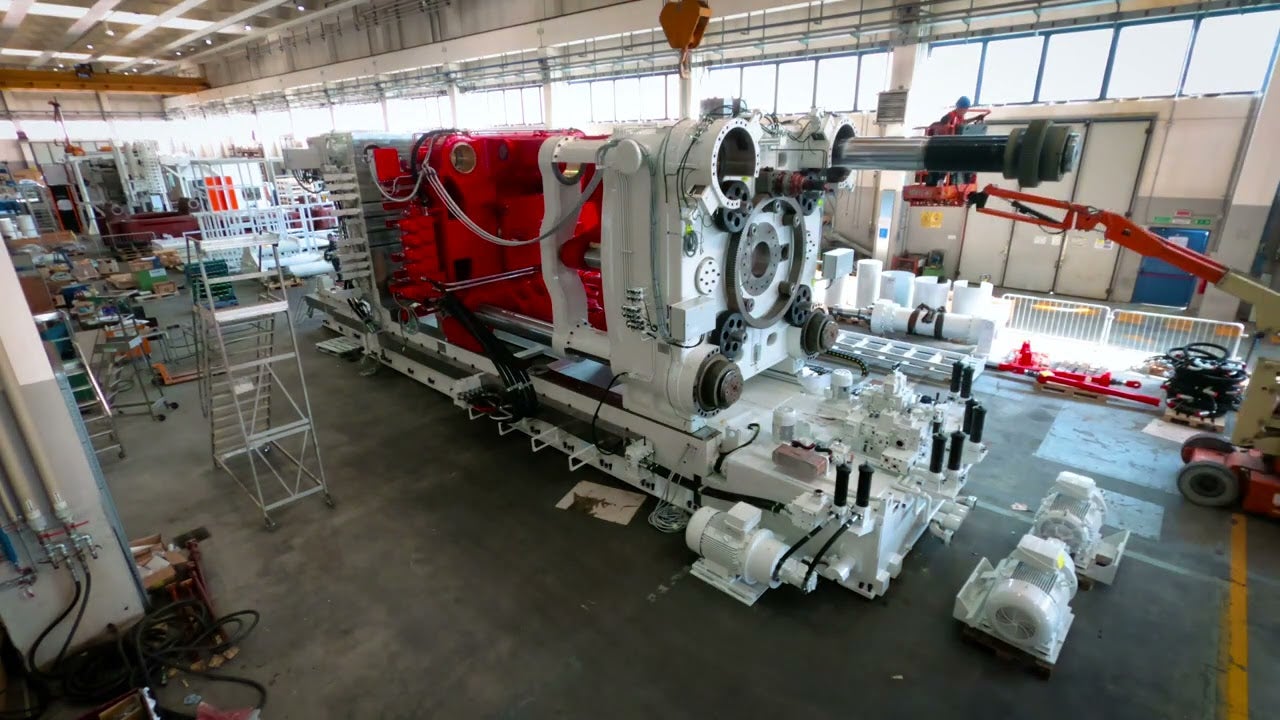
In September, Toyota unveiled a prototype of its new gigacasting equipment that can produce a third of a vehicle chassis in three minutes. The die-casting process promises to significantly cut manufacturing lead time, plant investment and production processes, bringing Toyota closer to its goal of producing 3.5 million electric vehicles (EVs) per year by 2030.
This comes as Tesla, the pioneer in these large-scale die presses, is said to be working on an innovation that would allow it to die cast the entire complex underbody of an EV in one piece, according to a recent Reuters report.
Meanwhile, mentions of casting technologies in automotive company filings appear to be on the rise, according to GlobalData’s analytics.
Other automotive companies mentioning “gigacasting” or “megacasting” in their filings include Volvo Car Corp, which announced investments of €855m ($909m) into its Torslanda plant aimed at the development of megacasting technologies last year. The company reportedly chose Swiss supplier Bühler to provide its die-casting cells for the Torslanda plant, which will be used to produce the floor structure of its EVs in 2025.
