BASF says with the polyurethane foam system Elastoflex E fromit, is possible for the first time to mass-produce an exterior car part featuring a honeycomb sandwich structure with a class-A film.
The roof module in the standard model of the new smart for two consists of a paper honeycomb and two surrounding glass fibre mats.
These are sprayed in an impregnation process with the low-density, thermally activable Elastoflex E 3532 and pressed together with a solid-coloured class-A film.
A single operation produces a roof module which is around 30% lighter than the standard roof on the previous model – but retains the same strength and flexural rigidity.
The lightweight roof was developed by Fehrer Composite Components, which manufactures it in its factory in Großlangheim, Germany.
The honeycomb technology has previously been used in the car interior, for example for loading floors, roof linings, and rear shelves.
How well do you really know your competitors?
Access the most comprehensive Company Profiles on the market, powered by GlobalData. Save hours of research. Gain competitive edge.
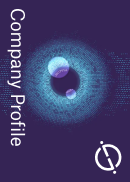
Thank you!
Your download email will arrive shortly
Not ready to buy yet? Download a free sample
We are confident about the unique quality of our Company Profiles. However, we want you to make the most beneficial decision for your business, so we offer a free sample that you can download by submitting the below form
By GlobalDataFor use in exterior components, BASF has adjusted the viscosity and reactivity of Elastoflex E (semi-rigid polyurethane system), which was developed for the honeycomb technology, so it can be optimally processed in each manufacturing step and shows good adhesion properties.
BASF says it guarantees uniform, thin wetting of the glass fibre mats and does not drip.
Once the semi-finished product has been impregnated, it is pressed into shape in a heated mould together with the class-A film.