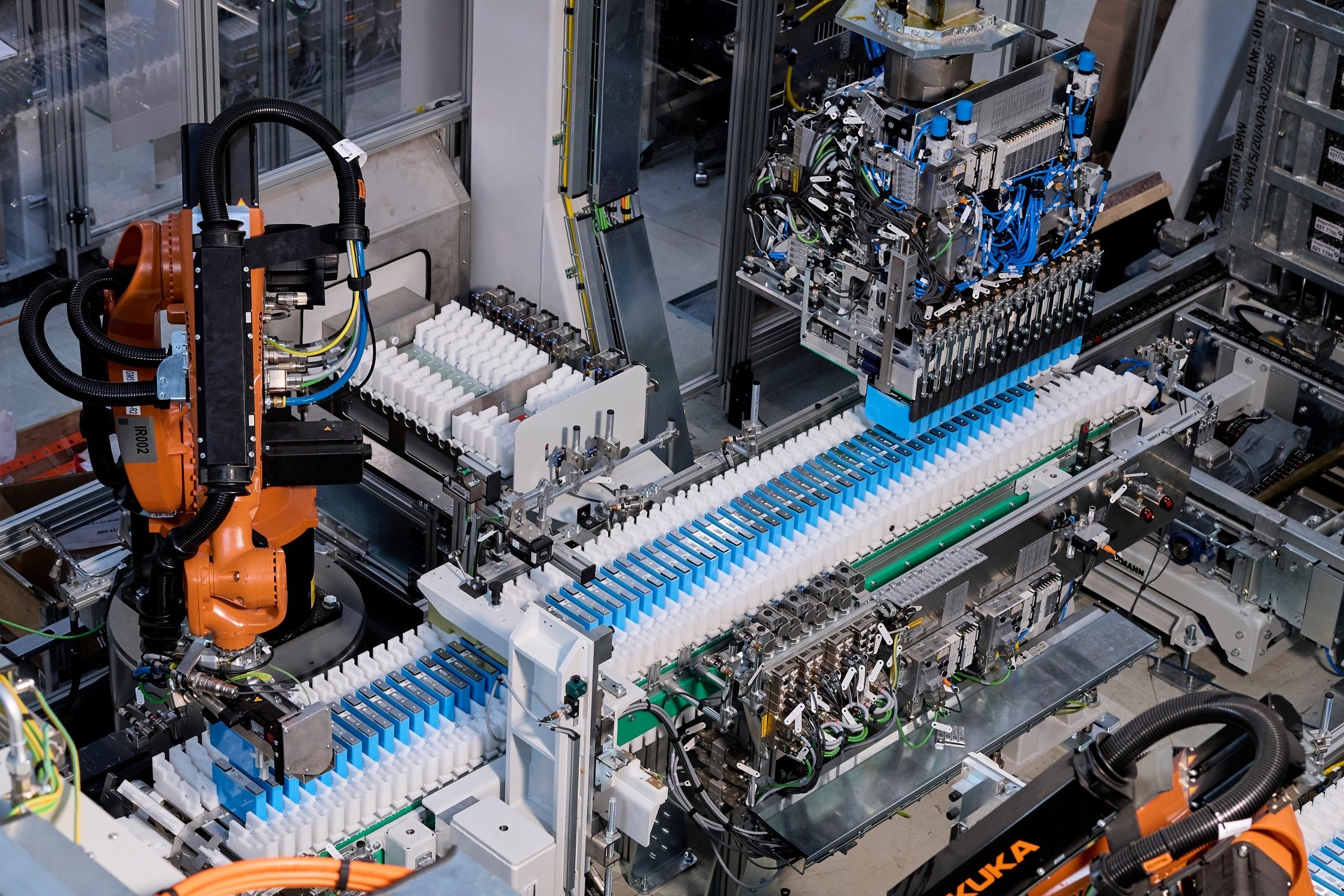
Production of fifth-generation high-voltage batteries and battery modules for use in various BMWs is now under way at the automaker’s dedicated factory in Dingolfing.
