Torotrak, developer of the revolutionary infinitely variable transmission (IVT), has been undergoing an intense period of change in the past 16 months. Mark Wilkinson reports for just-auto.
Dynamic new leadership
Dick Elsy, ex-Product Development Director of Jaguar, was appointed Chief Executive Officer of Torotrak in January 2003, after a long search for a new CEO following the departure of Maurice Martin. Elsy then brought in James Batchelor (ex-BMW and Trafficmaster) as the new Commercial Director and “the company has transformed itself from a research-based business into an applications business,” (applications engineering and testing for customers) says Elsy. This new blood has not only increased the company’s exposure to the outside world where it matters (at board and chief engineer level), but it has also driven further the development of the IVT, resulting in a range of improvements to make it truly competitive with the best six-speed automatics (6AT).
The functioning of the IVT
The key to the IVT is its variator, which uses an arrangement of input/ output discs and six sets of rollers to offer an infinitely variable effective ratio that can shift from Forward through to Neutral and then into Reverse without a clutch or torque converter. The effective ratio is altered by adjusting the angle of the rollers that rotate inside the toroidal spaces created by the curved faces of the input/output discs.
The variator offers a wide (7:1) range of effective ratios, but the geared neutral, coupled with very high overdrive, produce an effect rather like that of a nine-speed transmission, with ultra-low and extremely high effective ratios at either end of the normal driving scale. Even with this greatly extended range, the IVT part-count is far lower than that of conventional transmissions (which contain multiple epicyclic gears, sprag clutches, torque converter etc). IVT’s continuously-variable effective ratio helps to keep the engine in its ‘sweet spot’ (optimum emissions/fuel economy) for as long as possible whilst retaining the ability to offer instant response should the driver need to accelerate suddenly. Another benefit is the extremely low engine speed at cruising – around 1,200rpm at 80mph, for instance – for optimum fuel economy.
At the moment, Torotrak’s demonstrator Ford Expeditions are still equipped with the Series III development IVT transmission, which handles the 5.4 litre V8’s 200kW output with ease. Nevertheless, this IVT is a development unit and as such, it is over-engineered, with attachment points and sensor locations all over its casing. In fact, the Series III development unit weighs 240kg, similar to that found in a single-decker bus, and is almost as big.
How well do you really know your competitors?
Access the most comprehensive Company Profiles on the market, powered by GlobalData. Save hours of research. Gain competitive edge.
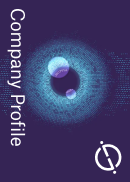
Thank you!
Your download email will arrive shortly
Not ready to buy yet? Download a free sample
We are confident about the unique quality of our Company Profiles. However, we want you to make the most beneficial decision for your business, so we offer a free sample that you can download by submitting the below form
By GlobalDataEven though the Series III development unit runs as smartly as the latest generation six-speed conventional automatics (with rapid response and similar smoothness), it is too bulky and heavy to fit in any but the largest of vehicles. Its driveability and electronics-enabled precision off-road control are extremely impressive, but how could IVT compete if it is the size of a bus transmission? When Dick Elsy arrived fresh from Jaguar (and that company’s installation of the latest 6ATs), he realised that Torotrak’s existing development IVT would need to be downsized to fit in a Jaguar transmission tunnel if it were ever to have the chance of competing. So he set about encouraging the company’s engineers to explore ways to downsize the IVT without compromising its unique smoothness and great torque handling capacity. From that point, the company’s engineers came up with a range of improvements.
How does it work?
