
There’s no doubt that the global automotive market is trending towards electric – with increasing consumer adoption and charging infrastructure implementation. In fact, around 1.6 million EVs were sold in the U.S. in 2023 — increasing 60% from 1 million sold in 2022. As consumers demand better mileage and cost efficiency out of their vehicles – with 77% of consumers citing saving money on fuel as the top reason they’d consider purchasing an electric vehicle – automotive manufacturers are striving to integrate the most efficient, durable and compact battery available to stay ahead of the competition. The answer to these demands isn’t in traditional lithium-ion batteries with graphite anodes, it’s in silicon-based anodes – delivering increased energy density in a smaller, more compact battery.
Battery cell and automotive OEMs (original equipment manufacturers) are increasingly looking towards implementing Gen 2 silicon-anode technology – to solve some of the historical challenges associated with silicon battery production and materials. Gen 2 silicon-anode technology enables dramatically higher energy density, while mitigating silicon expansion.
As automakers strive to dominate the electric vehicle (EV) sector, aiming to advance sustainability initiatives and overcome supply chain and production inefficiencies, below are four key benefits to adopting silicon-anode battery technology that they must consider – to not only stay ahead of the competition, but to drive a more sustainable future across the industry.
- Higher energy density (by both weight and volume): Silicon anodes enable the creation of smaller, lighter and more efficient batteries for both vehicles and consumer electronics – delivering up to 50% more energy density than traditional lithium-ion batteries with graphite anodes. While lithium-ion batteries tend to be one of the biggest contributors to overall weight in EVs – with the Ford F-150 Lightning’s battery alone weighing around 1,800 pounds, for example – silicon-anode batteries can enable much lighter battery packs for the same energy capacity, conceivably reducing the overall weight of an electric vehicle to optimize vehicle design, performance and critically, cost.
Boosting the energy density of the EV’s battery allows automakers to use fewer battery cells – leading to a more compact battery pack that contains more energy capacity. By implementing a smaller battery pack with the use of silicon-anode technology, car manufacturers can promote sustainability and minimize environmental impact – as lighter batteries (and turn, lighter vehicles) require less energy to transport, produce, and maintain throughout the product’s lifespan.
- Transformed battery range and faster charging times: With the integration of a more energy dense battery pack, electric vehicle makers can also achieve improved vehicle range and faster charging times. Nexeon’s NSP2 material supports step-change improvements in fast charging capability, taking only ~11 minutes to go from 20 to 80% state of charge.
As manufacturers compete to produce the most efficient vehicle, both range and charging times persist as a few of consumers’ primary concerns when it comes to purchasing a vehicle. Beating long-standing consumer perceptions about EVs across the industry, like “range anxiety,” begins with rethinking battery technology. As the market for EVs expands rapidly, silicon-anode batteries can deliver the competitive edge that car companies need, to capture market share and deliver a cutting-edge product.
- Remarkable cost reduction: When it comes to producing EVs, battery costs remain a paramount concern – as batteries largely contribute to production costs and typically make up around 30-40% of an EV’s value. If automakers opt to create smaller packs to fulfil the same range requirements, this can lead to a reduction in overall materials and secondary systems. In order to maximize both production costs as well as costs for end customers, implementing silicon-anode batteries is a must to maximize profit and generate returns.
- Avoiding emissions: the benefits for consumers are further compounded by benefits further upstream. Typically, graphite is used to produce anodes in the batteries that are used today; our NSP2 material is almost five times more energy dense than graphite.
As cell and material manufacturers continue to scale output to meet demand, scaling production plants that produce a much more energy dense material such as NSP2 eases the challenge by lowering the number of plants required, or rather, meeting the demand in a much more efficient way. Combined with our comparatively simple and energy efficient production process, this means that we have a strong capability to avoid carbon footprint emissions that would have been created through the production of typical graphite materials.
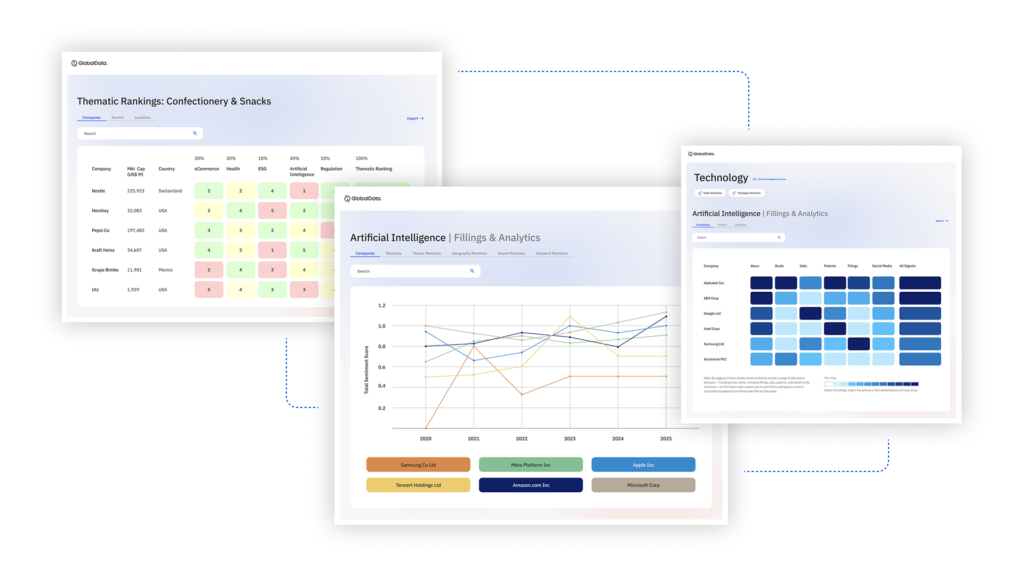
US Tariffs are shifting - will you react or anticipate?
Don’t let policy changes catch you off guard. Stay proactive with real-time data and expert analysis.
By GlobalDataAs EV adoption and market size continues to expand rapidly, vehicle companies are racing to provide consumers with EV features that can dispel their ongoing reservations about the technology – such as range anxiety, concerns about charging times, and product longevity/durability. While we continue to see breakthroughs in vehicle design and handling, revolutionising battery technology must follow suit, to deliver both better performance for consumers and generate returns for automakers. At Nexeon, we have an agreement in place with Panasonic to supply the company with silicon anode material, and we recently announced we broke ground on our first commercial production facility in South Korea – proof that this future is not far away.
To power a more sustainable future for electric vehicles, manufacturers must consider silicon-anode battery technology in the coming years – delivering the increased range, decreased charging times, and cost reduction needed to dominate this fast-growing market.
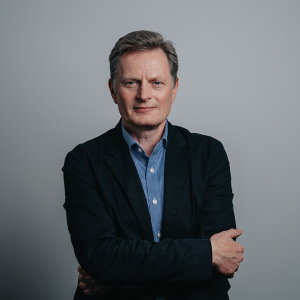
By Scott Brown, CEO of Nexeon
Scott Brown
Scott Brown has a strong track record of intellectual property management and licensing. His previous senior management roles include Cambridge Display Technology (CDT) and Dow Corning. Scott has worked in the US and Japan where he worked closely with many of Asia’s leading electronics companies. He was a key member of the executive management team during CDT’s NASDAQ IPO in December 2004 and its eventual acquisition by Sumitomo Chemical.
Scott joined Nexeon as CEO in June 2009 and since that time has led the company through a significant commercial transformation, resulting in multiple successful funding rounds and more recently, establishing Nexeon’s first commercial scale production plant in South Korea. He has a PhD in Chemistry, and an MBA with Distinction from Oxford Brookes University.