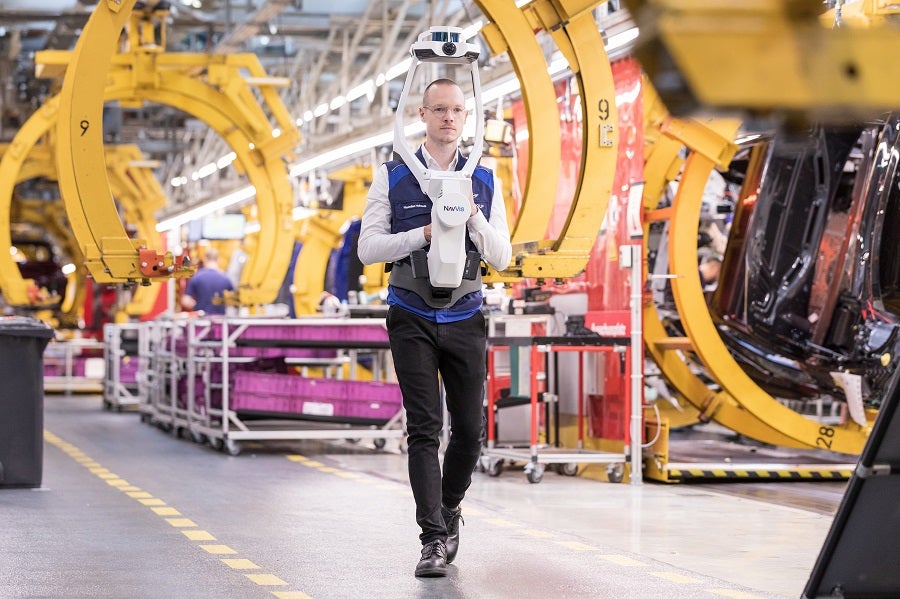
Automotive manufacturers face growing pressure to upgrade production facilities to accommodate the demand for electric vehicles (EVs) to help meet government targets for net zero. But waiting for in-person inspections to assess what needs changing within a facility can slow the process down and increase costs.
And time is not on the side of manufacturers. Many countries are banning the sale of new petrol and diesel vehicles as soon as 2030, meaning that carmakers have less than eight years to upgrade facilities to continue selling new vehicles in many markets globally.
The figures and predictions confirm the need for upgrades to happen soon. In 2021, 3.7 million battery electric vehicles were produced globally, according to figures from GlobalData. This trend will likely continue amid soaring fuel prices at the pumps. By 2031, GlobalData predicts that worldwide production will surge to 25.7 million vehicles a year, rising again to reach 38.6 million vehicles by 2036. EVs are increasingly viewed as a more stable motoring option for the long term.
Changes to manufacturing facilities for electric vehicles
While production sites must carry out upgrades to manufacture electric vehicles, the process is far more complicated than simply swapping one type of vehicle production line for another.
“The process by which you manufacture an electric vehicle is quite different than how you manufacture an internal combustion engine (ICE) powered vehicle,” explains Nate McCall, Senior Solution Manager at NavVis, leading provider of mobile mapping systems and digital factory solutions. “In the last ten to 15 years, there has been a lot happening with EVs. But in the last five years, it’s really accelerated. You see it in terms of cars coming on the market, but it’s going to take a few years for the manufacturers and supply chains to catch up.”
For manufacturers, a significant factor to resolve is the weight of EVs. Electric vehicles are on average 20%-30% heavier than their combustion engine equivalents due to the lithium-ion batteries and the more robust components required to handle this additional weight.
The extra weight of EVs can place significant pressure on conveyors when handling multiple vehicles in a production line. Over the long-term, this will inevitably slow down production, resulting in inefficiencies, rising costs, and delays in time-to-market. Consequently, one of the biggest challenges facing manufacturing facilities is reinforcing conveyors with steel to enable them to operate as efficiently under heavier loads.
Yet time spent carrying out in-person inspections before sending out engineers to perform the upgrades to facilities risks delays in production and extended periods of downtime.
Remote evaluations of automotive production plants
To keep up with the rapidly changing industry landscape, automotive manufacturers must upgrade their production facilities. And speed is of the essence.
According to GlobalData predictions, millions of electric vehicles are set to be produced in a very short space of time. By 2025, EVs built will amount to 15% of the total production of light vehicles a year. This percentage will swell to 22.5% per annum by 2028. And in the 2030s, electric vehicles are expected to become the dominant mode of automotive transport.
However, alterations to manufacturing facilities can dramatically decrease or halt vehicle production entirely. To minimize downtime, global operations managers must make sure that upgrade works are carried out as efficiently as possible. A further obstacle is relying on outdated building documentation, which can significantly increase rework costs. Any time that production is delayed results in lost revenue.
To increase planning efficiencies and avoid unnecessary travel costs, global operations managers at major automotive manufacturers are turning to technologies that enable remote inspections of production sites. Scanning technologies can generate a complete digital representation of automotive production facilities.
A digital representation enables global operations managers to remotely tour and inspect multiple manufacturing sites from one web browser without requiring the user to install any specialist software. Teams can visit locations virtually to study machinery and tools, and even view complete layouts of manufacturing sites. And with significant increases in fuel prices during 2021-22, travel is only becoming more expensive for in-person visits.
Digital representations of car manufacturing plants
Using NavVis Digital Factory Solution, for example, building managers can gain a complete 3D survey of their facilities and the precise spatial data inside at a global scale, eliminating the need for physical assessments before engineering works can begin.
To help capture and build the digital representation, rapid scanning is performed by the NavVis VLX wearable mobile mapping system. The user simply walks around the facility and lets the device scan the surroundings. The system uses vertical and horizontal light detection and ranging (LIDAR) sensors to record highly accurate spatial measurements. Four panoramic cameras at the top of the device record 360° images of the entire facility. Scanned data is available in NavVis IVION, a web-based platform that enables teams to collaborate and remotely access their facilities.
“In the scanning process, NavVis produces images similar to what you see on Google StreetView with 360° panoramic photos. You can zoom in, zoom out, and move around,” says McCall.
“You don’t just gain panoramic photos, you also gain point cloud data. They’re discrete measurements from the scanning device. That’s all captured, processed, and put into this virtual world. You get both spatial data and visual data.”
The NavVis suite of technologies enables fast and accurate decision-making. Before production begins, stakeholders can easily access vital information and quickly resolve engineering challenges. And advanced spatial data can confirm whether any works are required to remove obstructions before installation.
With a race against time for automotive manufacturers to upgrade their facilities to produce EVs, the NavVis suite of mapping and digital factory technologies provides a vital opportunity for operations managers to save invaluable time and expenditure on avoidable site visits.