Whether lithium-ion, solid-state, or sodium-ion, all types of current and future battery cells will produce heat when charged or discharged. There is the potential that solid-state cells might be so thermally robust and efficient that high performance cooling may not be required, but we are still yet to see this technology enter mass production.
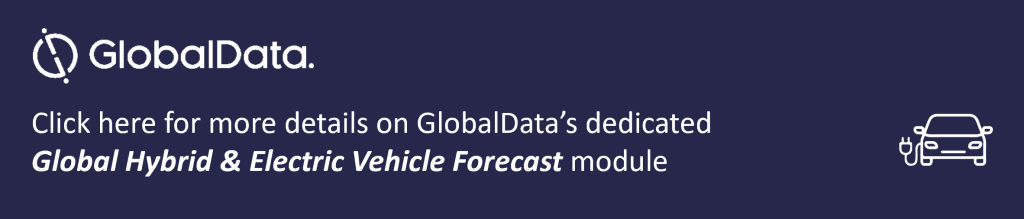
Higher charging rates will produce more heat, and keeping cells operating in the most efficient window is key for cell longevity. We have seen some battery brands highlight their achievements of reaching charging speeds of over 300kW, but the reality is that this peak power can only be attained during a very short window. When the most effective cooling systems are employed, more miles of range per hour can be gained over the course of a full charge with a lower peak charge rate.
At present, the majority of battery thermal control in Battery Electric Vehicles (BEVs) is based on a glycol coolant system, whereby coolant is circulated around the battery pack and then cooled via radiator(s). Where required, the vehicle’s climate system can usually assist in this process via a chiller. This allows the coolant to be cooled below ambient air temperature, increasing the battery cooling capability of the system.
In more premium vehicles, a heat pump is adopted, allowing the vehicle to scavenge heat from powertrain components and use it to heat the cabin, or in some scenarios, excess heat can be used to preheat the battery for faster charging.
This system requires a plethora of hardware to achieve efficient thermal control and there are several drawbacks to this approach. The heat removal capacity of cells is limited by the heat transfer between the cells and the coolant – the colder the coolant can be made, the better the heat transfer rate. But this causes a problem, namely that, dependent on the method used, there can be a large temperature delta (temperature difference) between the first cell to be cooled versus the last cell. This variation in cell temperature can cause premature cell wear on both the first and last cells. The best solution would be to heat and cool cell strings uniformly.
In order to achieve this, the cooling ‘middleman’ – the coolant itself – could be eliminated via substitution of a refrigerant plate.
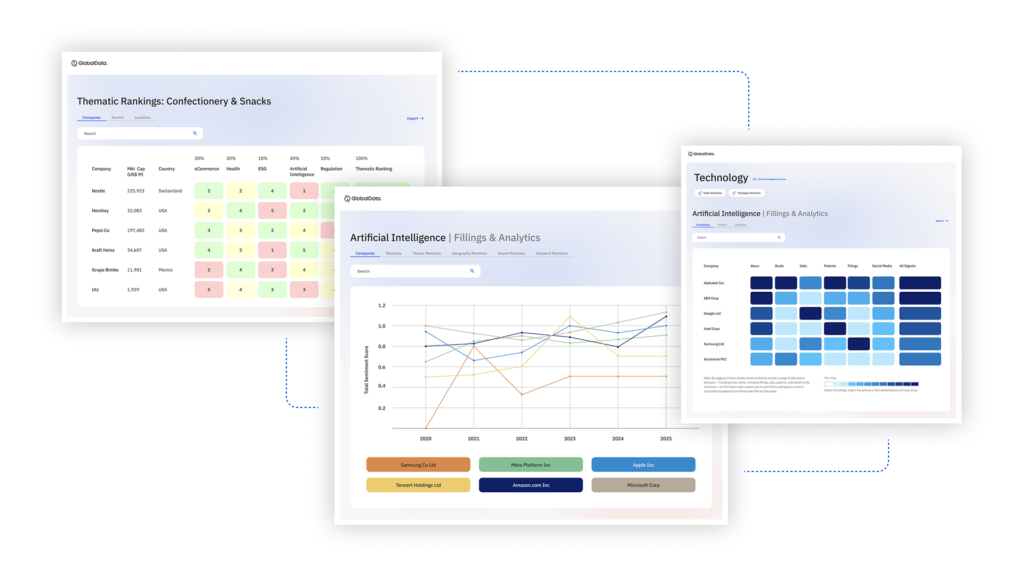
US Tariffs are shifting - will you react or anticipate?
Don’t let policy changes catch you off guard. Stay proactive with real-time data and expert analysis.
By GlobalDataThe primary issue with this method is that a giant pressurized plate would be required to cool the entire battery. Equally problematic is how well cell-to-plate contact can be achieved and whether the ambient air temperature is too low for the refrigerant system to work well enough to heat the cells. Other factors include the cell connections themselves. To achieve as much contact as possible while retaining battery rigidity and ease of assembly, a cell format designed so that the cell connections are at the sides would be needed. In the case of ultra-cold ambient temperature, issues can be mitigated with simple ribbon heaters running over the cells.
We have seen a lot of new patents filed in this area, illustrating a potential shift to this technology in the future.
One Chinese OEM has a refrigerant-based solution already in production, and as a result has achieved sustained 200kW charging for longer than most other high-charging-performance BEVs.
Direct refrigerant cooling is one of many emerging technologies that show promise in improving BEV user experience by lowering ‘refill’ times and prolonging the life of batteries.
Oliver Petschenyk, Powertrain Analyst, GlobalData
This article was first published on GlobalData’s dedicated research platform, the Automotive Intelligence Center.