At a recent ‘EV Battery Tech 2010’ conference held in London, the proceedings looked beyond prospects for electric vehicles themselves to consider issues associated specifically with batteries. These included their technology, cost, ease of manufacturing, raw material supply and recycling. Ian Henry was there to report for just-auto. This is the second of a two-part article (part one was published on Friday, May 21).
Battery production cost reductions required
In addition to presentations from the VMs, a number of highly technical presentations dissected the core technology and the costs involved in EV batteries. Sanko Lan of the National Taiwan University of Science and Technology presented on the costs of Lithium-Iron-Phosphate (LiFePo4) batteries. He explained the batteries’ cell structure, with the alternate layers of carbon, copper foil, LiFePo4, and aluminium foil, with alternating cathodes and anodes, all surrounded by electrolyte material. Then in breaking down the material costs of an EV battery, he told the conference that the main potential for cutting material costs comes from the 25% material cost which is accounted for by the LiFePo4, the cost of other materials reportedly already having been reduced to the minimum already.
Given that LiFePo4 represents around 14% of total battery costs, in order to cut battery costs, other cost cuts are required. In this regard, Prof. Lan highlighted the need to make the battery production process more automated and crucially to make progress in terms of standardising battery cells. In many ways, this could be the key issue for the industry. The commoditisation of the battery cannot really come soon enough.
Standardising or commoditising batteries will be essential
The VMs and battery suppliers are working alone and together, developing different versions of essentially the same technology. While the technological competition breads innovation, there is the disadvantage of the lack of standards at the present time; as yet, there is no standardisation in terms of charging technologies and protocols, nor is the size of the battery pack or how they are fitted into vehicles yet done in a standard way. At some point, especially if EV batteries are to be quickly changed at service stations, some standardisation will presumably have to emerge. Today, however, the industry is some way away from establishing the requisite standards.
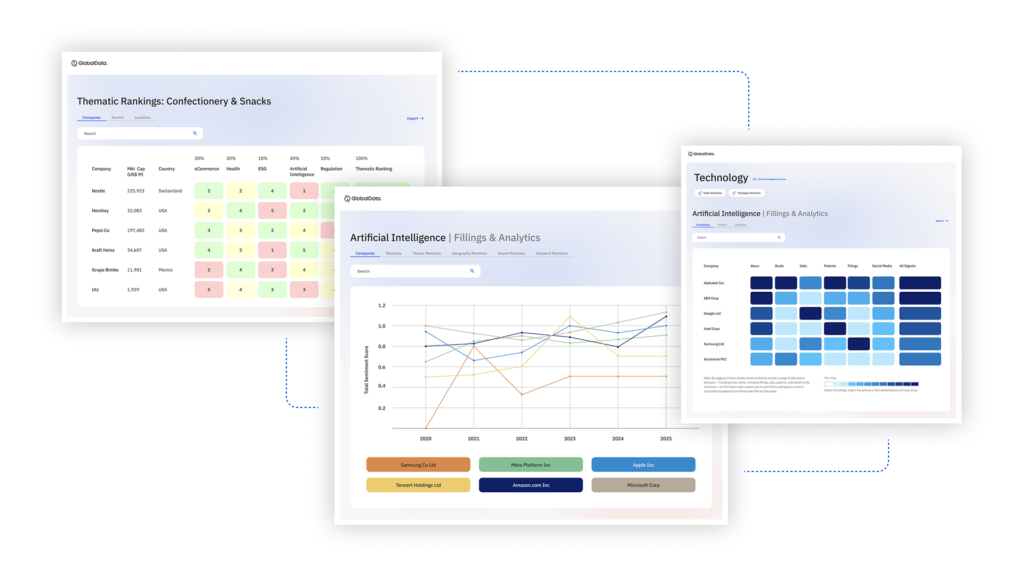
US Tariffs are shifting - will you react or anticipate?
Don’t let policy changes catch you off guard. Stay proactive with real-time data and expert analysis.
By GlobalDataRecycling has a major role to play – and concentration of resources is a worry
Recycling of batteries and their constituent materials is a further major challenge facing this emerging industry; Recupyl presented on this subject, starting with some somewhat worrying figures about the apparent length of resource supply for certain metals – according to Recupyl, there is less than 30 years’ worth of sustainable supplies of tin and silver and less than 50 years’ of gold, zinc and lead for example. While there are limited resources of some metals on one hand, there is also a notable geographic concentration of supply of others, especially lithium which is the crucial constituent of EV batteries.
According to Recupyl, Chile and Argentina currently represent 75% of all lithium production and together with Bolivia, these three countries represent 81% of the world’s known lithium deposits. Other presenters suggested there were supplies of lithium elsewhere, but the concentration of resources in a small number of countries is an issue of concern, especially in view of the potential for geo-political issues to cloud supply arrangements in the long run; similar concentrations of other rare metals, such as Brazil representing 90% of the world’s known supply of niobium and China having around 90% of the world’s known supply of rhodium, mean that securing use of these materials is crucial. Moreover, recovering and recycling material when their original applications come to an end is essential.
Recupyl wants the world to think of moving away from traditional mines in the ground to what it calls “urban mines”; this would involve recovering as much material as possible from discarded items, be they batteries, computers, cars, white goods and more. Putting some figures onto this idea, Recupyl notes that the basic simple batteries that we all use today represent around 120,000 tonnes per year of waste material in Europe; this could be converted into 24,000 tonnes of zinc, 20,000 tonnes of manganese and 18,000 tonnes of steel, all of which can be re-used, if “harvested” from the “urban mines”.
In terms of lithium batteries, the lithium compound represents almost 30% of both the weight and the value of current EV batteries, so ensuring a system for collecting and recycling this material is clearly beneficial. Recycling won’t solve all the long term issues surrounding scarcity of supply but it will help and it should be a very effective process. Recupyl reported how to generate one tonne of lithium, primary producers need either to mine 250 tonnes of ore or extract it from 750 tonnes of brine; or through recycling, one tonne of lithium can be extracted form just 28 tonnes of existing lithium batteries from defunct mobile phones and lap top computers.
Recupyl is already very active in this area which fully industrialised facilities recovering lithium in Singapore and England and new lines due to open in the USA, Italy and Japan during 2010.
In the end …
And in summary, what did we really learn from this conference. To me, a number of conclusions can be drawn:
- The trend away from conventional powertrains is unstoppable, but equally the VMs have made – and will continue to make – real advances in the emissions and environmental performance of conventional powertrains; so, unless legislation or regulations are used to ban vehicles with tailpipe emissions, the conventional powertrain configuration will remain dominant.
- The absence of definitive and standardised charging and battery changing infrastructures on a global – or even a regional scale in Europe – will limit the mass market potential of pure battery EVs or even plug-in hybrids. Unless consumers are forced to install their own charging points at home (possibly all new house builds could include a requirement for a power socket for charging a PHEV or a full BEV?), the largest part of the market will remain with known technologies, ie conventional powertrains, albeit with low emission engines, or with hybrid technology which is at least known and reasonably well understood – and does not require a plug and independent power source.
- The cost of batteries for full EVs has yet to come down to a level where they can be fully integrated into the purchase price of the car – in the medium term, batteries will almost certainly have to be leased.
- Concerns over the life-in-use of batteries remain, covering both the public’s perception of how long they will last on a single charge and how long they will last before their state of charge performance resources and they need to be replaced; moreover, long term concerns exist regarding the security of supply of raw materials – means to recycle and recover crucial materials need to be established.
There is still a lot for the industry to do before things settle down!
Ian Henry
[Please note that this is the second part of a two-part article. To read Part 1 click here}