Christened DB9 rather than DB8 to avoid the implication of a V8 rather than V12 engine, Aston Martin’s new sports-come-GT car is not only one of the most technically advanced in the world, but the future of Aston Martin rests on its not inconsiderable shoulders. Jesse Crosse looks at the technical highlights of the 186mph supercar.
The birth of any new supercar brings with it a characteristic deluge of eulogising in the press, but in the case of Aston Martin’s new DB9, the enthusiasm is more than justifiable. Not only has the new car met with rave road test reviews – steadfastly refusing to be overshadowed by Ferrari’s 612 Scaglietti launched just a few days before – more importantly it ushers-in a new era for Aston Martin which amounts to a virtual re-birth of the company.
Central to the new beginning is what Aston Martin calls its ‘VH’ (vertical horizontal) vehicle architecture. Vertical, because it will from now on form the basis of every future Aston Martin and horizontal, because it can be applied across the PAG group if necessary. At its core is the bonded aluminium alloy tub which draws on techniques developed originally for the Lotus Elise by Lotus Vehicle Architect, Richard Rackham and his team. Lotus was subsequently invited by Opel to develop a variation on the theme for the Opel Speedster/Vauxhall VX220 and later on, the Aston Martin Vanquish.
Architectural history
Lotus inadvertently started Aston’s aluminium ball rolling back in 1996 with the Elise. Since then the Norfolk company has built 17,500 Elises and in recent years has averaged around 2,500 cars per year, with a further 2,000 VX cars for Vauxhall/Opel. Tubs were originally built by Hydro-Raufoss in Denmark before production was moved to a new plant in Worcester during 1999. From there, completed tubs are shipped to Hethel for final assembly. Extruded sections are manufactured by presses exerting upwards of 2,200 tonnes at a temperature of 490 degrees Celsius. However, the large suspension turrets of the Elise are so substantial they are specially produced using a 100,000 tonnes. Sheet material is produced from 100 percent recycled aluminium processed at 900 degrees Celsius on a hotplate, where steel impurities are removed using electro magnets.
The Elise platform was originally designed as a ‘step-in’ chassis with no doors. As a result, the large chassis rails provided a particular manufacturing challenge due to a fairly large, curved, section and are produced by stretching and pulling the components around a tool. Potential crash damage is catered for by a design which accommodates the fitting of complete replacement sections. Components are bonded together using a heat-cured epoxy glue applied by robot, which never cures outside the oven and can be stored for years. Once the glue has been applied in minutely metered amounts, the components are assembled on a jig by hand. Some joints are merely clamped, but other major parts are fixed to prevent movement using aluminium bolts driven in by electric screwdriver. It is a simple technique, typical of an operation that is steeped in ingenuity. Other touches include tiny ribs on the surface of the extrusion which maintain precisely the right gap in the compressed joint and prevent the glue from being excluded. Once assembled, the chassis is clamped to a jig and cured for 40 minutes at 180 degrees Celsius. That the completed items are robust is beyond question. Original durability testing included 1000 hrs exposure to an acid salt spray (using a solution of battery acid) at 52 degrees Celsius. Lotus says steel bodies would virtually disappear under such conditions.
With such an impressive technology, it’s no wonder Aston Martin turned to Lotus to craft a similar chassis for the Vanquish. The challenge would be quite different this time however. While the Elise and VX220 were rear engine, rear-wheel drive, the Vanquish would be the first front engine, rear-wheel drive car using this architecture, so the transmission and propshaft would need to be accommodated in the middle of the structure. On that score, the Vanquish tub has a carbon fibre tunnel running its length and forming a rigid, structural, backbone, something that was absent from the previous two mid-engine designs. There are also composite crash structures on the front and rear of the tub supporting engine and suspension, still manufactured by Lotus at Hethel.
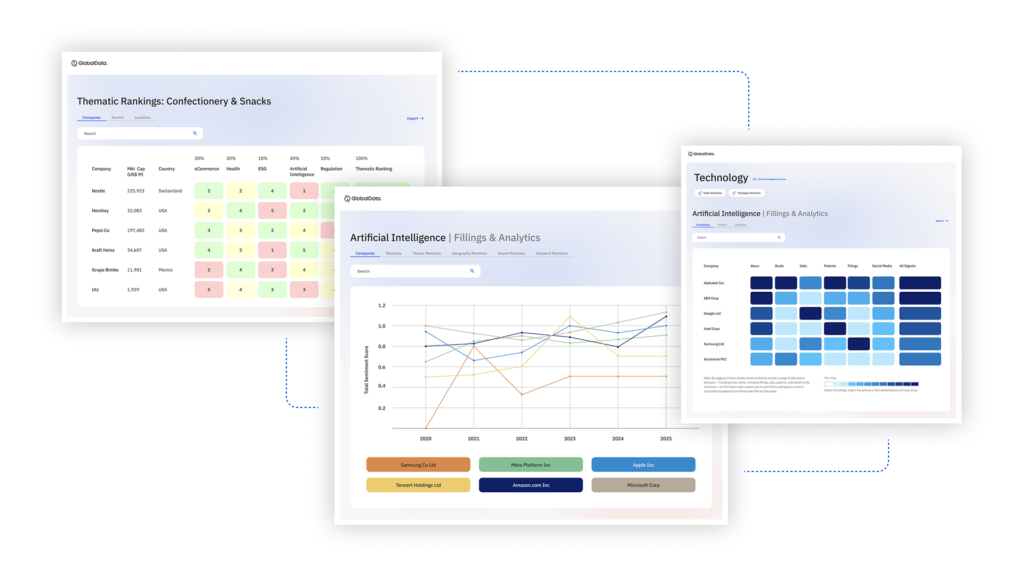
US Tariffs are shifting - will you react or anticipate?
