I doubt things are at the Panic Button stage but, as automakers and suppliers continue to pile into ‘low cost’ eastern Europe – this announcement of expanded output from Toyota just today is just one example – a question of labour availability and/or retention is beginning to surface.
Our business editor, Simon Warburton, at last week’s Central and Eastern Automotive Forum in Prague, heard lots of mentions of ‘labour’ and ‘shortages’. As he reported, Czech-Korean plastics supplier Plakor has been compelled to use more robots in its factories as the contracting pool of employees in eastern Europe starts to become a serious difficulty. In common with other suppliers in the region, it is coming up against myriad companies vying for a diminishing employee base. Access to staff – and crucially retaining them – has become a distinct challenge leading the supplier to offer incentives to encourage employees to stay and also offer training.
Lighting manufacturer Varroc echoed that view, cautioning the chronic labour shortage in the east will be around for a few years yet as suppliers struggle to attract enough employees to staff the booming automotive sector. The Visegrad Four: Czech Republic, Slovakia, Poland and Hungary, are the principal countries in the area, but are equally ringed with similarly low-cost bases in Slovenia, Romania, Bulgaria and Serbia, all competing for the same pool of increasingly in-demand labour. “The reality is the whole industry is in trouble,” Varroc told us. “Sometimes we decline business because we don’t have resources available – the whole industry is like this – everyone is in the same boat. How do we bring through engineers straight out of school [university] and put them to work? We have to have robust processes. It is going to be around for a few years. In the Czech Republic, they are having difficulty in getting young guys to get into technical universities.”
The subject came up again at an event in Hungary where automaker executives said improved worker mobility and local infrastructure were needed after years of emigration to western Europe created labour shortages in bordering countries Hungary, Poland and the Czech Republic, making it hard for businesses of all kinds to recruit. “There are some reasons for concern,” Audi Hungaria managing director Peter Koessler said. “If we think of human capital, we see problems in the necessary quantity as well as finding sufficiently skilled colleagues.” Hungary should focus efforts on improving housing conditions and local infrastructure to boost worker mobility and ensure a sufficient future labour supply.
Mercedes-Benz Manufacturing Hungary chief executive Christian Wolff said: “The labour situation will definitely pose a challenge for the future. We need to work hand in hand with the government and local authorities.” He said competitive wages were just a start. Daimler also had to invest in local education and provide facilities such as a kindergarten and housing for workers. You’d think hiking pay would be a good idea but Wolff was having none of it, cautioning Hungarian companies should avoid being sucked into a wage hike spiral in an effort to catch up to western pay levels quickly as that would damage Hungary’s competitiveness.
An issue to watch, I think.
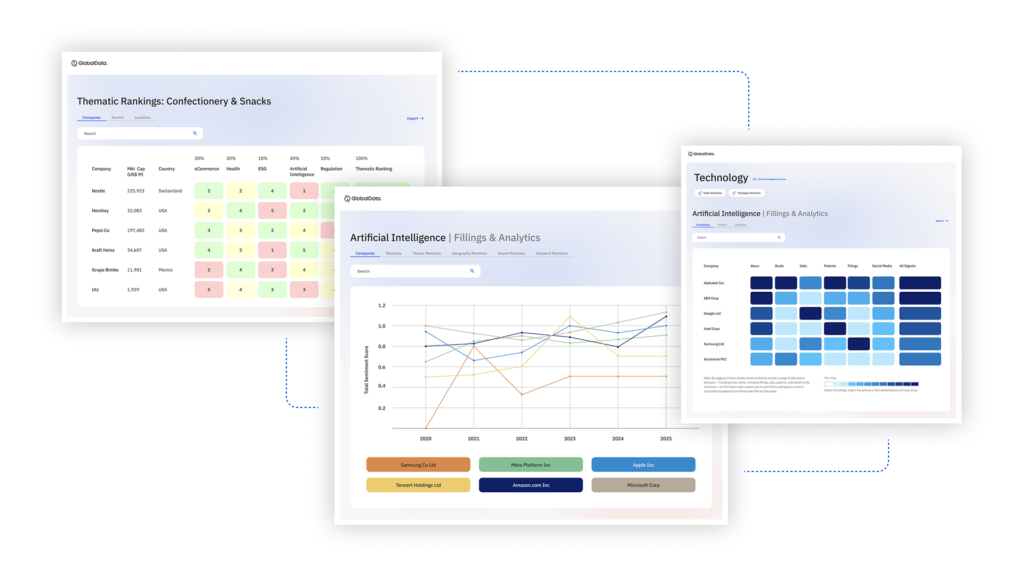
US Tariffs are shifting - will you react or anticipate?
Don’t let policy changes catch you off guard. Stay proactive with real-time data and expert analysis.
By GlobalDataHave a nice weekend.
Graeme Roberts, Deputy Editor, just-auto.com