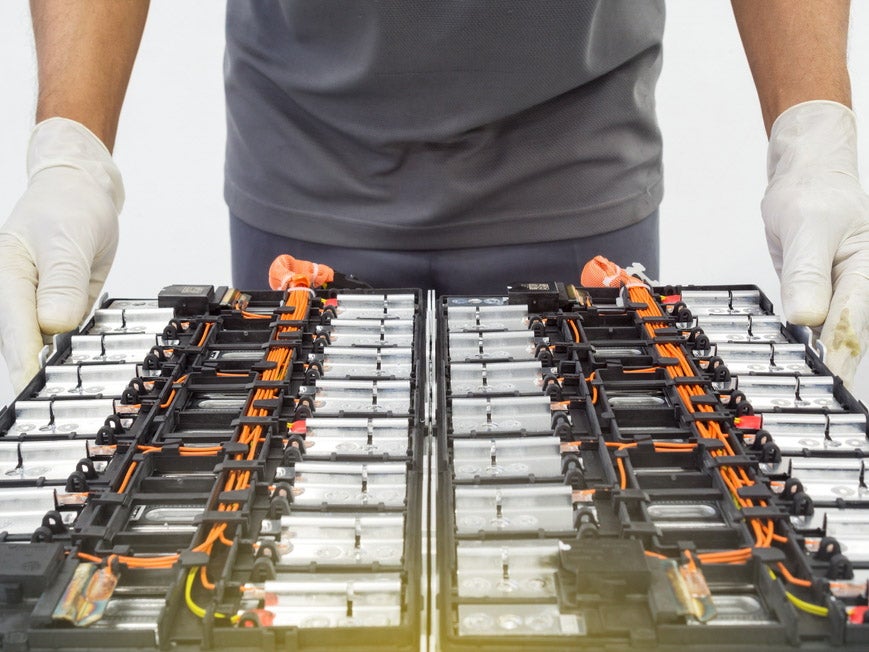
As demand for lithium-ion batteries continues to rise for electric vehicles, so too does the importance of responsible disposal, recycling and more sustainable alternatives.
According to GlobalData’s sector forecast for battery technology, the rapid growth in adopting electric and hybrid electric vehicles in recent years has propelled the global advanced nickel metal hydride (NiMH)/lithium-ion batteries market. The sector is forecast to post a CAGR of 15.3% between 2023 and 2028 to reach 54 million units.
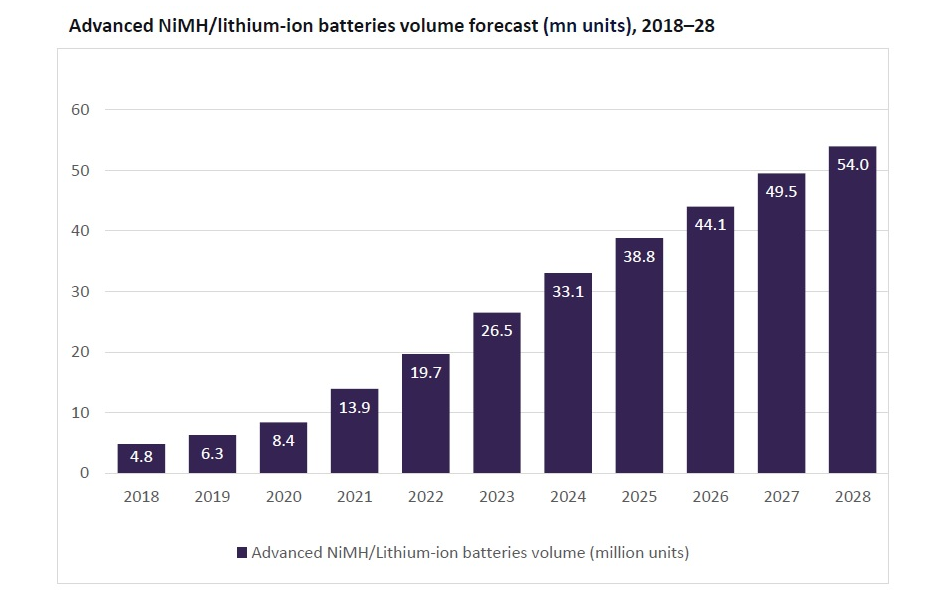
Rechargeable lithium-ion batteries are known for their high energy density and long lifecycle. The key components of a lithium-ion battery include a cathode, an anode, a separator, and an electrolyte, containing valuable and scarce resources such as lithium, cobalt, and nickel. As a result, this means that the mining and production of these resources have increased exponentially across the globe.
