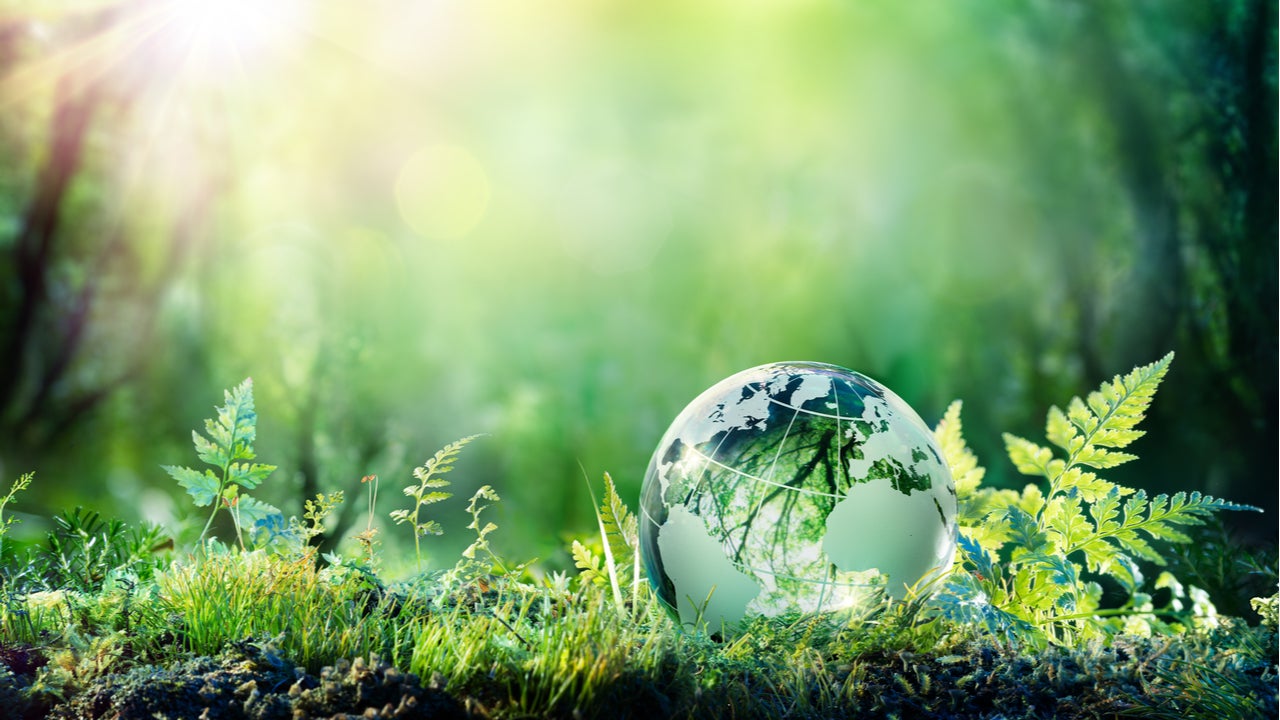
Recent years have seen a raft of new initiatives introduced across the coating and print industry that seek to move the meter towards a more sustainable future for the sector. Under the microscope are fossil feedstocks, energy usage and sustainable performance.
New regulation includes the European Green Deal, which has a zero-pollution ambition for a toxic-free environment. It is calling for a clean and circular economy – involving design, sustainable products and waste regulations such as the Packaging and Packaging Waste Directive Revision.
All of this is fostering innovation, and tailor-made bio-based products are one of the solutions.
What are bio-based materials?
The European Commission defines bio-based products as wholly or partly derived from materials of biological origin. As they are derived from renewable raw materials such as plants, bio-based products can help reduce carbon emissions and they can offer other advantages such as lower toxicity.
Biomass absorbs CO2 during its growth, so bio-based products can help to reduce the carbon footprint of inks and coatings. Bio-based products also reduce dependence on fossil fuels, are renewable and can give new or superior properties compared to standard oil-based products.
