
Volvo Car Group has been conducting extensive tests – working with UK-based tech firm Flybrid – on flywheel-based KERS (Kinetic Energy Recovery System) technology that it is claimed can yield fuel consumption savings of up to 25%. Ian Adcock took a closer look for just-auto.
Two dates are concentrating the mind of engineers like Dr Tomas Hannebäck, Volvo’s director of transmission engineering: 2020 and 2025. Both are years when seismic changes will be made to fuel consumption demands and CO2 levels, with 2025 almost certainly only being achievable with some form of hybridisation of the internal combustion engine whether it’s petrol or diesel.
“There are three areas we can work on to meet these challenges: (i) the engine and transmission to improve efficiency, reduce rolling resistance and (ii) better aerodynamics combined with lower weight, and (iii) recover energy. Vehicles waste energy under braking, so if you can recover that you reap benefits for improved efficiency and flywheel technology can help with acceleration or maintain speed under normal driving.”
In collaboration with Flybrid, Torotrak and SKF, and with financial backing from the Swedish government’s Energy Agency for the EUR2m project, Volvo Cars has built a prototype S60 powered by a 254hp five-cylinder T5 petrol engine with a Flybrid Kinetic Energy Recovery System (KERS) flywheel built into its rear axle.
Under braking, kinetic energy – which would otherwise be lost as heat – is transferred from the wheels to the KERS, and is used to spin a 6kg carbon fibre flywheel at up to 60,000 rpm. When the car starts moving off again, energy stored in the spinning flywheel is transferred back to the rear wheels via a two-stage Torotrak toroidal transmission, to either boost power or reduce engine load. The combustion engine that drives the front wheels is switched off as soon as braking begins. The energy in the flywheel can then be used to accelerate the vehicle when it is time to move off again or to power the vehicle once it reaches cruising speed.
According to Hannebäck this can add up to 80bhp whilst cutting fuel consumption by 25% and reducing zero to 62mph time by 1.5 seconds to under five seconds; CO2 levels on the NEDC cycle can be cut to 157 grams/km.
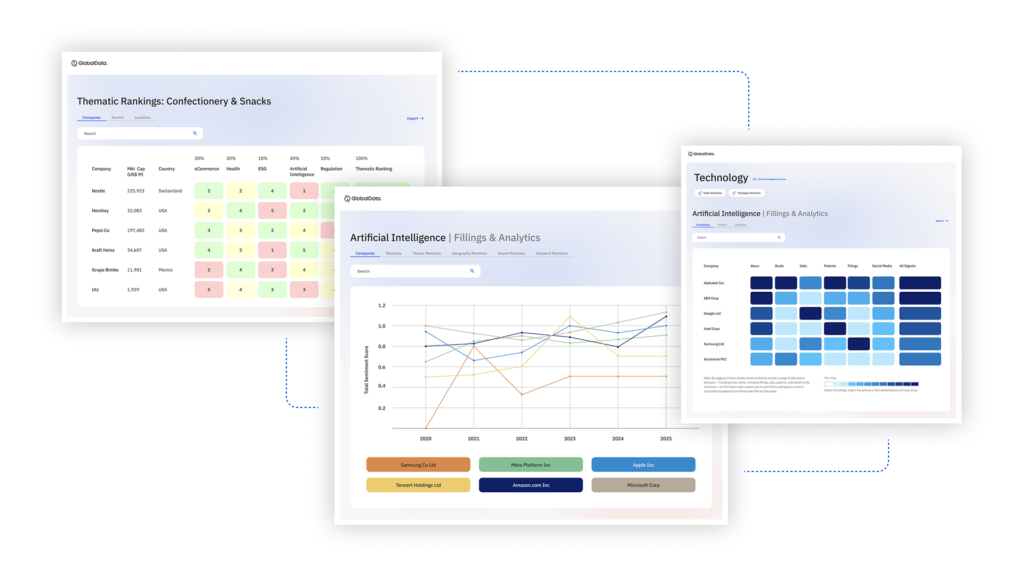
US Tariffs are shifting - will you react or anticipate?
Don’t let policy changes catch you off guard. Stay proactive with real-time data and expert analysis.
By GlobalDataEssentially the packaging is carried over from Volvo’s plug-in hybrid although some of the componentry is visible in the boot; future platforms will be package protected for both plug-in and KERS installations. “We don’t know what the take-up will be, but we envisage that customers will be able to decide when ordering their car which hybrid technology they want and it will simply be installed on the line,” said Matthias Jorgensson, Volvo’s technical leader for Propulsive Drive.
Whilst this prototype features a two regime Torotrak transmission for optimising the system between eight and 50 km/h and then to V-max, future installations will likely have only a single speed and could be packaged together with the front-wheel drive transmission rather than in the rear axle. This will reduce the parts count by 40% with a subsequent reduction in component and manufacturing costs which are already very attractive compared to battery-hybrid systems as Flybrid’s commercial director, Jon Hilton, emphasises. “Even with the current rear-wheel drive application it’s between a third and a quarter the cost of an electric hybrid; if fitted to the front it would be 40% cheaper again, a sixth of an electric hybrid, and that’s a big saving for the OEM and the end customer.”
Moreover, KERS is inherently more efficient than battery storage systems, it is claimed. “Storing energy in batteries is less than half as efficient as KERS since you are converting mechanical energy into electricity which is then converted into chemical energy – the battery. The whole process then has to be reversed to release the energy. With KERS you are harvesting and storing mechanical energy, the only losses incurred – about 30% – are through the gears, bearings etc.” says Hannebäck.
The system is basically the same as that which appeared on a TSB-funded Jaguar XF in 2010, but with Flybrid’s own ECU controlling the KERS and transmission rather than the Prodrive system on the Jaguar. According to Hilton, developing that so the KERS and petrol engine blended seamlessly was a major challenge although it was made easier by Volvo’s experience from its own hybrid systems. “That was one of the bigger challenges. The high level management is not straightforward as it’s a lot to do with strategy. On the braking side you simply capture everything you can because there is a very short window to harvest the energy and if that isn’t done, then it can’t be used.
“On the energy release side Volvo has done a lot of work with both Eco and performance modes. The flywheel can also be charged from the engine and with the engine off fully-charged KERS will power the car for about half a mile at a time.”
The challenge now is to get a Tier 1 supplier sufficiently interested in the system to put it into production which is easier said than done.
Manufacturing the flywheel is a highly precise process, so much so that Flybrid – now part of the Torotrak group – has invested GBP2m at its Leyland facility to produce flywheels. With some funding from the Advanced Manufacturing Supply Chain initiative, Hilton predicts Flybrid will be producing about 3,000 flywheels a year by 2018. “Flybrid developed the technology to make them including a flywheel balancing machine. The balance is critical, and our machine is ten times better than anything else available and is capable of balancing to true centre of gravity within 0.2 microns of the true rotational centre line,” says Hilton.
“That’s how you get the service life because the bearings have got pretty big load capability and the load that comes from out of balance is tiny otherwise you would never get 150,000 miles durability at such high speeds.”
A brief drive of the prototype was enough to convince that KERS could be a key to downsizing future engines. It would be perfectly feasible to have a 30kW engine augmented by an 80 or 100kW KERS in a family-sized saloon that would meet future emission levels with acceptable performance and greatly improved fuel efficiency.
See also:
SWEDEN: Volvo Cars testing Flybrid KERS technology
INTERVIEW: Jon Hilton, MD Flybrid Systems
UK: Torotrak finalises Flybrid Automotive acquisition