Here, Volvo in Gothenburg gets its enormous gigapress
— Nicklas 🇸🇪🚗T🐂📈🍀♻️🚀 (@NicklasNilsso14) October 8, 2023
Now Volvo Cars has started the installation of two enormous gigapresses in the Torslanda factory in Gothenburg. The giant presses came on 120 trucks and can press car parts with 8400 tons of pressure. In just two minutes, the… pic.twitter.com/rfwq9BKOCr
Hyundai and Ford have also recruited Italian Giga Press manufacturer and Tesla supplier Idra to produce its gigacasting technologies, while Japanese Toyota supplier Aisin said in early September that it would start using gigacasting to increase rigidity and decrease volume parts for its battery EV frame bodies.
How well do you really know your competitors?
Access the most comprehensive Company Profiles on the market, powered by GlobalData. Save hours of research. Gain competitive edge.
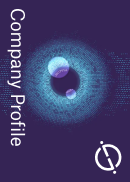
Thank you!
Your download email will arrive shortly
Not ready to buy yet? Download a free sample
We are confident about the unique quality of our Company Profiles. However, we want you to make the most beneficial decision for your business, so we offer a free sample that you can download by submitting the below form
By GlobalDataHow significant are these gigacasting developments for the automotive industry?
Shouxun Ji, Professor of Materials Engineering at Brunel University London and expert in high-pressure die casting, told Just Auto that the pivot from traditional car manufacturing approaches to integrated casting structures is “likely an unavoidable event in coming years”.
He says that gigacasting confers advantages such as improved car body stiffness, reduced manufacturing cost and reduced assembly time and cost. Rapid innovation, he says, has meant that high-pressure die-casting machines have gone from exerting a clamping force of 2,400 tonnes in 2019 to nearly 16,000 tonnes at present.
The Tesla partners linked to this technology, Idra and LK Machinery, are currently producing machines with 12,000 tonnes of clamping force, while Haitian has publicly announced the development of a 20,000-tonne die-casting machine.
However, Professor Ji notes that the thin wall structure in high-pressure die casting presents challenges for control processes as well as for manufacturing the machines themselves. Moreover, he says that “the knowledge obtained in the traditional high-pressure die casting is no longer effective and a new knowledge system will need to build up for gigacasting.”
Professor Ji notes, though, that digital twins and other simulation innovations should accelerate progress in gigacasting.
Professor Wolfram Volk, the department head for forming technology and casting at the Technical University of Munich, has also raised concerns about the complexity of aluminium die casting in contrast to cold-forming processes, with repercussions for scrap rates. In 2021, Tesla’s gigacasting scrap rate was reportedly 45%.
He also notes that die casting is not necessarily a “light-weighting” technique. “You see metal thicknesses with a lower boundary of 2-3mm in die casting, while wall thicknesses down to 0.7mm are possible with sheet-metal shells,” Volk explains. “That means giga- or megacasting cannot be classified either as an efficient or a lightweight solution – or as a higher-performing process.”
However, he says that gigacasting is a way of rethinking carb body construction, especially for EVs: “The progress that has been achieved over the years in internal combustion vehicles only has a limited applicability to electric vehicles, especially when you consider the rear-end and the middle of the vehicle. With the greenfield approach that Tesla is taking in Brandenburg, for example, the automaker can save significant space in its electric-vehicle body department.”
He adds, however, that it would be “operationally nonsensical” and not cost-effective for brownfield sites to replace long-depreciated machinery with new gigacasting technology.
Ultimately, it remains to be seen whether die casting will outpace traditional metal sheet fabrication, however, market indicators suggest a growing interest amongst EV-makers seeking to streamline production, minimise manufacturing lead times, and reach their ambitious sales targets.
Our signals coverage is powered by GlobalData’s Thematic Engine, which tags millions of data items across six alternative datasets — patents, jobs, deals, company filings, social media mentions and news — to themes, sectors and companies. These signals enhance our predictive capabilities, helping us to identify the most disruptive threats across each of the sectors we cover and the companies best placed to succeed.