During the Brexit referendum, then under Theresa May’s premiership, and also during the early days of Boris Johnson’s tenure, the UK was either “promised” frictionless trade or led to be believe imports, especially, would face no specific additional burdens. Any additional friction would be as a result of the EU, implying that it would be exports which would be hit. Indeed, much of the discussion in last year’s ‘no-deal’ planning suggests that there would be both zero tariffs on most imports and only light touch import procedures, with ‘easements’ for deferring VAT payments for example.
The lack of expansion of border infrastructure on the inbound side at Dover, and the failure to recruit customs officials, or train customs agents, gave much of UK business the feeling that even on January 1, 2021, things would be relatively simple, especially on the import side of the equation.
Some of us doubted this would be the case and now we know it won’t be. In January, the Chancellor of the Exchequer said, entirely disingenuously, that UK businesses had had four years to prepare for leaving the EU; and now, in February, the de facto deputy prime minister announced that there would be full border controls. And yes, there would be unavoidable delays to imports. The food and drink industry is, unsurprisingly, very concerned, particularly regarding perishable products. But the auto industry will be affected too, although quite how remains to be seen.
On a practical level, all industries are likely to suffer from the lack of border inspection infrastructure at Dover and elsewhere. At Dover in particular there is very little, if any, space for more inspection bays, whether for inbound or outbound trucks. Reports quote logistics specialists who suggest that a two minutes inspection and paperwork check per truck would lead to a 17-mile tailback; for outbound trucks, there is the M20, but for incoming trucks, what will happen? Time is short, but perhaps the solution is building a bridge over the channel, rather than between Scotland and Ireland, simply to hold the inbound tailback.
That last statement was made not entirely in jest; the reality is that all industries will face checks where no checks exist now and this must mean extra time, extra space, extra people, extra work and certainly extra costs for industry – which will be passed on to consumers.
For the UK’s vehicle factories which receive hundreds of truck deliveries on a just-in-time basis every day, a new modus operandi will be required. Current logistics systems have a buffer time built in to allow for cross-channel delays or problems on the M25 around London for sure, but how much more time will be needed? The truth is, no one knows.
How well do you really know your competitors?
Access the most comprehensive Company Profiles on the market, powered by GlobalData. Save hours of research. Gain competitive edge.
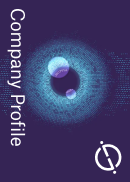
Thank you!
Your download email will arrive shortly
Not ready to buy yet? Download a free sample
We are confident about the unique quality of our Company Profiles. However, we want you to make the most beneficial decision for your business, so we offer a free sample that you can download by submitting the below form
By GlobalDataOf course, the auto industry is used to handling import paperwork, VAT payments and tariffs. All UK vehicle companies source anything from 10% to as much 40% of their components from outside the EU anyway; so, they are used to tariffs, VAT payments and associated border control issues on this part of their business. It will not necessarily be simple, and it will certainly not be cost free, but for the vehicle manufacturers, they have the basics already in place and will have to scale up; a challenge for sure, but impossible? I doubt it.
Components imported from outside the EU already require bigger buffer stocks to accommodate infrequent, batch deliveries from far afield; the same approach may have to be adopted for EU supplies. But as Honda famously warned, the potential warehouse demands this would entail would likely outweigh capacity in this area of the economy. Holding additional supplier stocks, even on consignment, will also have cash flow impacts along the supply-chain. For some supplier companies this could be beyond their cash or working capital capacity. Will the banks provide additional funding, and at what cost?
The automotive industry had to cope with a significant, albeit temporary, disruption to its finely tuned supply-chains in 2011, in the immediate aftermath of the Japanese tsunami and Thai floods; within a week of the tsunami, the supply of black paint to the world’s car factories ran out as the only factory capable of making automotive grade black pigment was located within the earthquake zone. In the UK, the Luton van plant also ground to a halt because of a lack of an electronic component supplied from a Japanese tier 3 supplier which had been flooded. Similarly, the start of production of the (then new) Honda Civic and CRV in Swindon was delayed because Honda’s Thai electronics factory was under water.
Within a few weeks, however, the auto industry had re-calibrated their supply-chains; cars could be painted black, Vauxhall Vivaros were assembled once again and Honda’s Swindon plant was busy again, albeit not forever, but that’s another story.
If vehicle production is to continue in the UK in the long run, new or heavily revised supply-chains will almost certainly need to be established.
The tsunami and floods of 2011 led to a re-evaluation in supply-chains; although this was not a complete revolution, it certainly led to greater analysis of where tier 2 and 3 suppliers were located so that vulnerabilities in supply chains could be quickly identified. Some parts were re-sourced back to Europe or to locations deemed less vulnerable to natural disasters, such as flooding or earthquakes. If vehicle production is to continue in the UK in the long run, new or heavily revised supply-chains will almost certainly need to be established.
In summary therefore, the imposition of border controls in 2021 will be a matter of great annoyance and frustration to the industry; it will add significant cost to an industry used to operating on fine margins; and yes, the UK government is now saying the reverse of what it said in the referendum, since the referendum and during last year’s election campaign. But this shouldn’t be a surprise.
If one industry can cope with such a demand for change and need to implement new systems or develop work-arounds, then the auto industry can do it – if that is, the UK factories’ overseas owners decide it is worth the effort. How much all this will cost remains to be seen. Trade economists in Switzerland looking at global trade data (pre-Brexit it should be noted) had calculated that non-tariff barriers could cost the automotive industry as much as 9%; we will soon know if it will higher or lower than this.
Brexit may yet be terminal for some, possibly most, of the UK auto manufacturing sector.
Brexit may yet be terminal for some, possibly most, of the UK auto manufacturing sector. Which factor will be the biggest impact or most damaging remains to be seen: maybe border controls, although probably not. More likely it will be the totality of the challenge of making cars profitably in the UK post-Brexit, with exchange rates, longer/more time-consuming/regularly disrupted supply-chains, the need for higher buffer stocks, tariffs on finished vehicles, regulatory issues and more. The tipping point for each car company forcing it to leave the UK will vary (it could be EVs’ investment requirements as at Honda, or loss of a crucial export market – again as at Honda). For sure, there will not be one factor alone and this will help the proponents of Brexit. They will be able to blame something else, such as EU intransigence, the coronavirus, Chinese or US protectionism/tariffs or pesky regulations.
However, it seems certain that post-Brexit, UK vehicle production will be lower – and therefore the supply-chain will be smaller – than it would have been had the UK stayed inside the single market and customs union. But that ship has sailed. As have some of the last ships with vehicles bound for export markets. Not the last one, but some of the last ships for sure.
Ian Henry is a major contributor to the GlobalData Automotive Intelligence Centre forecasting service, director of AutoAnalysis and visiting Professor of Automotive Business Strategy at the Centre for Brexit Studies at Birmingham City University.
Related Company Profiles
Autoanalysis Ltd
Birmingham City University