What are Advanced Planning Systems
(APS)?
Automotive suppliers are always in a state of flux. OEMs change their
requirements as expected sales are lost or exceeded. Suppliers fail to deliver. Machines
break down or the right skills are not available to do the job. However, most automotive
suppliers continue to base their plans on systems that are bad at absorbing and reflecting
all this information. While most Manufacturing Resource Planning (MRP II) and Enterprise
Resource Planning (ERP) systems have Material Requirements Planning (MRP), Master
Production Schedule (MPS) and Customer Requirement Plan (CRP), executives need more
advanced systems to control the supply chain. Automotive suppliers need to assess how they
can become more responsive to the real world.
Do you need APS?
A quick evaluation of a company’s planning and scheduling performance can be made
using these five points:
- regularly meet quoted delivery dates
- manufacturing lead times shorter than
competitors - production meetings focus on corrective
action for future schedule problems identified by the system - constraining/bottleneck work centers are
highly visible and controlled - schedule simulations are easily performed
for ‘what-if’ analysis of plans and schedules, including ‘when will it ship’
(Source R.Michael Donovan & Co
Inc)
Advanced Planning Systems (APS) are an
umbrella under which sit a variety of approaches to planning. These approaches have one
significant theme. They plan on a multidimensional basis instead of the traditional
batch-based planning structures that run in sequence. APS is a decision support system
that allows manipulation of the data and viewing of possible changes without disrupting
the operations.
What does APS do?
APS gives companies the ability to
plan all aspects of their supply chains.This covers the:
- transportation of products
- forecasting of product demand, sales and
stocking - stocking of finished goods for sales to
customers - scheduling of finished goods production
- scheduling of the materials and resources in
the production facility - scheduling of vendors to supply the plant or
warehouses with materials
In other words, APS does MPS, MRP and the
finite capacity planning process simultaneously and rapidly. It also avoids the
compromises made in each step of the traditional planning hierarchy. In a conventional
situation, each person is unaware of the implications of his or her decisions. For
example, a material plan may generate a projected workload that exceeds capacity and
overtime. If additional capacity cannot be found, it is necessary to rerun the MPS with
the new plan. In most organizations this will not happen. Therefore production, materials
and sales will not fully understand the implications of this new scenario. APS rapidly
addresses all conflicts in one computer based planning session. This highlights two of the
most significant advances of APS in an organization; instantaneous simulation of various
plans and smarter algorithms.
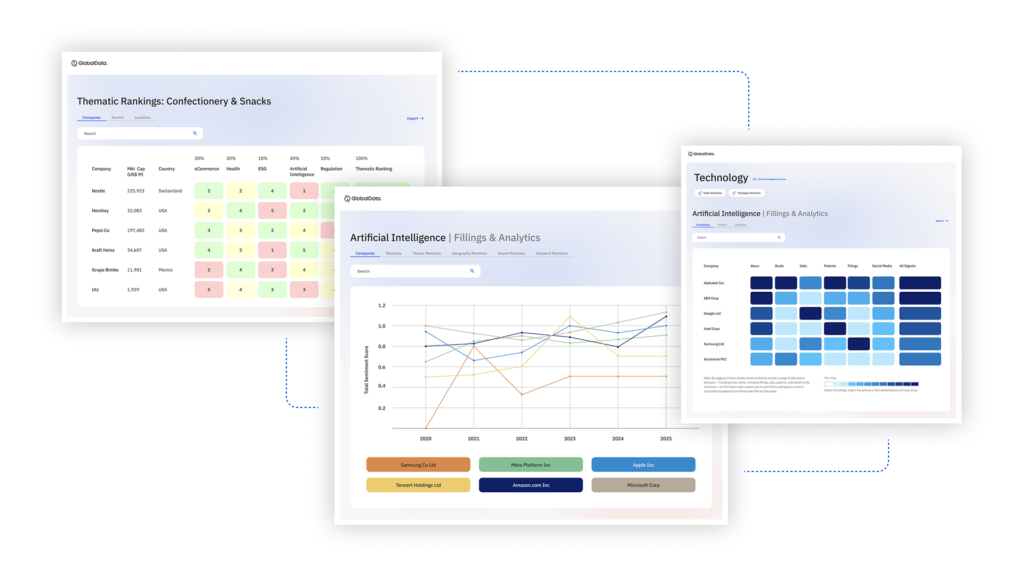
US Tariffs are shifting - will you react or anticipate?
Don’t let policy changes catch you off guard. Stay proactive with real-time data and expert analysis.
By GlobalDataWhy is APS available now?
Real time decision support is possible because these systems create plans and
schedules in a fraction of the time that an ERP system takes. ERP systems use batch-based
planning structures, which need to be run in sequence. Each step in the sequence requires
manual intervention to review, correct and pass the plan to the next sequence. For large
companies with complex products, MPS and MRP runs can be measured in tens of hours. This
means that it is often not possible for a medium to large size automotive suppliers’ ERP
installation to complete a planning cycle more than once per week. In today’s competitive
environment, it is critical to have more flexibility than this. OEM’s are transmitting
requirements daily. To run MPS/MRP weekly negates the schedule cascade required by the
supply chain.