Don’t let policy changes catch you off guard. Stay proactive with real-time data and expert analysis.
By GlobalDataGoing it alone
With the DB9, however, Aston Martin is flying solo, its aluminium architecture a direct collaboration with Hydro-Raufoss in Worcester where the tubs are manufactured alongside those of the Vanquish. Once complete the two lines part company, Vanquish tubs being shipped to Newport Pagnell and the DB9 components to Aston Martin’s new plant at Gaydon. Construction is very similar though and the elements of the tub (which Aston prefers to call a ‘frame’) joined by adhesive supplemented by self-piercing rivets. Body panels are assembled onto the frame at Gaydon, again using adhesive which is applied by a single robot before being cured using hot air.
Upper and lower C-pillars are joined using an advanced ultrasonic welding technique at a frequency of 20kHz. The high frequency vibration, generated by a ‘sonotrode’, causes a molecular bond 90 percent stronger than a conventional spot weld. The process is so far unique to Aston Martin and has huge advantages in that no heat is generated, so there’s no oxide contamination and most important, no deformation of the materials. The remainder of the structure is of equally lightweight materials. The one-piece windscreen frame (another first) is cast in aluminium, the steering column and inner door frames are from magnesium alloy and the bonnet, roof and rear wing panels are ‘superformed’ in aluminium before being hand finished. Both the front wings and bootlid, however, are manufactured in composite materials while the propshaft is from carbon fibre.
The front suspension picks up on a cast aluminium subframe, as does the rear suspension along with the transaxle. Wishbones are all forged from aluminium and damper bodies are also made from aluminium. 19-inch alloy wheels, flow formed rather than cast to save around 1kg per wheel, wear specially developed Bridgestone tyres. Brake discs are ventilated and grooved in preference to cross-drilling, a detail which Aston Martin considers adds greater efficiency and an improved ability to shed brake dust. Unusually, brake calipers are each manufactured from a one-piece casting for improved rigidity. The body’s torsional rigidity is immense, at 27 kN/degree, twice that of the DB7 and 25 percent lighter too.
Powertrain
The DB9’s engine is a development of Vanquish, quad-cam, 48-valve, V12 which contrary to rumours at the time, was not a hybrid of two V6 Ford Duratec engines. That said, the original V12 did make use of Duratec pistons, connecting rods and valvetrain. The engine originally evolved in two stages. Stage one developed 420bhp but in Stage two Vanquish form, that was upped to 460bhp and 18.1kg removed from the engine internals, more than half of which involved rotating parts such as the crank, camshafts and flywheel. Inertia has been reduced still further for the DB9 and the engine’s characteristics modified to make it even more tractable. Maximum power has been reduced to 450bhp at 6,000rpm but 80 percent of the 570Nm maximum torque (developed at 5,000rpm) is produced from just 1,500rpm. Despite this supposed blunting of the V12’s teeth, the manual DB9 still accelerates to 60mph in 4.7 seconds and 100mph in a breathtaking 10.8 seconds. As with the Vanquish each bank of cylinders is equipped with its own engine management unit, both of which are integrated with the transmission and drive-by-wire throttles. Overall weight of the engine is a further 11.8kg lighter than the Vanquish version and positioning is well back to help achieve the DB9’s 50:50 weight distribution.
Aston Martin has opted for a transmission solution that is at the same time both well tried and radical. Well tried, because the sublimely effective ZF HP26, six-speed automatic gearbox has been in use by BMW and Jaguar for some time, and radical, because on this occasion, the Lepelletier gear train sits inside a transaxle casing specially developed by ZF for the DB9. From the driver’s perspective, the transmission emulates an automated manual with magnesium ‘Touchtronic’ paddles for shifting in manual mode, and simple, push-button selection of drive, park and reverse. Software has been developed by Aston Martin to deliver super-fast shifting that is easily a match for most automated manual systems if not for the brutally quick SMG transmission of the extreme BMW M3 CSL. Unlike the CSL, however, the DB9’s ZF transmission delivers a high degree of refinement at all times and in fully automatic mode, is naturally far superior to any single clutch automated manual yet developed – essential to ensure success in the US market. Software details include engine blipping on the downshift, something Aston Martin believes is a first on a torque converter-based gearbox. Transmission and engine are connected by a cast aluminium torque tube and drive is via the carbon propshaft which is both light in weight and exceptionally rigid. A manual six-speed will be available in conjunction with a twin-plate clutch, developed by Graziano and claimed by Aston Martin to have the best gearchange action of any manual transmission in the world.
Partners and manufacturing
Electronics naturally include EBD (electronic brake force distribution) ABS and standard DSC while a not-so-common feature is the use of LEDs for rear light clusters. The overall electrical system was developed with Volvo and is based on the Swedish manufacturers multiplex design. Volvo also partnered Aston Martin on safety, providing development and testing resources at Gothenburg. No less than 25 of the 93 prototypes were eventually crash tested. Other test locations included Nardo, Death Valley, Northern Sweden, the Cranfield wind tunnel and Ford’s Dunton R&D facilities.
2,200 DB9s will be constructed at Gaydon this year (including a few Volantes from late summer onwards) and 300 Vanquish at Newport Pagnell. Next year, DB9 output will remain at 2,200-2,300, but 40 percent will be DB9 Volantes and the balance, Coupes. In the middle of 2005, the V8 Vantage comes on line at Gaydon of which a further 2,500-3,000 a year will be built, bringing total production to something over 5,000 units. 200 man hours are spent on each DB9 compared to 450 hours for the DB7, yet for the well heeled, the price is a tantalising £103,000-£109,000. With world-class technical architecture and assembly lines now firmly in place, plus its own bespoke engine plant at Cologne, Aston Martin’s future looks more than bright; incandescent would perhaps be more appropriate.