fuel cell engine is in the region of €750 per kW compared to around €20/kW for an internal combustion engine. A significant proportion of the cost element can be attributed to materials. Effective research and development will play a vital role in bringing these costs down and enabling mass production.
Another challenge is the development of the technology and how to produce it – through electrolysis or reformation – and whether this is done on-board or off-board.
Fuel suppliers have yet to map out a clear route to achieve the ultimate goal: a scenario where pure hydrogen can be retailed to users of fuel cell vehicles just as gasoline is today. The industry is facing enormous infrastructure investments, which cannot be recouped in the short to medium term by fuel revenues.
In this sense the auto industry is getting plenty of demand for change, but little help from governments. It is trying to stay ahead of the curve and second-guess any upcoming legislation.
Volkswagen, one of the pioneers of the hybrid car a few years back, is again taking a primary role in improving fuel economy as the leading partner in a €5 million European Union research project into the creation of ultra-light cars.
The initiative, led by VW, boasts fifteen partners, including Volvo, Renault and DaimlerChrysler. Along with a host of research organisations throughout Europe, it is bidding to help develop the new generation of energy efficient automobiles.
Named TECABS – Technologies for Carbon Fibre Modular Automotive Structures – the project aims to provide the technology to halve body weight using low cost carbon composite structures, thereby reducing CO2 emissions.
Meanwhile, petrol engines are becoming more efficient. VW and Renault are working on a 1-litre petrol turbocharged unit designed to produce the same power as a conventional 1.6 litre motor: effectively offering a 30 per cent reduction in fuel consumption.
If the research projects are successful, the next generation environment-friendly cars will have only 30 percent of the current number of body parts, cutting assembly costs to make this an affordable option for the man in the street.
What’s more, research and development can throw up all sorts of interesting problems. For example using a new material could call into question the traditional shape of cars as we know them leading to a new concept in body parts and shape. It could be cigar shaped and car companies admit they don’t know how the public might respond to such a concept.
The partners in the EU project are not the only ones with their eye on lightweight cars.
The Toyota Prius and Honda Insight, both now on sale in Japan, the United States and Europe, use differing combinations of electric and petrol engines at up to 2.75 litres/100km (103 miles per gallon).
To achieve the necessary economies, research into production processes will clearly be key. While it is easy to make a lightweight prototype – Formula One has been doing so for many years – the challenge of mass production will be paramount. High speed and low cost manufacturing production processes using cost effective and quick preform and resin processes will be employed.
But Research and Development is not all about the environment and how to build cars. With increasing technology available, there is an issue as to how the driver can interact with everything now available. After all, car drivers are not jet pilots.
Taking your eyes off the road to fiddle with the radio, navigation system, air conditioner or mobile phone can have catastrophic consequences. But with longer working hours, busy family lifestyles and long commutes sitting in cars stuffed with more and more computerised paraphernalia it is easy to be driven to distraction.
It is issues such as these which tax engineers in R&D departments as well as spin-off issues such as stopping drivers falling asleep at the wheel. This happens a lot and while there are no governments demanding that “something must be done”, the auto industry is quietly going about addressing the problem. And it is complex.
Volvo has been working on a system that warns drivers when they are becoming drowsy or not paying enough attention to the road ahead. Called Facelab, the system uses two dash-mounted spy cameras linked up to eye tracking technology. The cameras monitor the position of the driver’s facial features such as the eyes, ears, nose and chin.
It then calculates where each eye should be and looks for their whites and irises. By measuring how elliptical the irises look compared to how they appear in a computer model of the eye, it calculates the driver’s angle of gaze. Drivers who are about to drop off show characteristic blinking patterns, so Facelab tracks the frequency of blinking to detect fatigue and boredom.
If sunglasses obscure the eyes, the system uses other stored facial data to work out where the driver is looking. The system is therefore capable of tracking the face when the head is quickly turned of when the face is partially obscured. Even the eyebrows and corners of the mouth can be tracked to determine facial expression.
The set-up takes five minutes and involves using the software to select the tracking points on the face. This requires five snapshots of the head, selecting a number of reference and feature locations – again it’s all scary stuff.
Ford has opened a high-tech driving simulator laboratory to study driver workload and distraction issues related to the computerised gadgets that are used in modern cars. The facility allows researchers to measure a driver’s ability to cope with common traffic situations while using mobile phones and twiddling with navigation systems.
Research & Development is not only responsible for new product development and optimization, but also for making sure that spending is tied to customer needs. This ensures value to customers and fiscal responsibility.
It is also an expensive business and why we are seeing more cooperation between vehicle manufacturers as well as with their suppliers. One of the latest such co-operations is the Autosar consortium (Automotive Open System Architecture) is to standardise elements of software architecture for all vehicle areas.
This includes engine, bodywork, chassis, telecommunications and multi-media along with the man-machine interface. Partners in this are Ford, Renault, DaimlerChrysler, PSA Peugeot Citroen, Toyota, Volkswagen, Nissan, Bosch, Siemens VDO and Continental.
Such co-operations are vital if the auto industry is to continue to stay one step ahead of safety and environmental legislation, as well as maintaining the search for alternative fuel sources.
This article was first published in the Lotus Engineering newsletter, proActive. Current and back issues of proActive are available for free download in pdf format here.