
Electrification of mobility is one of the cornerstones in the fight against climate change. The transition to electric vehicles (EVs) represents an unprecedented opportunity to decrease dependence on fossil fuels and reduce greenhouse gas emissions. However, the democratisation of EVs faces a significant obstacle: the price. According to market research company JATO Dynamics, the average price of an electric vehicle in Europe is around €60,000. This figure, still far from that of combustion vehicles, undoubtedly hampers the mass adoption of these vehicles.
For this reason, the automotive industry in the old continent has been immersed in its particular race, especially since the pandemic, to offer the market a 100% electric vehicle that is profitable to produce, offers good autonomy, and has a more accessible selling price. There is a certain consensus that the price point of €25,000 is considered the ‘sweet spot’ for achieving the democratization of electric mobility.
The goal seems clear. However, the arrival of this “popular” electric vehicle, manufactured in Europe, with a price of less than €25,000, does not appear to be as rapid as expected. What is causing this situation? What is holding back the industry? What are the challenges (and opportunities) that European manufacturers face in achieving this milestone?
When it comes to batteries and price, Europe has a lot of work ahead to catch up with China.
The main challenge lies in the batteries, which are the “heart” of the electric vehicle and the most expensive component. The most common battery chemistries in current electric vehicles in Europe are NMC (composed of nickel, manganese, and cobalt) and NCA (composed of nickel, cobalt, and aluminium). These are very efficient batteries, very energy-dense, but very expensive to produce. Since 2020 in China and more recently in Europe, coinciding with the release of patents and taking advantage of the reduction in the price of lithium, the so-called LFP (lithium iron phosphate) batteries have re-emerged. Their main advantage is their cost: they are cheaper to manufacture because iron and phosphate are more abundant and economical elements. Moreover, LFP batteries offer additional benefits such as lower degradation over time, meaning they can maintain a higher charge capacity after many charge and discharge cycles. Therefore, having vehicles with these LFP batteries is a key element in achieving an affordable electric car.
However, when it comes to batteries and price, Europe has a lot of work ahead to catch up with China. The Asian country has made significant advances in producing EVs at very affordable prices, partly thanks to its integrated supply chain, its ability to scale production quickly, and a robust system of national subsidies. Additionally, the battery oligopoly, including the mentioned LFP, is also theirs, as they control the entire value chain from raw material extraction to cell manufacturing, covering all associated key technologies such as mixing, calendaring, or slitting. All this allows them to have an average electric vehicle price in the country of €31,165, a figure far from the average cost in Europe. In this sense, while European manufacturers continue to focus their attention on the high-end electric vehicle segment, their Chinese counterparts are focusing on producing a variety of models in numerous segments, including more affordable ones.
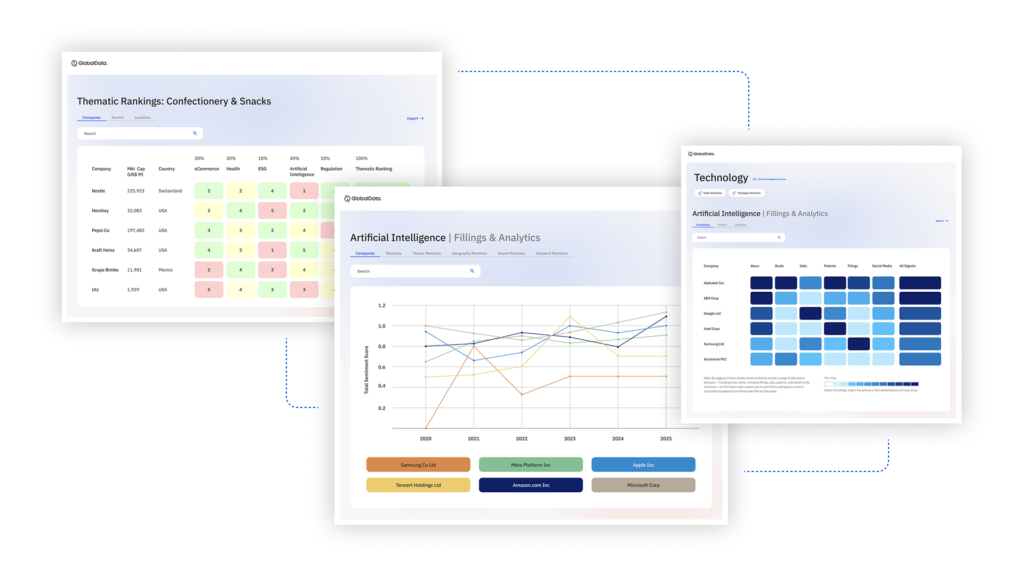
US Tariffs are shifting - will you react or anticipate?
Don’t let policy changes catch you off guard. Stay proactive with real-time data and expert analysis.
By GlobalDataWhat can Europe do in this regard? As we have recently seen and following the United States’ strategy, Brussels has decided to regulate by increasing tariffs on vehicles coming from China. Personally, I think protectionist measures will not solve the problem; in my opinion, the new paradigm requires profound transformations that go beyond, starting by defining, as China or the USA has done, a common industrial policy.
Access to raw materials and the development of key technologies for electric vehicles are major challenges that must be faced to consolidate electrification. In Europe, there is still a great dependence on foreign countries for the supply of raw materials for electric vehicles. Although it requires time and significant investments, one of the priorities should be to strengthen the internal supply of these materials in our continent and promote agreements with countries rich in these resources.
Similarly, another important factor is the creation of gigafactories where European manufacturers can produce their own battery cells; currently, most of these are imported from Asia, often bought from manufacturers who are also competitors.
Following this strategy of vertical integration of key components, many traditional manufacturers are beginning to internalise the development and manufacture of motors or inverters, among other components, with the aim of absorbing the labour surplus that electrification will create in their factories. In any case, I believe this will be a temporary and tactical action because it seems difficult to think that they can produce more optimally than specialised suppliers, who will undoubtedly be able to leverage synergies in development and economies of scale in their production with the proliferation of new platforms.
Another key technology for cost reduction is gigacasting, popularised by Tesla and increasingly adopted by European manufacturers. This process involves casting large sections of the vehicle in a single piece, reducing the number of individual components, simplifying manufacturing, and reducing assembly and material costs, contributing to a more competitive selling price. In the future, this chassis should house the battery cells playing a structural role in a solution known as CTC (Cell-to-chassis) or CTB (Cell-to-body).
Furthermore, a solid and transversal infrastructure is essential. Currently, nearly 50% of the charging points in the European Union are concentrated in just two countries: the Netherlands and Germany. It will be pointless to democratise electric mobility through price if we do not distribute these infrastructures more equitably, making them more accessible to everyone.
Another key technology for cost reduction is gigacasting, popularised by Tesla and increasingly adopted by European manufacturers.
The challenge of producing a more affordable electric vehicle is intrinsically linked to various factors that Europe must urgently address. We cannot conceive of the continent’s future as merely a consumer of imported electric vehicles; the European industry must also be a protagonist in production. Although there is still much to be done, the sector has already historically demonstrated its capacity to reinvent itself. The race towards the democratisation of electromobility has already begun, and it is everyone’s responsibility to ensure that Europe does not fall behind.