Still plugging away
Bosch-platinum-plug.jpg” vspace=5>There are three things a gasoline engine needs: air, fuel and spark. The spark plug ignites the air/fuel mixture, producing the combustion that powers the engine. Earlier this year, Robert Bosch celebrated a hundred years since it was awarded the patent for the first spark plug. Designed to be combined with a high-tension magneto ignition system, the spark plug solved what Carl Benz had described as the most ‘fundamental obstacle’ to early motoring. Together with improvements in production technology, the spark plug laid the foundations for the rapid increase in vehicle production over the decades that followed.
In 1902, Bosch produced about 300 spark plugs. Now the company’s plant in Bamberg, Germany alone produces about a million spark plugs every working day and world-wide production is about 350 million spark plugs per year.
Early version spark plugs, used in low-speed, low-compression petrol engines had a life of just 600 miles as compared to modern copper-nickel spark plug, which lasts up to 18,000 miles. The spark plug is a key engine system component, playing a major role in fuel economy, clean, efficient combustion and the reliable operation of engines and catalytic converters. A typical spark plug will spark up to 100 times per second or more than 20m sparks over its useful life.
Although the useful life of a spark plug has been extended, its basic function has not significantly changed since the early 1900s. What has changed, however, are the requirements for emissions and service life. In 1985, Bosch introduced a platinum tipped plug in North America, thereby creating the premium spark plug market. It featured a centre electrode made entirely of platinum that was sintered, or heat fused, into a ceramic insulator. Platinum can withstand temperatures of up to 1,600 degrees Fahrenheit and so less metal is lost during firing. Platinum is also more resistant to corrosion and pitting than traditional copper and nickel-alloy electrodes. Three years later, Bosch introduced its Platinum +4 into the aftermarket, containing four times more platinum than its predecessor and four ground electrodes. Now retailing at $6 each, Bosch guarantees its Platinum+4 plugs will last 100,000 miles.
How well do you really know your competitors?
Access the most comprehensive Company Profiles on the market, powered by GlobalData. Save hours of research. Gain competitive edge.
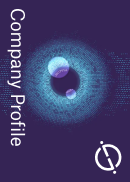
Thank you!
Your download email will arrive shortly
Not ready to buy yet? Download a free sample
We are confident about the unique quality of our Company Profiles. However, we want you to make the most beneficial decision for your business, so we offer a free sample that you can download by submitting the below form
By GlobalDataInevitably, as more new cars are fitted with longer-life platinum electrode spark plugs, the knock-on effect is a reduced replacement market. The consensus among plug manufacturers is that the European aftermarket alone is declining by 7 – 8% in volume terms each year. Another factor dampening the European spark plug aftermarket has been the popularity of diesel engines in passenger cars. Instead of spark plugs, glow plugs are used for diesel engines to pre-heat each cylinder prior to starting.. Manufacturers estimate that the European market for glow plugs is rising at 5% annually.
Wiper innovations
Debate over the issue of ‘driver distraction’ is nothing new, having first began in 1905 over the possibly hypnotic effect of windscreen wipers, and continuing in the 1930’s over the introduction of in-car radios. And now debate over the danger of mobile phone and e-mail use is emotionally charged as ever and likely to intensify as carmakers fill their vehicles with more gadgets.
Like spark plugs, wiper blades appear the same today as they did when the first windscreen wiper system operated at constant speed by electric motors appeared in 1926. However, technical advances by the major wiper manufacturers since then have centred on improving two performance characteristics: silence and wiping quality. At the forefront of these developments are Bosch and Valeo
Bosch’s Aerotwin design uses a flat-bar wiper blade that adapts to the shape of the windscreen. Traditional curved wiper blades can leave smeared or unswept areas because they don’t match the contours of the windscreen perfectly. Bosch also claims that the Aerotwin’s design improves the aerodynamics of the wiper blade, reduces wind noise, and does not impair the driver’s view of the road so much when in operation. The Aerotwin features on the Mercedes Benz CL. VW, Audi, Renault and Ford all showed cars equipped with Aerotwin wipers at the Frankfurt motor show last September.
Valeo also recently introduced a new generation of high performance wiper arm and blade for both front and rear screen applications. Valeo claims its Flat Blade delivers better screen cleaning and cuts wind noise thanks to an aerodynamic design. Valeo won an Equip Auto 2001 innovation award for its Silencio flat blade in aftermarket section. The windscreen wiper is designed to overcome noise problems associated with conventional blades. It also offers stylistic improvements over traditional designs. The new flat blade has only seven parts compared to 23 for a traditional wiper.
