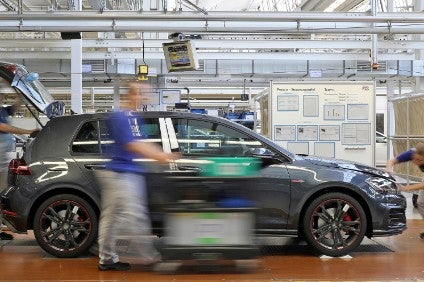
Volkswagen‘s main plant in Wolfsburg is heading for greater productivity and efficiency “with an exemplary pace of change” according to an assessment by a team of independent experts in its European competition study to make the Lean Production Award for 2018. The internationally renowned award for slim and agile production systems in the automotive industry went to Wolfsburg for the first time.
At the plant, the jury assessed equipment and technology at more than 50 stations in the press shop, body shop, paint shop, assembly and logistics as well as with respect to Industry 4.0.
VW production chief Andreas Tostmann said: “The team has genuinely earned this award. People are implementing the changes required for greater productivity and high quality with many initiatives and exemplary speed. We need this approach more than ever before to safeguard the future of the plant. Wolfsburg must be a model plant in our brand’s worldwide production system.”
“We are extremely proud to have won this award for the first time,” said Wolfsburg plant manager Stefan Loth. “This is an honour and clear recognition of our team’s performance. In addition, this accolade confirms that we are on the right track with the changes we have initiated and the pace of implementation.”
Werner Geiger, managing director of Agamus Consult and chairman of the jury, said: “No reworking and high productivity – these demanding goals are being consistently pursued at [Wolfsburg]. Improvements are implemented actively and passionately. The speed with which the team at the plant has introduced many excellent solutions over the past 24 months with a view to becoming fit through lean production is impressive. We are therefore very pleased to present the Automotive Lean Production Award 2018 in the OEM category to the Wolfsburg plant for this outstanding achievement.”
VW said that, through its PQM strategy, its main plant is focusing on productivity, quality and team performance. The objective is increasingly efficient volume production which safeguards the plant and its future. With the 400 or so workshops to be held this year alone, managers and team members are improving processes within the production system, thus reducing the production cost per vehicle at the same time as consistently maintaining the highest possible quality standards.
How well do you really know your competitors?
Access the most comprehensive Company Profiles on the market, powered by GlobalData. Save hours of research. Gain competitive edge.
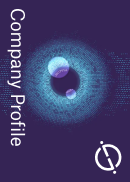
Thank you!
Your download email will arrive shortly
Not ready to buy yet? Download a free sample
We are confident about the unique quality of our Company Profiles. However, we want you to make the most beneficial decision for your business, so we offer a free sample that you can download by submitting the below form
By GlobalDataThe plant daily builds up to 3,500 Golf, Golf Sportsvan, Touran and Tiguan models.
Since series production started in December 1945, over 45m vehicles have been made there.
As agreed in the pact for the future, Volkswagen will pool production of its Golf family at Wolfsburg from the next generation. The plant will also add an additional group model, the Seat Tarraco SUV, from the end of 2018.
The international Automotive Lean Production Award has been presented by the specialist Automobil Produktion and Agamus Consult every year since 2006. This year, around 80 European plants took part in the competition and there were over 60 entries.
VW Wolfsburg representatives will receive the award for the best OEM at this year’s Automotive Lean Production Congress in Bremen in November.