Fuel delivery systems specialist TI Automotive has announced a revolutionary type of fuel pump especially to suit modern gasoline direct injection (GDi) engines. The latest GDi engines’ need for increasingly higher fuel pressures (5-6 bar, up from today’s 3-4 bar) and fuel flow rates poses quite a challenge for the pump, not least because the harder the fuel pump works, the shorter the life of the pump motor.
TI’s new Dual Channel Single Stage (DCSS) pump overcomes this problem by increasing the flow rate in a unique way. Conventional turbine type pumps use an impeller to drive the fuel around a single channel – whereas the new DCSS design uses a patented impeller with two sets of specially curved blades to drive the fuel around two circular parallel channels. This greatly increases the pump’s capacity (250-200 litres/hr at 4-6 bar), with little or no corresponding increase in friction, so the pump can be run at lower speeds, thereby increasing motor life.
“Present pumps only give you a maximum pressure of about 5 bar and flow rates of 180 l/hr,” said Ernst Kuhlen, TI’s director of global fuel delivery systems.
The second major benefit is that the twin channels help to overcome hot fuel handling problems in high performance GDi engines. The higher engine temperatures (necessary for improved emissions) and higher fuel flow rates increase the tendency for the fuel to vapourise in the pump, especially on hot days.
“If you have two parallel channels, one can be blocked, but the other is ok and the bubbles clear soon,” said Kuhlen. Any fuel vapour bubbles that form remain in the inner channel, whilst centrifugal force drives the liquid fuel into the outer channel, thus ensuring that some fuel always gets through in a situation that in other pumps could result in complete vapour lock.
How well do you really know your competitors?
Access the most comprehensive Company Profiles on the market, powered by GlobalData. Save hours of research. Gain competitive edge.
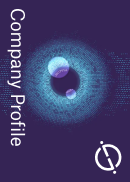
Thank you!
Your download email will arrive shortly
Not ready to buy yet? Download a free sample
We are confident about the unique quality of our Company Profiles. However, we want you to make the most beneficial decision for your business, so we offer a free sample that you can download by submitting the below form
By GlobalDataThe DCSS technology also brings nearly 50% greater efficiency (up to 30% efficiency, whereas conventional pumps can only manage about 20%) to the fuel pump, resulting in greatly improved overall fuel efficiency and driveability, said Manouchehr Kambakhsh, TI vice president, global advanced engineering.
“The DCSS pump will enable automakers to increase fuel efficiency, reduce emissions and improve the overall performance of petrol engines,” he added.
TI manufactures around nine million pumps a year (7.5 million gasoline, 1.5 million diesel) and expects that the new DCSS pump will replace the majority of its current generation fuel pumps “within six years… on a global basis.”
Larger engines will be the first to benefit and production will begin at the end of 2004 at the company’s facilities in Caro, Michigan and Neuss, Germany. First applications are expected to be in a German car from early 2005, followed by applications in existing vehicles in the US and others. The company is also working on a smaller, lower-capacity DCSS design to meet the needs of high-revving Japanese engines.
Current high performance gasoline and diesel engine fuelling needs will continue to be met by TI’s novel E5L and E3L screw pump designs. These offer a very wide, flexible, range of fuel pressure and flow rates for high-end vehicles from Bentley, Rolls Royce, Maybach, AMG and DaimlerChrysler. Extremely high flow rates (270-390l/hr) and excellent hot fuel handling characteristics are features of these special pumps.
In port (indirect) injection systems, the screw pump and DCSS pump designs supply high pressure fuel directly to the fuel injectors, eliminating the need for any other type of pump. However, for direct injection GDi systems, a high pressure mechanical pump – situated between the electric fuel pump and the injectors – charges the fuel to 170-200 bar for delivery to the injectors.
Mark Wilkinson