APS, on the other hand, can complete many
scenarios and plans in a few seconds or minutes. The reason for this is that APS does the
planning in computer memory, which is dramatically faster than accessing data on disk
drives. It also completes all steps using imbedded logic rather than waiting for the next
sequence to be performed. Due to today’s powerful computers, this approach has become more
practical. Also, computing costs have shrunk over the years making this technology
affordable to most companies. (Note: the smaller the company the greater the benefits of
an APS system are because of the constraints of manpower).
Why use APS?
APS is a decision support system that allows
manipulation of data and viewing of possible changes. This can impact business activities
such as:
Schedule adherence promising
Real time analysis and response are the goals of most organizations.However, they are
very difficult to achieve because most manufacturing organizations have conflicts and
workflow constraints. Most companies run an MPS or MRP to determine whether they have the
capacity to add the new workload and if they have enough material.
In the automotive environment, it is
necessary to keep material to JIT levels. Therefore, it is not always possible to suddenly
add demand and expect that the material will be available. With scheduled forecasts, it is
possible to look ahead and plan for the material to be delivered to the plan. Again, this
is done on a JIT basis. This provides a schedule to the suppliers in the same way as the
OEM’s provide it. However, OEM’s suffer from the problems of forecasting as daily ship
requirements are often out of synchronization with the forecast. This increases the need
to run very quick and accurate plans with the alternative options available.
Planning to meet accepted criteria
This is the age of consolidation in the Automotive Industry due to acquisitions and
mergers. Therefore, many manufacturing organizations are spread over numerous sites and
countries. Multiple plants that manufacture the same product are more common. In a single
plant organization, there are still many methods to manufacture a product. The advantage
of APS is that it can quickly plan to least cost, highest revenue and best customer
service level. This gives the organization the optimal plan of utilizing the resources
that it has available.
Ramp-ups
Ensuring that OEM’s are supported during the critical ramp-up period for a new model
introduction is a problematic issue for automotive suppliers. Most ERP systems will plan
to the due date of the requirements. If finite scheduling is available, the system will go
one step further and allow users to see and plan for bottlenecks and problems in meeting
commitments. APS takes the plan to the next level. Throughout the chain, it identifies
where problems occur and suggests the best approach to eliminate the problem.
Internal metrics
Just as important as customer service are the costs of an organization. Automotive
companies are expected to reduce costs year after year. Therefore, it is just as important
that the plans that meet customer service levels are also in line with the business
objectives.
Optimizing inventory levels
Minimizing inventory levels has its penalties. Therefore, optimizing inventory so
that it meets the customer goals, but does not increase the inventory value of the company
is very important.
Policy fine tuning
Financial performance of the company is paramount. By keeping track of the financial
situation, executives can see early warning of potential problems. Various statistics show
the impact of this type of information on a company (see Figure 1).
APS can also support ‘management by
exception’. While many ERP users are bombarded by more action messages than they can ever
act upon, APS is designed to highlight the most urgent problems. Allowing each user to
prioritize their activities and fix pressing problems are key features to improving
performance.
Benefit Improvement |
Potential |
Delivery performance | 10 – 25 percent |
WIP reduction | 20 – 25 percent |
Set up time reduction | Up to 50 percent |
Make time reduction | 15- 25 percent |
Machine and labor utilization | 15 – 25 percent |
Reduction in idleness | 15 – 20 percent |
Maintenance crew utilization | 10 -15 percent |
Fig.1 The impact of information on
an automotive company
Source: Automotive Manufacturing and Production, May 1998
Supply chain management implications
Another concept that APS supports is supply chain management. The supply chain
encompasses all activities associated with the flow and transformation of goods from the
raw materials stage through to the OEM. It also helps control the associated information
flow. Materials and information flow up and down the supply chain. Supply chain management
is the integration of these activities through improved supply chain relationships. In
turn, this helps to achieve a sustainable competitive advantage.
For example, an automotive company supplier
network includes the firms that provide items ranging from raw materials to complex
assemblies and sub assemblies. The supplier network will contain both internal and
external sources for this material. A given material may pass through multiple processes
within multiple suppliers and divisions before being assembled into a vehicle. Supply
chains are essentially a series of linked suppliers and customers. In turn, every customer
is a supplier to the next downstream organization until the finished product reaches the
end user.
Market pressures are forcing automotive
suppliers to become virtual enterprises. They need to share information and make joint
decisions to ensure a fast and profitable response to the demand chain. With supply chains
such as the Automotive Network eXchange (ANX) it is necessary to speed up the process of
sharing data so that even the deepest level of the supply chain knows of a problem,
allowing it to be relayed up the chain before impact is felt.
The next level of APS moves into the
collaborative sharing of data. This truly allows different entities to access the data
using the internet. It also allows each party to add their views on a plan before it is
used in the next level of planning. This will allow the business systems to truly support
the concepts of supply chain planning.
Fig.2 Advanced Planning Systems -parts and information flows
Conclusion
APS is the next step in ERP systems. It can provide MPS, MRP and finite capacity
planning simultaneously and rapidly; it can subtract people intervention from every step
to achieve more logical views; and it rapidly addresses all conflicts in one computer
based planning session. Also, APS can plan against business objectives and address
multiple constraints and objectives simultaneously according to relative priority. Plans
can be developed at low cost and APS ensures that the concepts of supply chain management
can be made possible within a business. These functional advantages ensure that APS will
extend the enterprise into the next century.