Chrysler Group president and CEO Dieter Zetsche joined more than 2,000 employees at the Newark (Delaware) assembly plant on Thursday to launch the official production of the redesigned, larger 2004 Dodge Durango SUV.
“Today marks the beginning of 10 new product launches for Chrysler, Jeep and Dodge by the end of 2004 and our manufacturing operations play a critical role in the successful introduction of these vehicles,” said Zetsche.
Approximately seven inches longer, three inches taller and three inches wider than its predecessor, the 2004 Dodge Durango is a large SUV with new, stand-alone platform and new hydro-formed and fully boxed frame for added stiffness and refinement.
It has a towing capacity of 8,950 pounds and features a 15% increase in cargo volume with 102.4 cubic feet of cargo space that with third-row seat folded, is claimed to beat rival large SUVs.
The vehicle features a new trio of 3.7-5.7-litre V6 and V8 engines that deliver a claimed 10% improvement in fuel efficiency. Sales start on November 15.
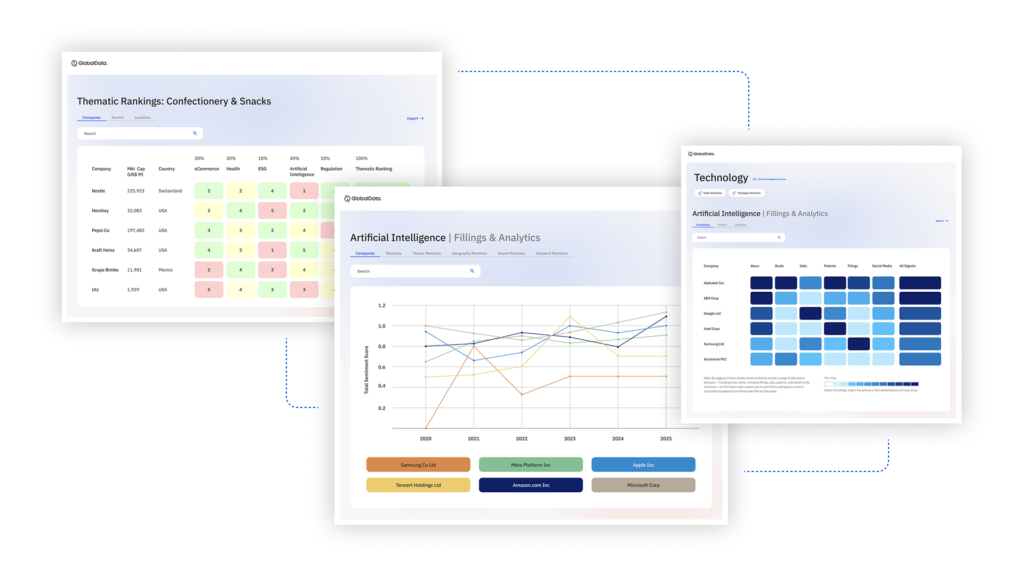
US Tariffs are shifting - will you react or anticipate?
Don’t let policy changes catch you off guard. Stay proactive with real-time data and expert analysis.
By GlobalDataChrysler Group invested approximately $US180 million to prepare Newark for production of the new model. Through flexible manufacturing strategies and reusing existing plant equipment, the company has been able to reduce initial capital expenditures by 30%.
“The new Durango will offer more vehicle options than its predecessor, and will be produced more efficiently, requiring fewer production hours per vehicle,” said Chrysler manufacturing head Tom LaSorda. “We are demonstrating through the launch of this vehicle that flexibility can be applied to an existing, and quite mature, manufacturing operation.”
The Newark facility was originally built in 1950 to assemble tanks for the military and built its first car, a Plymouth, in 1957.
From the outset, Chrysler’s engineering, procurement and supply and manufacturing organisations worked together to develop the new vehicle in a “design for manufacturing,” approach involving a comprehensive review of the previous Durango development and production processes.
“Designers and engineers were joined in a common effort – to produce a vehicle that meets the customers’ highest quality standards the first time it rolls off the line,” said Zetsche.
Plant employees were engaged early in the development process and their input prompted engineers to reconsider aspects of the vehicle’s design and assembly process. It also led to the introduction of new ergonomic approaches, thereby creating a safer work environment for employees.
This broad approach to vehicle development also involved various partners, ranging from plant tooling and equipment producers to vehicle parts suppliers. As a result, the assembly process has been streamlined, despite the addition of more options on the vehicle.
Newark Assembly also instituted an extensive quality programme that integrates over 125 quality checks throughout the production process, from the body shop to final assembly and pre-shipment to dealers. The basis for the programme was customer feedback and assembly benchmarking both within and outside the company.
The new quality verification processes enable employees at all levels to identify and resolve quality issues during production. It is expected that these actions will help lower future warranty costs.
The facility underwent a conversion to re-tool existing equipment and processes, enabling both the new Durango and its predecessor to be built simultaneously on the same production lines. The plant also minimised the amount of time required to change over plant equipment from the previous production model to the new one.
Nearly 300 robots were installed for production of the new Durango, most of them in the new body shop which was created in pre-existing, unused space at the plant. Tooling from the old shop was utilised, thus furthering cost efficiency.
Within the paint shop, two new processes and technology have been added to the line to give Durango a smooth, quiet ride in all types of road conditions: PUR foam application and Liquid Applied Sound Deadener system (LASD). PUR foam is a patented noise suppression adhesive that is injected into the body of the vehicle to minimise noise, vibration and harshness (NVH).
The second technology, LASD, is an underbody system that applies a liquid compound to the vehicle’s floor pan. This sound deadening fluid is applied in a highly precise motion by robots and helps reduce noise inside the vehicle.
Newark Assembly is one of the few automotive paint shops in the world that uses a patented “Super Solids” clear coat technology for improved scratch and mar resistance, while reducing paint emissions by 25%.