Clutter free instrument clusters
Siemens.jpg” vspace=5>Superficially, instruments appear much the same today as they did 30 years ago, but, like spark plugs and wipers, they have changed extensively in that time and they are likely to change even more through this decade. In advancing their driver information system, Siemens VDO engineers spent 30 months working with DaimlerChrysler developing a new instrument cluster for the new Mercedes-Benz E-Class.
Offered in four design variations, one of the novel aspects of this cluster is the floating ring speedometer needle. Instead of the speedometer needle being attached to the centre of the dial, the needle moves along the dial’s perimeter where it is attached to a revolving ring, fixed to a magnesium base. The base is gear-activated and driven by a small stepper motor.
|
Another unique aspect of this display device is the fact that it uses electro-luminescent foil instead of conventional light diodes. Claimed benefits of this white tone illumination are that the illumination is spread more evenly across the speedometer, clock and tachometer and the system adjusts to any changes in brightness, thus maintaining a uniform light intensity.
The central information display combines dot matrix and segment display technology through two display cells. The front cell has 64 light segment arranged in a circle to display information such as adaptive cruise control located within the speedometer dial. Positioned behind this cell is a second layer featuring a dot matrix display capable of conveying some 240 warning messages. All of this information may be delivered in either German, French, English, Italian, Spanish or Japanese. At the heart of the instrument cluster is a 32-bit microcontroller.
Given that Mercedes-Benz holds a high market share in the taxi industry, this instrument cluster also includes a number of taxi-related functions, eliminating the need to install other aftermarket displays in the centre console
Oil aboard
Bosch has developed a multi functional oil sensor for spark-ignition and diesel engines which provides information on the oil level and the condition of the lube-oil in use. Lube-oil wears out at different rates depending on various factors such as individual driving mode, frequency of cold starts, fuel quality or ambient temperature. Although on-board computers in modern vehicles already calculate the oil condition on the basis of these factors, Bosch claims that its sensor can determine the actual current condition of the lube-oil by measuring its viscosity, temperature and electrical parameters. Based on this data, an optimal timing for an oil change becomes more precise and reliable than previously available, says Bosch. The company plans to begin equipping vehicles with the oil condition sensor next year.
Smart seat belts adapt to the load
Autoliv recently began making a seat belt system which can adapt its restraining force—and hence the load on the occupant—to the severity of the crash and to the restraining force of the airbag. “We have equipped the retractor in our smart seat belt with a gear box,” said Autoliv’s adaptive load limiter project leader, Gunter Clute. “In a crash, our smart seat belts starts, like most modern seat belt systems, tighten the belt up to 15cm using the pyrotechnic pretensioner. This eliminates slack and makes it possible to release some webbing at a later stage, if the load on the occupant becomes too high. In a traditional system, the loads to the occupant from the seat belt and the airbag are added to each other when the bag also starts to restrain the occupant. But in our smart seat belt, the system just shifts into the second, lighter gear to maintain the restraining force at a relatively constant level.”
|
Autoliv also claims that its smart seat belt can adapt its restraining force—and hence the load of the occupant—to the crash severity. In a violent crash, the belt will remain in first gear for a split second longer before it shifts into second gear.
The gearbox itself consists of a torsion bar in which the belt is attached at one end. The bar is designed to twist when the load on the bar exceeds a pre-determined level. The bar has two sections with different diameters to produce two levels of torque. A metal tube can be moved and coupled onto the thicker or the thinner section of the bar, thereby changing the torque and the resulting restraining force.
The Swedish safety equipment maker’s smart seat belt technology already features inside the new BMW 7-Series and Mercedes E-Class.
Night-time driving, anytime
Hella has just developed its own night driving simulator, saving the German group time and money in developing new headlamps. Based on a Windows 2000 operating system, the simulator boasts a number of features. The driver and vehicle positions, vehicle orientation and position and direction of the headlamps are calculated 25 times per second while ‘driving’. The expected luminance of all objects visible in the simulated landscape is also determined based on this data. The effect of the input variables (acceleration/deceleration, steering angle, etc) is calculated directly into the driving condition and the lighting situation. It can even simulate Hella’s Varilis intelligent light systems (‘bending’ light around corners).