The output of the variator is then carried by a chain to an engine-driven epicyclic gearset. Essentially, the epicyclic gearset acts like a difference engine; its output speed will be the difference in rotation speed between the variator and the engine-driven shaft. Depending on the relative speeds of these two, the effect at the road wheels can either be a positive (forward) or a negative (reverse) effective ratio. If the speeds are the same, the difference between them is zero, and the therefore the effective ratio is zero – in other words, the transmission’s output to the wheels is zero, even though the engine is still connected directly to the wheels. This is called a ‘geared neutral’, and the beauty of this is that it enables the elimination of a starting device such as a clutch or torque converter. As a result, the driveline is simpler and more fuel efficient – and it avoids the durability issues inherent in starting devices. At a cruise, when higher effective ratios are called for, an internal, ‘high regime’ clutch disconnects the epicyclic gearset so that the variator output drives the road wheels directly. At low speeds, the low regime clutch re-connects the epicyclic gearset to bring the IVT’s unique forward-through-neutral-to-reverse controllability into play. |
A new compact variator control system
The first priority has been to simplify the control and arrangement of the variator rollers. In the Series III development unit, the control arms that carry the rollers point out of the variator at different angles, making it bulky and complicated to assemble. Elsy’s drive for a more compact transmission has led to a simpler modular method for effective ratio control that offers minimal projections outside of the variator footprint. Elsy points out that the engineers had already had the idea for a more compact control mechanism before his arrival, but that they just hadn’t had the chance to develop it.
The new compact variator assembly uses an arrangement of levers to carry each roller, all of which have been engineered to be actuated by just one source of hydraulic pressure. This has greatly simplified the hydraulics requirements.
Reduced size and low manufacturing costs
To address the size reduction, the engineers have taken a multi-pronged approach in addition to minimising the profile of the roller control module. The variator discs have been reduced to 90mm diameter, 25% down from the Series III development unit’s 120mm, also cutting their weight and moment of inertia for improved ‘kick-down’ response. The engineers have also taken the opportunity to thin down the output discs to 10mm, which enables the entire variator assembly to be just 220mm long.
In fact, the new Compact IVT design is much smaller and lighter than the current Series III development unit. Torotrak says that it will be no larger than the smallest in-line rear wheel-drive 6AT (the Aisin AW unit, which is used in the Lexus 430LS, Porsche Cayenne and others). In addition to this, engineer Les Robinson says that each component can be produced using tried-and-tested manufacturing techniques, which is calculated to bring the costs down to rival those of six-speed automatics.
Improved cooling for greater power density
Improved cooling is crucial because it helps to maintain the IVT’s power handling capacity during downsizing, particularly for the rollers in the variator. The Series III development unit in the 200kW Ford Expedition demonstrator is cooled by spraying each roller with the traction oil, but the cooling effect is limited because much of the oil simply bounces off the spinning rollers. In the new compact lever design, close-fitting shrouds around the rollers keep the oil in close contact with the roller surface, thus maximising the opportunity to absorb heat. The improved cooling has enabled the compact variator to handle 235kW in testing; whereas the design’s calculated maximum power rating was only 140kW before the use of the shrouds! “The design has the potential to handle even more power, but our test rigs are at their limit,” says Mike Hough, Project Leader of the Variator Design Unit.
New ‘fill-for-life’ traction oils
The oil used in the new IVT is a technological marvel in itself. Eighteen months ago, when Torotrak invited journalists to try out its Series III IVT development unit, there was a question mark over the transmission oil’s ability to meet fill-for-life or low temperature operation requirements.
In the IVT, unlike any other transmission, the oil is needed to behave like a component as well as a lubricant because it has to transmit torque between the input/output discs via the rollers. In the microscopically-thick oil film between the rollers and the input/output discs, the oil molecules actually align themselves to form a semi-solid layer – “like chewing gum” – to resist the incredible shear forces and thus transmit the torque from one disc to the other. Chief Tribologist Jonathan Newall says that initially it was hard to persuade the oil companies to supply small quantities of unique specification oil – nowadays they are sending in samples for testing on a regular basis.
![]() |
Dick Elsy was appointed as Torotrak’s new chief executive officer on January 1, 2003 |
The new oils meet the manufacturer’s strict durability and low temperature requirements (down to minus 30-35C, unaided): “we’ve now got the fluids that will take IVT into automotive use without compromising the traction capabilities,” explains Chief Tribologist, Jonathan Newall.
