
Managers at PSA Group’s Sevelnord light commercial vehicle plant in northern France do not sugar coat the plant’s recent history – put bluntly, in 2012 the factory dodged a bullet with award of a contract to build a new line of vans.
A booklet, prepared to introduce media attending the recent launch of the redesigned mid-size Peugeot Expert and Citroen Jumpy/Dispatch model lines to their factory, states quite clearly: “We must not forget that Sevelnord was struggling in 2012, and serious questions were being asked about its future. Now the award of the K0 project [Expert/Jumpy/Dispatch] and the arrival of a new partner [Toyota, for whom the plant builds Proace derivatives of the PSA vans] are evidence of the group’s determination to maintain a strong manufacturing base in Europe and particularly in France.”
The plant is part of a northern France automotive cluster. Sevelnord itself is now in PSA’s own North Region Manufacturing Division, which also includes Francaise de Mecanique (Douvrin powertrain) and PSA’s Valenciennes (gearbox) sites, while partner Toyota, under its own steam, also builds the Yaris in the region, all supported by adjacent supplier final assembly/sequencing factories.
That, an insider told just-auto, is handy when it comes to personnel. There are now a lot of good, well trained auto assembly workers in the region and considerable workforce flexibility. Last year, PSA added an extra shift at Sevelnord for six weeks just as Toyota temporarily reduced staffing so many of those workers hired on at PSA. When PSA’s extra shift ended, back to Toyota went the workers.
“Having four big assembly plants in the region gives you advantages. The workers have skills and are agile and flexible,” I was told. Same with the local suppliers: “They can supply all of us or at least two or three of the plants.”
Recognising there are common issues, the regional automakers also have their own association/lobby group known as ARIA.
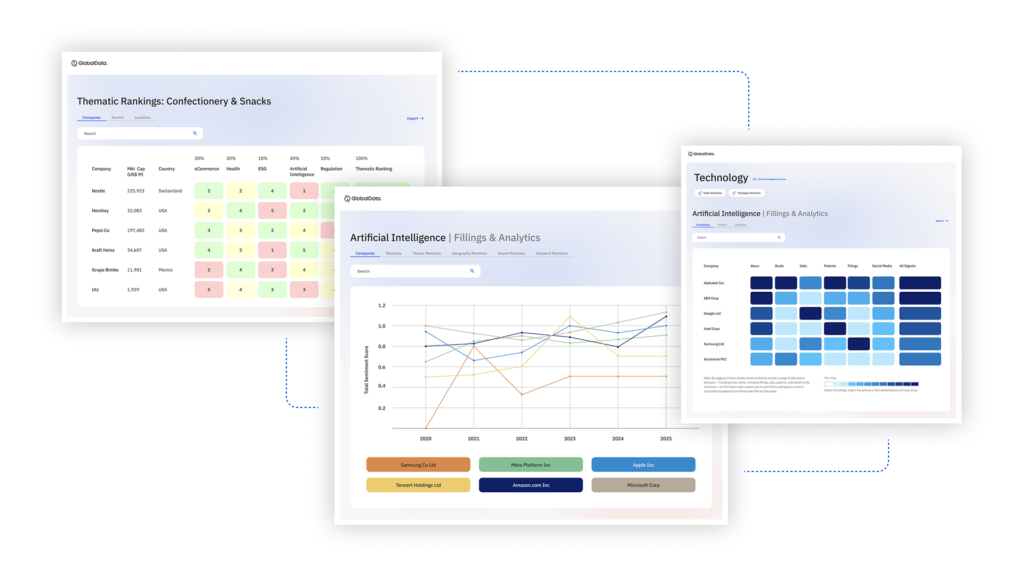
US Tariffs are shifting - will you react or anticipate?
Don’t let policy changes catch you off guard. Stay proactive with real-time data and expert analysis.
By GlobalDataSevelnord dates back to 1993 when it began building first generation MPVs [minivans] – Citroen Evasion, Fiat Ulysse, Lancia Zeta and Peugeot 806 for a now ending JV with the Fiat Group. Dark clouds formed in 2011 when PSA and Fiat said the Sevelnord JV agreement would not be renewed beyond 2017. Production of the final generation of shared medium vans – some with Fiat badges – was winding down when I visited.
The horizon began to brighten in July 2012 when PSA and Toyota announced they would cooperate on LCVs for Europe with the Proace van replacing the long-nose Hiace Toyota Europe previously assembled for itself in Portugal. A few days later, PSA announced a company-wide competitiveness agreement between itself and three trade unions which altered working conditions with the focus on job mobility and skills development, organisational flexibility, wage restraint and youth employment.
On 1 January, 2013 Sevelnord became a wholly owned PSA Peugeot Citroen subsidiary and the K0 project was assigned to the plant. The first Proace was delivered to Toyota later in the year. Francaise de Mecanique (Douvrin), Sevelnord (Hordain) and PSA Valenciennes were brought under the new Regional Manufacturing Division on 1 January 2015 and on 1 January this year employees became Peugeot Citroen Automobiles (PCA) staff.