The emissions produced from mining lithium, cobalt, and nickel are still lower than those from fossil fuel production. However, the extraction methods for these resources can be energy-intensive, leading to air and water pollution, land degradation, and potential groundwater contamination.
The importance of lithium-ion battery recycling
As the first generation of electric vehicles ages, recycling their batteries will be essential. Expertise in this specialist area is expected to be highly sought-after.
Recycling EV batteries allows for the recovery of multiple materials, reducing the need for new mining and conserving finite resources. The recycling process involves an initial classification of the used battery to determine if it has more than 70% of its residual capacity to make it suitable for reuse as stationary storage or low-speed EVs.
The dominant process for reclaiming materials from batteries requires units to be shredded and incinerated. The end-product is called black mass, comprising residual electrolytes, as well as ash and graphite. Once the makeup of major elements has been established, those working in recycling can extract and refine valuable metals from the cathodes to produce new batteries.
However, as the compositions of batteries can vary between manufacturers and different models, the exact quantities of other elements present are not always known until after incineration. Furthermore, shredding and incineration commonly result in high levels of impurities that must be carefully managed to avoid potential damage to both the new batteries and the environment.
PerkinElmer’s Avio 550 Max fully simultaneous inductively coupled plasma optical emission spectroscopy (ICP-OES) is one instrument that battery recyclers are finding highly effective in accurately analysing the composition of black mass and the impurities present. The unit can be used alongside the SmartQuant for screening to enable users to focus on specific elements within quantitative analyses.
This information enables the reclaiming of essential metals from the black mass. After purification, new lithium-ion batteries can be produced with a fraction of the environmental impact caused by the mining and processing of virgin materials.
Are sodium-ion batteries a viable and sustainable alternative?
In the longer term, replacing lithium-ion with sodium-ion is one option being explored. Sodium is capable of reaching similar voltages and has the potential to reach a comparable energy density. Harnessing this potential could be groundbreaking for the industry, as sodium is far more abundant and cheaper than lithium.
Karlsruhe Institute of Technology (KIT) at the Research University in the Helmholtz Association has been researching overcoming the challenges with lithium-ion alternatives. Teams have been researching how to improve the health, longevity, and safety of batteries. The team at KIT also analyses ways to help batteries hold their charge for longer.
“A battery is an interplay,” explains KIT scientist Andreas Hofmann. “You can have great materials for the housing unit and electrode. But if the electrolyte is the wrong one, then it simply decomposes. Then that decomposition can catalyse another reaction. To have a good battery, we need to coordinate everything. That makes the electrolyte work more of a challenge than in previous battery development.”
PerkinElmer provides the technology and services needed to make such research possible. Hofmann and the team at KIT have been studying the electrode reactions using PerkinElmer gas chromatography (GC) instruments, including the Clarus 690, Clarus 690/SQ8 chromatography-mass spectrometry (GCMS) with headspace (HS), and an ARNEL Gas Analyzer system. These flexible systems enable the team to study both the gases and liquids, addressing many of their key research questions. Ongoing research into these techniques is essential for the future of the automotive industry.
Nevertheless, lithium-ion will likely continue to be in high demand for some time yet. For recycling existing batteries and developing new technologies, solutions from PerkinElmer will be increasingly important.
To learn more about how PerkinElmer can help overcome some of the challenges with EV batteries, download the document below.