A technical collaboration with the Tokyo City University in Japan is enabling Federal-Mogul to provide vehicle manufacturers with power cylinder systems (pistons and piston rings) specifically designed to reduce CO2 emissions, the supplier said.
The powertrain technology specialist is in the fourth year of a contractual arrangement with the university, a world leader in tribology technology for internal combustion engines. Tribology is the study of the mechanisms of friction, lubrication and wear of interacting surfaces that are in relative motion. The collaborative arrangement provides Federal-Mogul’s technical centre in Plymouth, Michigan, with a trained graduate student from Japan to support its floating liner engine (FLE). This provides valuable analysis of the company’s efforts to reduce CO2 emissions and improve fuel economy.
“The FLE method allows us to evaluate engine frictional losses associated with the piston and piston ring components – a functional requirement in our pursuit to reduce CO2 emissions,” said Francis Kim, application engineering manager, and one of the original architects of the arrangement.
The collaborative programme and friction evaluation method was the foundation for proprietary technology, called EconoMiser, a comprehensive computer aided engineering and set-based test methodology allowing reduction in piston friction losses by up to 35%.
“Four consecutive years of university collaboration have contributed to a steady growth in applied knowledge,” said Steve Krause, director, automotive applications engineering, North America. “The FLE is integral to EconoMiser [but the] technology alone is not a unique approach to friction study. However, structuring the FLE tool directly within our analysis, applications and technology teams has led to innovative advances in the method, and product-specific advantages.”
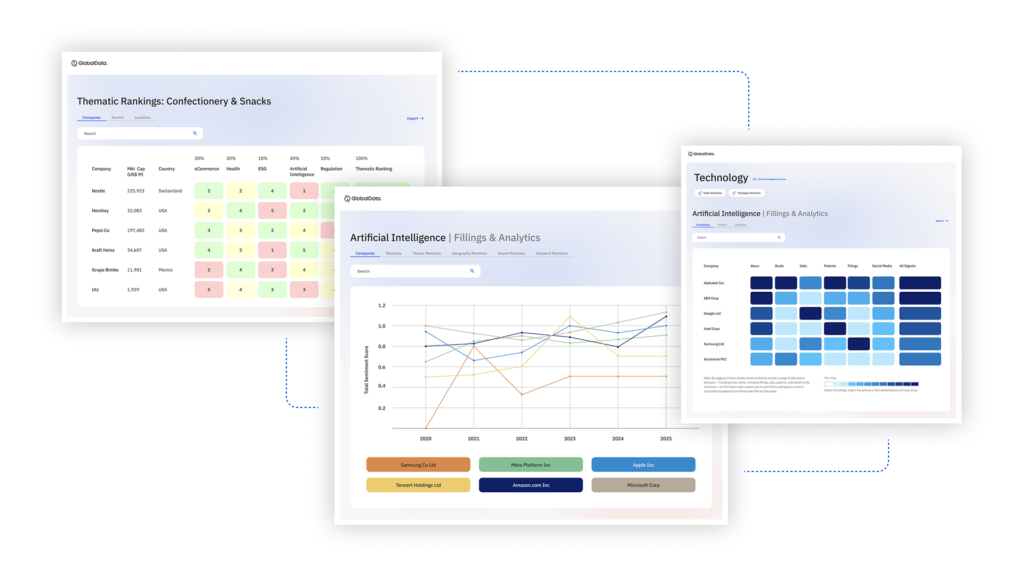
US Tariffs are shifting - will you react or anticipate?
Don’t let policy changes catch you off guard. Stay proactive with real-time data and expert analysis.
By GlobalDataTechnology improvements include optimisation of piston design for friction and fuel economy improvement applied to production pistons in 2008 model year; advanced development of piston ring design features and coatings for a 50% reduction in ringpack tangential forces resulting in improved fuel economy; and validation of in-house predictive simulation tools.
The university also benefits from the arrangement, according to Kim, through a rotational programme where one student every six months has the opportunity to work at the US center as a test engineer.