New Off Highway and Heavy Duty division
Torotrak has until recently focused the majority of its efforts on winning business in the light vehicle segments, but in early 2003 the company decided to expand its potential marketplace by setting up a new Off Highway and Heavy Duty division. Director, Rob Oliver, an ex-Massey Ferguson man who has been with Torotrak for five years, explains that the division is dedicated to winning new business in the off highway (tractors, diggers, etc) bus, heavy truck and delivery vehicle segments.
The need for a continuously variable transmission is already appreciated by the tractor manufacturers; many tractors use this in the form of the hydrostatic drive.
“The trouble is, the hydrostatic pumps and motors themselves tend to be extremely expensive and can run to 1,000s of pounds,” says Oliver, “we’ve carried out extensive cost analysis on our variator and believe that we could offer a significant cost benefit.” Oliver also explains that the maximum efficiency of the variator is around 96%, whereas hydrostatic drives manage 78% at their most efficient, so there is less need for oil cooling of the IVT because it throws out less waste heat. Oliver goes on to suggest that a developed and tested standard IVT variator unit could be dropped into off highway machines to directly replace the hydrostatic transmission. The simpler IVT unit would come at a significant cost saving; and apparently this concept is currently being examined by a number of manufacturers.
The ability to control the vehicle precisely via the transmission electronics is also of great appeal to the off highway market. Accuracy of movement is particularly attractive in planters, for instance, which need to advance 1m, pause, plant and then advance another 1m. This precise control of the vehicle is amply demonstrated in the Ford Expedition with TORC™ (see below) – where the vehicle can be instructed to move forwards by any preset amount and then stop again.
Oliver goes on to say that in addition to his division’s success in the tractor industry, IVT is also finding interest in the delivery vehicle and bus sectors. Delivery vehicles are apparently an ideal application, with their constant stop-start regime and need for ease of driveability. Bus costs could also be cut because the IVT would be able to use TORC™ control to eliminate the retarder. Oliver says that the brake-free anti roll-back function provided by TORC™ is also of interest to bus manufacturers and fleet users.
TORC™ electronic control
Torotrak has adapted the IVT’s electronics to develop its trademarked TORC™ (Total Off-Road Control) control, which enables a new range of user-specified driving characteristics. The TORC™ system is mounted in the dashboard and comprises a digital display, rotary control knob and four push buttons (Speed, Distance, Creep and Hold).
The electronic controls enable constant low-speed hill climbing and descent (and hill hold), without touching the brakes or accelerator, simply by dialing in a speed on the display.
![]() |
This rear-wheel drive version of the Compact IVT is a co-axial unit, with the epicyclic gearset mounted on the end of the variator |
The transmission adjusts its ratios and controls the engine to maintain a constant speed, even when driving over the brow of a hill. ‘Distance’ lets the user tell the vehicle how far he wants to advance before then stopping; again, without the use of brakes or accelerator. ‘Creep’ lets the user set their own preferred transmission creep speed, whilst ‘Hold’ lets the driver stop on a hill and then remain stopped, again, without the brakes or accelerator, because the transmission provides the necessary torque to prevent roll-back, without the risk of burning out a clutch or stalling a torque converter.
Elsy and Batchelor see TORC™ as a real ‘hook’, both for the showroom and for the vehicle manufacturers. In the showroom, a highly stylised TORC™ dashboard installation could provide the executive toys that help to win customers in the upper SUV segments. For the vehicle manufacturers, the relatively inexpensive electronic interface can be charged as an expensive luxury feature. Elsy points to his time overseeing the engineering of Land Rover’s Freelander, which pioneered Hill Descent Control (HDC). This highly visible in-car feature offers a controlled 5-6mph descent speed on hills, simply by using the ABS electronics and the brakes. The difference is that the IVT with TORC™ control doesn’t use the brakes; it uses the transmission-engine combination to modify the effective ratio and torque to control the vehicle. TORC™ could also be used to replace the low-range transfer box for off-roading.