The award of the K0 project spurred a ’30 months to transform Sevelnord’ project which included, among other things, a new IT system to streamline the supply chain, ‘plug and play’ assembly tools and about 150,000 hours of training costing EUR150m – what one insider called a ‘frugal’ solution. The aim was to ‘right size’ the plant to improve performance and also improve synergies with the nearby Regional Manufacturing Division plants such as Valenciennes where gearboxes are made and Douvrin (engines). A broad based training and skill enhancement plan was also put in place to ensure staff knew how to use the new technical innovations to best advantage.
It didn’t stop there. Now a new, two-year site project – ‘Tomorrow Starts Today’ – is under way intended to make the plant competitive enough to become “the undisputed European leader for LCV production”. The project is expected to achieve a 30% reduction in the plant’s manufacturing costs as a proportion of total vehicle production costs.
Sevelnord is, in many ways, like BMW’s Leipzig plant in eastern Germany. It does not press panels nor make engines and gearboxes; they come from other dedicated company factories near and far. The factory instead does what it says on its tin: assemble. There are three main buildings – body in white, paint and final assembly.
Body-in-white
For anyone who thinks knocking up a line of vans is simpler than building cars – let him come to Sevelnord. All those options – long, short, medium wheelbase, one (left or right) or two side loading doors, barn doors, glazed or no, or tailgate, glazed or not. With or without wiper/washer holes. And so it goes, the permutations are endless and door choice often dictates roof pressing, too. Body in white has three brand-new lines – one for doors, flaps and bonnets, one for the chassis and one for side panels. Only two were retooled for K0 – the frame line, where the various sub-assemblies come together to make the vehicle body and the final assembly line where the opening modules are fitted. Particularly impressive was the roof fit station where sucker-cup robots choose the correct roof from multiple stacks of panels, hoick it up to the correct body and other robots weld it on. About EUR90m of that EUR150m spend went into the body shop.
PSA has a policy of making group plants more compact with fewer, smaller production lines to adapt to volumes, logistics concentrated at the centre of the facility and suppliers integrated into the plant. This has been achieved at Sevelnord with Yazaki (wiring looms) and Plastic Omnium (fuel tank systems) operating in the BIW plant to final assemble and line sequence parts for the vans.
Value is also extracted from unused areas, if possible, through rental or sale and both Gefco and Altya use space at Sevelnord.
Paint
The KD kit plant party trick of standing visitors in a hand-spray paint booth close to workers painting cars to demonstrate the efficiency of the down-draught to water bath catchment spray droplet extraction system are long gone – these days it’s probably easier to enter a nuclear plant than get a visitor into a hermetically sealed, dust-free, auto factory paint shop. Despite a willingness to special suit and boot, admission to PSA’s Sevelnord paint shop was not forthcoming. Not even a view from The Other Side through glass. So I could not see the new generation surface treatment process with low environment impact, new robots to stretch the sealing strips or fully robotised paint application on which EUR10m was spent. I did, however, see the impressive end result on newly coated bodies arriving by conveyor at the start of the trim line – Sevelnord offers an impressive range of metallic shades as well as the expected ‘commercial’ white, red and blue (and any other colour you like for a big enough fleet order).
Assembly/logistics
Everyone I met at Sevelnord was particularly proud of the way they have “revolutionised” the way parts are conveyed from reception bay to the operator who installs them. Kitting processes have been developed on a wide scale to increase quality, flexibility to marketing needs and logistical efficiency. Operators are now given all the parts they need to assemble a vehicle together in a ‘kit’ that travels line-side with the vehicle. This essentially does away with line-side stocks. The number of handling operations for parts containers has been halved and the IT systems that control the overall supply chain have been replaced. Sevelnord was the first European site, in November 2014, to adopt the Corail programme which transforms the way the supply chain and its IT systems work. It manages and monitors the flow of 3,600 units at the plant a day and is focused on cutting transport costs, stocks and the space needed for storage while improving relationships with suppliers to give them greater visibility.
All this cost about EUR40m. Among new features: a bumper conveyor system, mechanical assembly areas, a dashboard assembly area and computer-guided trays that distribute parts automatically. Many other systems were adapted to accommodate the resized K0 and to operate with the new platform on which the van line is built. “Sevelnord now sets the operating standard for assembly and logistics”, is the claim.
This is not surprising as the new vans themselves are so complex. Most of the driving aids, safety items and infotainment/connectivity now available for cars are also offered on the new Citroen, Peugeot and Toyota van models and many are optional so it’s much like the Mini plant in England – hardly any two vehicles following each other down the line are the same so getting the right standard or optional parts to the right operator to install on the right van is critical – hence the emphasis on the logistics.
People
None of this is much good without properly trained workers. Of 2,400 employees at Sevelnord, 82% are production operators, 14% administrative staff, technicians and supervisors and 4% manage. A programme over three years delivered 154,000 hours of training. The factory also works with other companies and public authorities in the Hauts-de-France region to share information on professions, job offers and training needs to build ’employment pathways between companies’ – hence that earlier mentioned to-and-fro with Toyota.