It is unusual for an established automotive technology such as turbochargers to see entirely new entrants joining the fray. Barriers to entry are high, both in terms of technology experience and embedded customer relationships which can be difficult to dislodge. However, Continental appears to have bucked the trend in the turbo market, writes Matthew Beecham.
Continental began in 2006 by focusing on the development of a small turbocharger. Five years on, its first turbochargers are for Ford’s 1.0-litre EcoBoost gasoline engine. The supplier’s turbochargers have been designed specifically for small engines, which fit Ford’s concept.
“For small gasoline engines, we have developed a completely new turbine stage for these turbochargers,” said Udo Schwerdel, head of Continental’s turbocharger product line. “The reason we did that was to get a better understanding on how to use the pulsation energy of the engine for our turbine. Our new turbine stage has a number of benefits when it comes to the moment of inertia [referred to as] the turbo lag. It also improves the efficiency of the turbine stage. So, if you have the opportunity to drive the Ford Focus fitted with a three cylinder engine, test it very hard and then ask yourself, “Did I really feel a turbo lag? I´m very sure you will not feel it at all.”
Continental’s turbos feature a unique rotor design, a nickel-free housing, and is made in a new automated manufacturing process. Those elements combine to offer reduced cost and improved reliability. Its current turbo concept is claimed to be so scalable and flexible allowing it to be adapted to other engine sizes and outputs thereby forming a basis for a whole new generation of novel turbochargers made by Continental.
“It is one of the real benefits,” added Schwerdel. “We designed this turbocharger – or this whole concept – right from the beginning with the capability to assemble [it] fully automatically. And with that concept, we are able to go for three different families. Consequently, we are very scalable to cover almost the whole market when it comes to gasoline engines.”
The scalability, flexibility is one of the things that give Continental an edge that has allowed it to open up new business in the Europe turbo market.
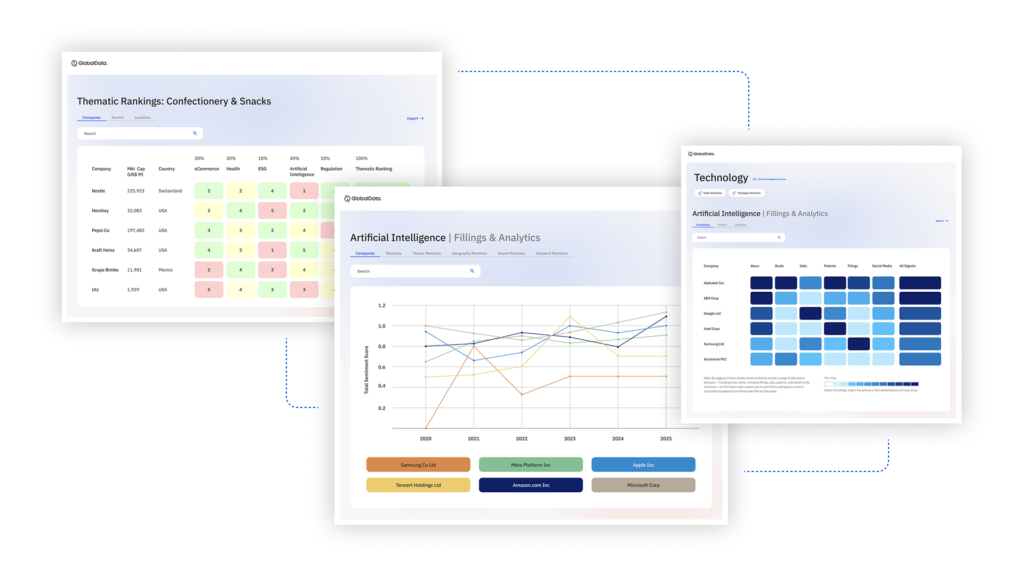
US Tariffs are shifting - will you react or anticipate?
Don’t let policy changes catch you off guard. Stay proactive with real-time data and expert analysis.
By GlobalData“The OEs are really looking for a new approach,” says Schwerdel, “especially coming from newcomers since they have to demonstrate something new. In particular, the OEs are looking for new manufacturing processes in order to further reduce costs and improve quality quite dramatically. That is something that gives us a very strong position as a newcomer in our discussions with OEMs. Fully automatically assembly process with a sophisticated traceability concept offers a significant improvement product quality.”
Continental’s development team sought improvements over existing turbochargers in several aspects, including reducing carbon-dioxide emissions, reducing costs and improving transient behaviour to cut down on turbo lag.
To keep CO2 emissions to a minimum, Continental’s turbo uses electric wastegate actuation, which requires one-third less force to open and close than a traditional setup. Electric actuation generally is faster and allows more freedom to calibrate and close off the wastegate. By ensuring it’s open or closed as needed, fuel consumption can be reduced by increasing engine and turbo efficiency. Continental added a new twist by reducing the size of the wastegate and actuator. The smaller size allowed the supplier to integrate both components into the compressor housing.
The fact that automakers like to have multiple suppliers for critical components allows relative new entrants like Continental to win new business, too. “During our discussions with OEMs, they want us to give them our best turbocharger hardware for their thermodynamic tests. Now, what does it mean if you compare an established turbocharger manufacturer with the newcomer? An established manufacturer can always go and pick up something he has already on the shelf and make some small modifications if necessary. A newcomer doesn’t have anything on the shelf; we have to go and design specifically for the need of the customer. Of course it is a lot of frontloading work but it put is in a winning situation.”
To date, Continental says it has focussed its efforts on the small gasoline engine market and carried out some conceptual studies only on diesel applications.