
As the automotive industry evolves, so too must innovation in materials. With the electric vehicle market recording a sale volume of nearly 25 million units in 2023, and GlobalData projections pointing to a compound annual growth rate (CAGR) of 10.9% in the years leading up to 2030, a new generation of vehicles is hitting roads. And they are expected to be lighter, tougher and greener than ever.
Traditional plastics – the backbone of vehicle interiors and exteriors – are under mounting scrutiny. Regulators in Europe, China, and elsewhere are pushing manufacturers to cut reliance on fossil fuels, improve recyclability and slash emissions across the supply chain. Recycled plastics have made some headway, but sourcing consistent, high-quality plastic materials of this kind remains a headache. Desperate for solutions that tick the boxes of performance, sustainability, and cost-efficiency, OEMs are casting around for new materials to meet tightening End-of-Life Vehicle (ELV) legislation and the demands of eco-conscious consumers.
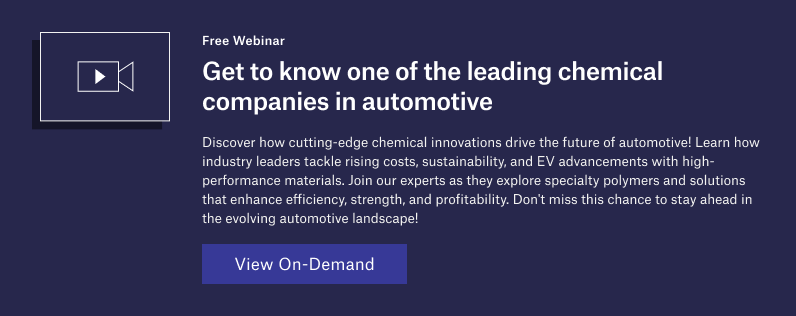
The new class of contenders
Performance, sustainability and manufacturability are the three key criteria that plastics must demonstrate in the automotive future. Combining them to the necessary standard would have seemed fanciful even a few years ago – but an increasing number of materials are hitting the market that do just this.
For example, DURABIO™, developed by Mitsubishi Chemical Group, is a technical-grade, highly transparent polymer derived mainly from plant-based isosorbide, boasting a certified bio-based carbon content of over 50%. Unlike many bio-based materials, DURABIO™ is durable and recyclable but not biodegradable. This is a vital distinction; by not disintegrating over time, it can ensure longevity while helping manufacturers meet sustainability targets thanks to its unique formulation.
The material occupies an unusual – and highly valuable – position, offering the best characteristics between conventional engineering plastics like polycarbonate (PC) and polymethyl methacrylate (PMMA). Durabio offers good impact strength and scratch resistance while delivering optical clarity and UV resistance, outshining traditional rivals. Crucially, its low photoelastic coefficient means less distortion under stress, a prized property for applications that must be both strong and aesthetically pleasing.
MCC provides a ready to use pre-colored resin, tailor made for each specific manufacturer need; they can masterbatch DURABIO™ during production, eliminating the need for costly and polluting post-mould painting. The resulting “mould-in-colour (MIC)” parts lower volatile organic compound (VOC) emissions, reduce production complexity and cut costs. Even better, OEMs do not require radical new tooling or major capital expenditure: standard moulding equipment suffices, making adoption painless.
Future-proofing with DURABIO™
As high-profile adopters such as BMW and Honda start to roll out DURABIO™ in their production lines, the industry is starting to realise its potential. The BMW i7’s distinctive piano black kidney grille surround, for example, made from DURABIO™, combines high-gloss aesthetics with the robustness to house sensitive radar and LiDAR sensors. Honda, meanwhile, has used DURABIO™ to craft windshields and bodywork for models like the X-ADV and FORZA 750 motorcycles, taking advantage of the material’s toughness and convenience in eliminating the need for traditional paint finishes.
DURABIO™ is finding its way into exterior parts where UV and weather resistance are essential. Its chemical resilience means parts can better withstand everyday assaults from everything from sunscreen to harsh cleaning agents without the need for protective coatings. OEMs also appreciate its high-gloss finish, scratch resistance and superior light transmission in internal applications.
For OEMs seeking to burnish their sustainability credentials, maximise efficiency and minimise the need for investment in new production lines, DURABIO™ is the answer. As regulations tighten and consumer expectations rise, all while margins remain razor-thin, materials that combine performance, manufacturability, and a credible sustainability story will fuel tomorrow’s automotive innovation. DURABIO™ is just one of the ways Mitsubishi Chemical Group is feeding into this innovation – and they are on hand to help manufacturers take their own leap into the future. Fill in your details on this page, or watch Mitsubishi Chemical Group’s experts unpack the topic and the latest innovations in the field, to find out more.