Fuel economy improvement still beats 6AT
Conventional transmissions haven’t stood still whilst Torotrak’s IVT has been in development; the new 6ATs are more efficient than ever. However, whereas the Series III IVT development unit competed against 4ATs, the Compact IVT design has also improved on efficiency and ‘launch feel’. Matt Burke, Dynamics and Control Project Leader, explains that detail improvements have improved the Compact IVT’s peak mechanical efficiency by 5% over that of the Series III development unit. Thus, fuel economy on the EU96 combined drive cycle shows 9.5% improvement over a 6AT for the Compact IVT – and the company points out that there is room for further improvement in the future via powertrain optimisation initiatives. Compared to the 4AT, the Series III prototype IVT shows a 20% improvement on the US Metro-Highway cycle, which has been independently verified by a vehicle manufacturer.
Prospects
Torotrak is working with a global Tier 1 automatic transmissions manufacturer to produce physical examples of the Compact IVT for testing by the end of 2004. It will fit in the space occupied by the latest six-speed automatics and offer not only a smoother ride but also an estimated 11.5% improvement in fuel economy and CO2 emissions – and all at the same cost as the 6AT. Assuming that the new unit meets its design criteria and a go-ahead for production is received, we could see IVT-equipped production vehicles on the road by 2008.
Rising fuel prices in the US are continuing to pile the pressure on the manufacturers of SUVs and pick-ups, and a change in US leadership could see tougher fuel economy legislation. The off highway market is particularly attractive for Torotrak, where its IVT could be used to challenge the costly hydrostatic drive in tractors (members of Torotrak’s team have actually been sent on tractor appreciation courses…).
The feeling that one gets on visiting the company’s headquarters up in the North of England’s Lancashire is much more up-beat, with a real sense of energy and enthusiasm, very much in contrast to the atmosphere only 18 months ago. “The engineers can now begin to see payback for their efforts… the handover of the technology to our partners and customers themselves is quite a fulfilling experience,” says Elsy. “Our engineers are now getting quite used to travelling halfway around the world and being welcomed and embraced as equals by the transmission manufacturers and by the OEMs,” adds Batchelor.
What of Torotrak’s financial position? The IPO raised an estimated £50m in 1998, but Batchelor explains that the company has found a strong revenue source in consultancy work for its prospective customers. In the early stages, customers get pure research support and that can then progress to the prototype stage and installation into vehicles. “We don’t have to wait to get revenue from production – there is plenty of potential to work with customers along the path to licensing,” he says.
In terms of technology development licensing, there has been no change since GM and Toyota dropped out and Equos (subsidiary of Japanese automatic transmission manufacturer, Aisin AW) and ZF took up licences. However, with the efforts of the dedicated Off Highway and Heavy Duty division, it wouldn’t be surprising to find that the company’s next licensee comes from that sector.
Whilst niche markets, such as off highway and bus or delivery vehicles, are attractive to Torotrak, “of course, the high volume automotive market and shareholder satisfaction are the long-term goals,” says Elsy.
It is true that whilst the current Series III IVT development unit is very impressive, its sheer size and engineering complexity prevent it from being seen as anything more than an interesting concept. What the firm needs is a device that can be truly competitive; the new Compact IVT design addresses those issues by being no larger than the latest six-speed automatics, whilst at the same time it is more responsive and even more fuel-efficient. Oh, and at a projected manufacturing cost equivalent to that for the 6AT. “To displace existing technology, you have to be absolutely bullet-proof – if you don’t answer the critical problems you’re sunk,” Elsy sums up. With this new unit, the company can meet the 6AT head-on – and that is something worth shouting about.
|