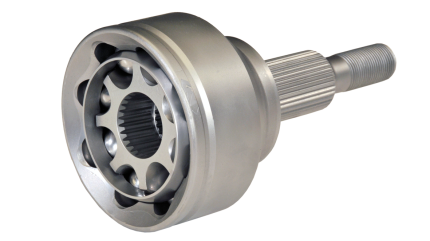
The global transition to electrification has brought a shift in the technical requirements for hardware which has previously been designed, engineered and optimised for conventional ICE vehicles. However, several fundamental differences between ICE vehicles and EVs means driveline components must withstand higher vehicle mass, greater acceleration torques, and up to 1,200Nm of braking force to enable key technologies like regenerative braking.
This requires the redefining of certain driveline components, to accommodate these fundamental differences, so that they are optimised for EVs and serve to improve the overall performance and durability of our cars.
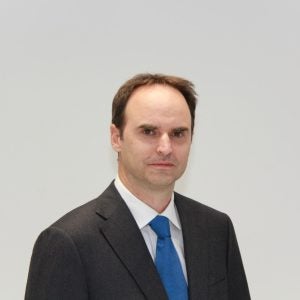
The shift from front-wheel drive (FWD) to rear-wheel drive (RWD), often favoured in EVs, along with the increased weight of the battery packs, are two of the more significant differences we’ve seen in vehicle dynamics as a result of the transition. Unlike ICE-powered vehicles, which generally carry the majority of their weight on the front axle, the mass and dimensions of an EV’s battery pack alter the load distribution. Its central location means that EVs typically have a lower centre of gravity, and are often positioned towards the rear axle.
A major challenge of this extra weight is the increased inertia of the vehicle and, therefore, higher torques in acceleration, braking and in recuperation. This necessitates a shift in how suppliers develop, test and manufacture parts for EVs.
With e-drive units being considerably larger than conventional ICE gearboxes, the sideshafts used in an EV must be significantly shorter than those in ICE vehicles, requiring different mounting points and larger installation angles. As such, we’re seeing increased plunge distances as well as updates to some basic requirements for the constant velocity (CV) joints.
Due to the increased torque demand, however, sideshafts for EVs must be stronger and more durable – despite their shorter length – while avoiding a significant increase in size, to remain as efficient and cost-effective as possible. The improved acceleration and near-instant torque availability is undoubtedly part of the appeal, but it relies on more robust sideshafts to contend with these differing dynamic characteristics, and to manage the higher torque across a wider power band.
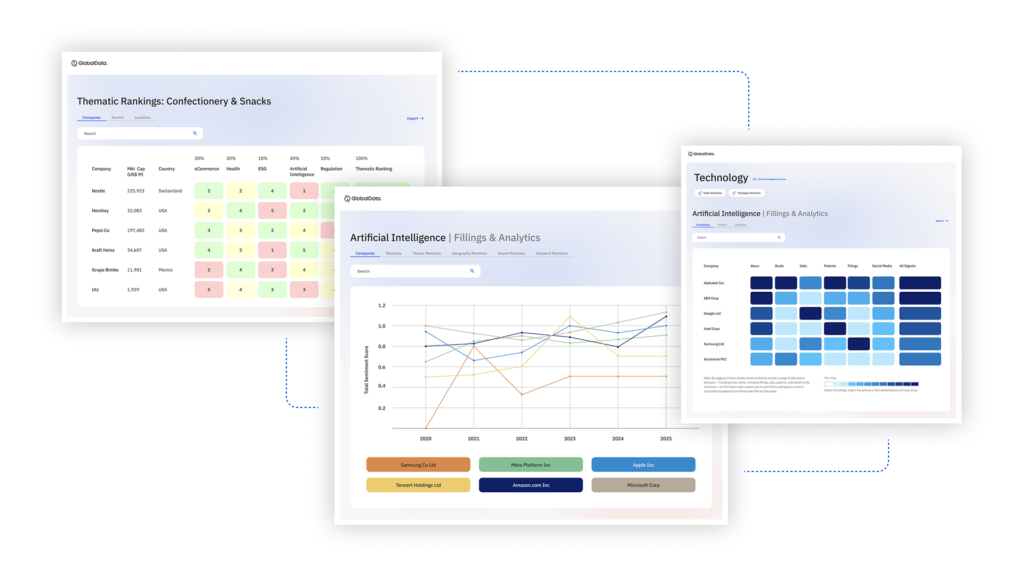
US Tariffs are shifting - will you react or anticipate?
Don’t let policy changes catch you off guard. Stay proactive with real-time data and expert analysis.
By GlobalDataIn order to navigate these fundamental changes, it’s essential that suppliers deliver solutions that are optimised specifically for EVs and their different hardware requirements. This opens up considerable opportunities for suppliers to advance technologies that fulfil the new technical requirements for EV sideshafts.
Take our Countertrack CV joints, for example – by using opposed tracks that better balance the internal forces, we are seeing efficiency improvements, alongside reduced friction and noise, vibration and harshness (NVH), to which EVs are particularly sensitive. The improved efficiency works to increase the range of the vehicle, presenting a tangible advantage in the case of battery electric vehicles.
By increasing the stiffness of an EV sideshaft, it is also possible to reduce extreme vibrations and wheel spin, providing greater torque control despite the harder acceleration. There’s great potential in this area, which is why we’ve developed a range of solutions that deliver increased stiffness for improved oscillation control.
With forecasts consistently indicating that future EVs will have a longer lifetime than today’s ICE vehicles, thanks to improvements to the efficiency of the whole system, driveline components must be durable and robust to withstand this longevity. Reducing wear and heat generation, without compromising on the set of other parameters, will help to improve the longevity and performance, which is essential for electric applications. As such, a balanced and efficient system design, with the lowest possible material consumption, is vital to manufacturing driveline components that are fit for the future.
Christian Carlando
Director of Customer Engineering in Europe, GKN Automotive