The chemistry of bio-based products
“When disposed of, oil-based products always introduce extra CO2 into the atmosphere. With bio-based materials, the CO2 has previously been removed by the plants for photosynthesis and locked into the molecule we use,” says Alexander Thrift, technical sales manager at leading global supplier of UV-curing raw materials RAHN, who has worked in the ultraviolet industry for 30 years.
RAHN’s scientists utilise these bio-based raw materials to create products used for UV curable polymers for use in various applications, including inks and coatings. Sometimes these products come from fermentation or industrial waste refining, making the process even more sustainable.
From these materials, new products are created and then produced on a commercial scale. RAHN’s newest bio-based products include GENOMER 3143, which is good for clear coatings and adhesives, GENOMER 4293, the hardest product in the range and giving advantages in 3D printed products and GENOMER 3135, which exhibits excellent flexibility and low viscosity.
So, how much bio-based material is in a product? Darren Lumber, RAHN’s technical key account manager, says: “We can calculate the percentage easily, but for our customers we need to measure it. That way, when creating a new product, we can show with confidence its bio-renewable content.”
The standard measurement accepted in the industry is ASTM D6866 or EN 16440; both methods measure how much Carbon 14 is in the product in order to calculate how much biomass there is.
For example, GENOMER 3143 and GENOMER 4293 have a bio-based content of 81% and 56%, respectively. They give impressive performance in a range of applications, offering high transparency and clarity, and low yellowing. They also have thermoplastic behaviour.
How ultraviolet light curing is more sustainable
When it comes to curing, UV light offers an environmentally friendly and efficient alternative for inks and coatings, heat sealable coatings, deep drawing, adhesives and 3D printing.
Traditional printing inks contain solvents known as volatile organic compounds (VOCs), some of which can aggravate climate change, so the industry is trying to reduce them. As traditional curing is by evaporation, involving large ovens and a lot of time and energy, it is not environmentally friendly and often the solvent directly enters the atmosphere.
In contrast, the UV curing process does not contain VOCs. UV rays initiate a chemical reaction that leads to an almost instant drying, or actually, curing of the liquid formulation into a solid state, without any need for water or solvents.
“We want to help move the industry to sustainable curing,” says Lumber. “This could be going from a conventional solvent or water-based system to UV curing or producing sustainable products and better materials.”
The benefits of UV curing
UV curing units are small and compact. Their space-saving qualities lower production costs and energy consumption. Traditional mercury vapor UV lamps, whilst already more energy-efficient have been further improved with the introduction of LED UV technology.
In fact, changing from mercury UV to LED UV can eliminate 7 tons of CO2 and give a 46% energy saving on an average printing press.
UV curing results in a lower ink deposit and higher ink mileage. As UV inks are 100% solid, you can put less ink on the substrate compared with solvent or water-based inks. The result is a smaller dot and improved dot definition, resulting in a better-quality print.
RAHN combines high-quality products, innovative expertise and comprehensive services to offer its customers tailor-made, integrated, sustainable solutions.
“UV inks and coatings can be used to protect products and increase their life.”, says Lumber, “if you’re going to produce something, you want to produce it in a low-energy way, and you want to increase sustainable performance, because by extending the life of a product, you’re automatically improving its sustainability,”.
To summarise the advantages of UV curing include:
- Higher production speeds
- No need to burn methane gas for ovens
- High and consistent quality of products
- Reduction of waste to landfill
- Lower pollution
- Conservation of natural resources
- A one-component system for easy handling
- Can be used in 3D printing, coatings, adhesives and electronics
Are you ready to take your understanding of sustainability of UV curable inks and coatings to the next level? Explore fresh perspectives and actionable insights that can drive real change in your business practices and join Rahn on February 8th at 3pm London / 10am New York for an engaging webinar that promises to illuminate the path toward a more sustainable future.