In this latest guest article written exclusively for just-auto, Dato Madani Sahari, the CEO of Malaysia Automotive, Robotics and IoT Institute (MARii), considers the evolving electromobility ecosystem and the rising importance of the battery management system.
While discussion surrounding EV manufacturing often revolves around lightweight frames, battery, charging availability and electric motors, a key component within the electromobility ecosystem lies in the technology to manage energy storage within batteries, or the battery management system (BMS).
Generally, energy used in electric vehicles is stored in a group or series of battery cells, called battery packs. This means there isn’t a single battery cell in the car (like you would see in your mobile phone), but rather a collection of batteries that are connected together to in many clusters to store energy.
During operations of the electric vehicle as well as the charging phase of the battery, each cell would need to be monitored, balanced and managed to ensure they operate safely, and are protected to last as long as possible. Unlike mobile phone batteries that need replacement every one or more years, electric vehicle batteries need to be designed to last the lifetime of the vehicle itself – failure in which the cost of running the car becomes uneconomical for the owner.
Some reports estimate that the cost of the battery alone accounts for around 30 to 40 percent of the total vehicle cost. This poses challenges to capture the minds of the consumers, who need to overcome both range anxiety and cheaper costs of traditional cars, and particularly in Malaysia – the cheaper cost of fuel.
Commodities consumed to make batteries are also becoming a challenge. Prices of cobalt, for example increased sharply by more than triple between 2016 and 2018, only to fall back to 2016 prices. However, this volatility casts many doubts on future battery costs – making them a risk to produce without the appropriate production volume and planning.
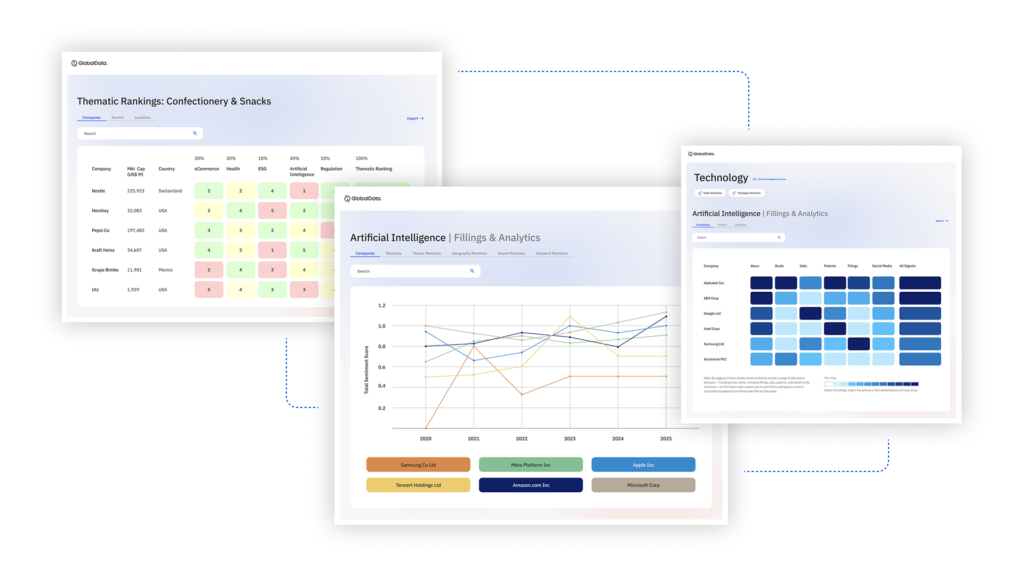
US Tariffs are shifting - will you react or anticipate?
Don’t let policy changes catch you off guard. Stay proactive with real-time data and expert analysis.
By GlobalDataConsumer sentiment on electric vehicles is slowly improving. In the case of EV batteries, a key competitive area is the mastery of battery management technology.
The BMS is one of the crucial parts in electric vehicles, that work to monitor and report the state-of-charge (SOC), state-of-health (SOH) and remaining useful life for every rechargeable multi-unit battery cell. It also monitors and manages internal and ambient temperatures, current, voltage and controlling the charging and discharging operations.
The BMS is also able to manage and adapt towards the changing of battery characteristics over time – which means it optimises the battery life based on varying conditions over the lifespan of the vehicle, i.e. the longer batteries can last without needed replacement, the more economical the cost of ownership of electric vehicles when spread over a longer period.
With more and more Malaysian SMEs participating in the IT sector, battery management technologies are new opportunities for domestic players to participate in the future auto industry.
With more and more Malaysian SMEs participating in the IT sector, battery management technologies are new opportunities for domestic players to participate in the future auto industry. Such opportunities are similar in history when the engine control unit (ECU) received attention in the 1970s and changed the way the automotive industry saw the internal combustion engine – more fuel efficient, lighter engines became a reality and made car an affordable transportation option.
The National Automotive Policy (NAP2020) stipulates the development of critical components and systems for Next Generation Vehicles (NxGVs), Mobility as a Service (MaaS) and Industry 4.0, including systems and components within AACVs, Industry 4.0 technologies, light-weight material technology as well as hybrid, electric and fuel-cell vehicles.
Battery Management Systems (BMS), Thermal Management Systems (TMS) and such technologies related to on-board energy storage are listed in Phase 1 of the policy, and will promote manufacturing and application of batteries together with the development of BMS and TMS.
MARii together with the government and the industry have begun the establishment of the Electric Vehicle Interoperability Centre (EVIC) – a shared test centre for the development of EVs and EV-related products and systems, including vehicle technology, smart grid integration, as well as energy farming, storage and management.
As more investments in EV manufacturing roll in from not only OEMs, but also components, raw materials and systems unique to electromobility, the more complete the Malaysian ecosystem will strive to become to not only assemble and sell electric vehicles, but also participate in its value chain at all levels.
The writer is the chief executive officer of Malaysia Automotive, Robotics and IoT Institute (MARii)