As the purchasing manager leaves, new challenges arrive for the new GM, says SupplierBusiness.
Last Friday’s news of Bo Andersson leaving General Motors did come as a big surprise for the industry, although it was somehow likely at a time when clean sweeps of management layers are becoming more common as two of the Detroit Three restructure themselves under Chapter 11 and new challenges become apparent for the future.
Andersson, Group vice-president since 2007 and head of Global Purchasing and Supply Chain of General Motors since 2001, reportedly left the car maker to pursue new career opportunities after a 22 year stint at the Detroit car maker. GM’s CEO Fritz Henderson has said that “Bo has made tremendous contributions to the development of our global purchasing and supply chain strategy as we have globalised our product line portfolios and manufacturing footprint”.
There is no possibility to cast doubt on the above mentioned contributions that the former Swedish Army officer made to General Motors. Overseeing a purchasing budget of US$86bn – as large as the GDP of Morocco – is definitely not an easy task. It is even more difficult when the purchasing department has to cope with a diverse and fragmented supply base, with facilities on all continents as a consequence of GM’s “going global” policy. Finally, but most importantly, the financial context in which this purchasing executive was working is being shaken up. General Motors has been in dire straits for a long time.
Its relentless cash burn, which finally led it to bankruptcy, forced the car maker to exert high pressure on the purchasing department to squeeze out suppliers in an attempt to maximise cost savings and reduce expenditure on activities such as supplier development, a feather in the cap of Japanese car makers. Andersson worked according to the guidelines and demands he received from Wagoner and Henderson, GM’s former CEO and CFO (now CEO) of GM respectively.
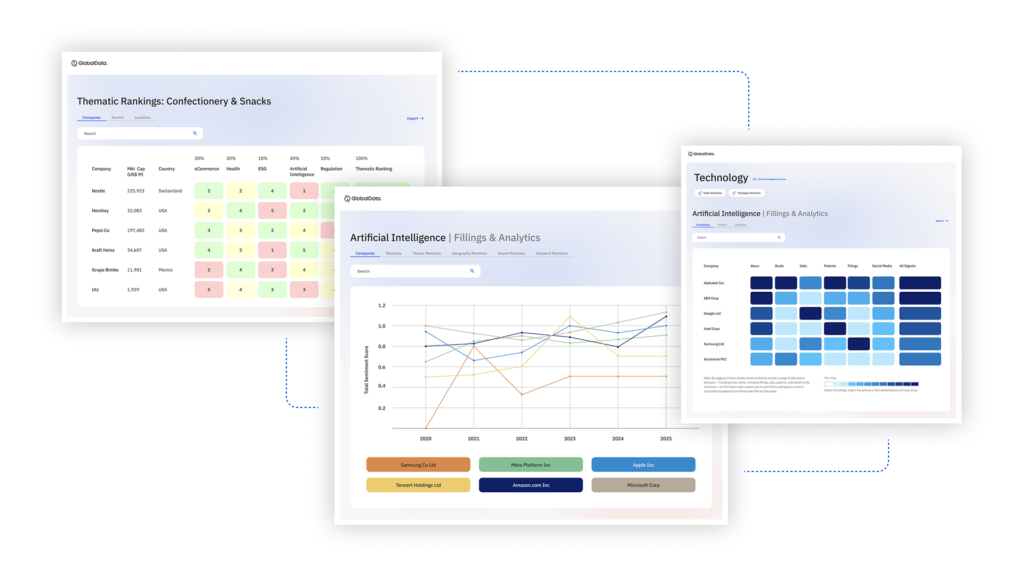
US Tariffs are shifting - will you react or anticipate?
Don’t let policy changes catch you off guard. Stay proactive with real-time data and expert analysis.
By GlobalDataHowever he also had his own straightforward and outspoken approach to supplier management, which was often seen as aggressive by suppliers. With that said, Andesson was able to improve relations with suppliers. Taking into consideration our OEM supplier relations index since its creation in 2005, it is clear that GM managed to improve its relations with suppliers over the last four years and has recorded significant improvements, regardless of its growing debt pile and of the doubts arising among all stakeholders (including suppliers) about the car maker’s ability to continue as a going concern.
Other car makers such as Chrysler and even the much-adulated Toyota deteriorated. Nevertheless GM was ranking poorly, notwithstanding the improvements. The backslashes of the Lopez era, when the seeds of disastrous relations with suppliers were sown, were still there when Andersson took the reins of the purchasing function of the then world’s biggest car maker.
The Sweden-native executive was able to improve on what was a very negative reputation of GM among suppliers, without having complete free hands. Andersson was really called upon a mission impossible also because of the influence of the UAW (United Auto Workers), the largest labour organisation in the US, on the operations of the Detroit car makers. In many cases the UAW requested components assembly to be carried out in the OEM’s plant instead of suppliers, thus limiting the possibilities for the automaker to reap the benefits and efficiencies of outsourcing certain operations to suppliers. This represented a serious obstacle towards the achievement of efficient and streamlined procurement and production operations.
Under the new corporate organisation of the revamped GM, the UAW will retain and possibly even increase its decision making power over the management of the OEM which will hopefully emerge from the bankruptcy. In addition to decisions regarding the allocation of product lines to assembly and stamping operations, the UAW will drive the procurement policies of the new GM, with its 17.5% stake. In a UAW document it became clear that joint-decision making between the management board and the union will occur for sourcing strategies, cost structures and technologies. The agreement between the two parties calls for the new GM to hire an independent consultant in the evaluation of ‘insourcing vs. outsourcing’ of GM operations so it retains that what can be done competitively within the automaker’s operations. Lots of constraints are therefore ready to be enforced on the new management layers which will be laid down in the following weeks. Bo Andersson had a difficult task, but whoever his successor is, he’d better be prepared to roll up his sleeves.
This article was supplied to just-auto by SupplierBusiness, an IHS Global Insight company.