Key harness supplier Leoni reckons high voltage wiring for electric vehicles could be manufactured considerably more cost effectively if automakers collaborated on a standard design.
The wiring systems division's chief technology officer (CTO), Udo Hornfeck said: "The emission limits that will apply in 2030 can only be met if the electric car becomes a mass market product. It will therefore be a matter especially of significantly lowering vehicle costs. That will be the only way to create an attractive overall package. New generations of high-voltage wiring systems can make a notable contribution in this respect.
How well do you really know your competitors?
Access the most comprehensive Company Profiles on the market, powered by GlobalData. Save hours of research. Gain competitive edge.
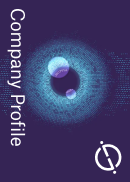
Thank you!
Your download email will arrive shortly
Not ready to buy yet? Download a free sample
We are confident about the unique quality of our Company Profiles. However, we want you to make the most beneficial decision for your business, so we offer a free sample that you can download by submitting the below form
By GlobalData"As is the case with all fresh technologies or products, there is significant potential for optimisation in the respective next generations. The key will be that we don't seek this potential by just looking at improving the individual components, but rather that we consider the overall system level – and therefore the entire scope.
"Alongside material costs, production costs constitute a major element. This is where we would like to seek the best comprehensive solution together with our customers and suppliers. Initial analysis shows high voltage wiring systems certainly do have corresponding optimisation potential through system adjustments. We can optimise our own production very well with our expertise as a systems supplier. Yet the key is to unleash all the potential along the value chain. That means it may make sense to accept higher supplier production costs if assembly costs at our customers' plants drop simultaneously."
Leoni thinks the transition from mostly manual towards highly automated production of high voltage wiring systems offers additional efficiency potential.
Plant technology has been developed further.
"The important thing is to keep an eye on the costs of production equipment and also the lifecycle costs of the product. Automation is worthwhile especially when producing large lot sizes with limited variation.
"In volatile markets, this can also be achieved by deploying standard components or standard sub-networks on several vehicle platforms simultaneously or also across several manufacturers."
Leoni is developing new components, for instance high-voltage splitters for connecting auxiliary units, with a view to a high degree of assembly automation.
"If also applying this in other areas succeeds, the variety of versions for the traction harness could be sharply reduced, thereby establishing a de-facto standard."
There are good reasons for the variety of high voltage cable harnesses presently in the market.
"Manufacturer specifications are based on many years of experience and aim to achieve maximum safeguarding. To exploit the productivity potential that can be attained with standardisation, it is essential to talk to one another about experience and to reach new forms of collaboration.
"With corresponding flexibility on all sides, we can jointly contribute to making electric cars more cost effective – without compromising safety or other product properties."