BMW is also increasing production capacity for its fifth-generation electric motor, which has been built in Dingolfing since 2020.
“We expect at least 50% of the vehicles we deliver worldwide to be electrified by 2030. To achieve this, we are relying on our extensive in-house drive train expertise. We are increasing capacity at existing production locations like Dingolfing and developing capabilities at others like recently in Regensburg and Leipzig,” said Michael Nikolaides, the group’s head of production engines and E-drives.
The group is spending EUR500m expanding capacity for e-drives at Dingolfing between 2020 and 2022. From 2022, it will produce e-drives for 0.5m electrified vehicles. The group is also spending EUR790m boosting capacity for electric powertrain components at Dingolfing, Leipzig, Regensburg and Steyr between 2020 and 2022.
Battery component output at Regensburg and Leipzig began in April and May 2021. Landshut and Steyr are stepping up production of e-drive housings.
The output and energy content of drive units and high-voltage batteries with the automaker’s fifth-generation eDrive technology can be flexibly scaled – optimally adjusted to suit different model variants.
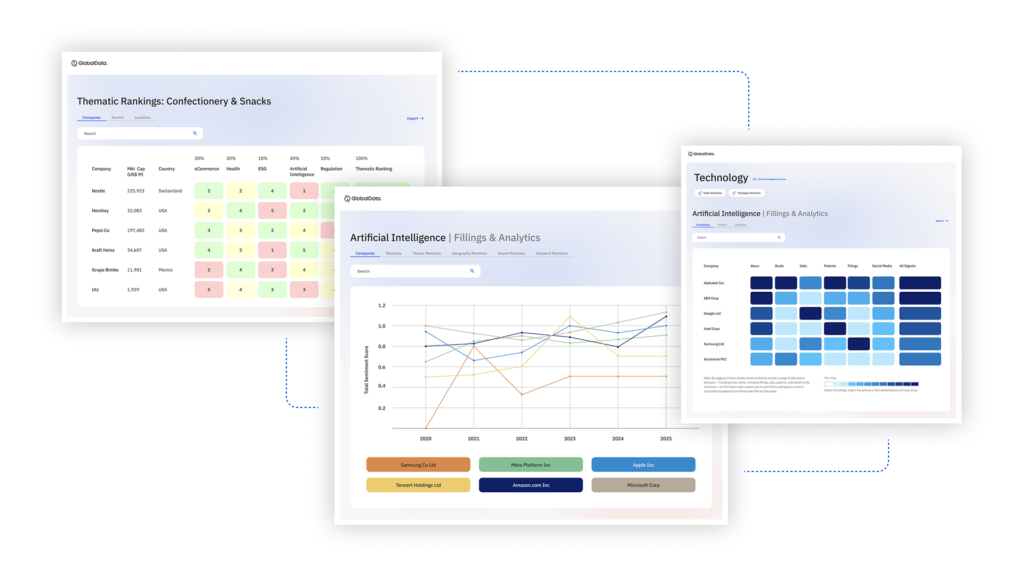
US Tariffs are shifting - will you react or anticipate?
Don’t let policy changes catch you off guard. Stay proactive with real-time data and expert analysis.
By GlobalDataEach vehicle uses up to two integrated e-drives, which combine the electric motor, power electronics and transmission in a single housing. Based on the design principle of a current-excited rotor, the fifth-generation e-drive does not require any materials classified as rare-earth metals.
The standardised production process for battery modules has been further developed so different module variants can be produced on the same line – in line. Battery modules are produced from supplied prismatic cells. A modular system developed in-house allows model-specific high-voltage batteries to be manufactured from these modules in a flexible arrangement.
Dingolfing has been manufacturing standard high-voltage batteries and battery modules since 2013 when the i3 went into production at Leipzig. The first production lines for electric motors and high-voltage batteries for plug-in hybrids went on stream in Dingolfing in 2014.
By the end of 2021, around 1,900 employees are expected to work in e-drive production in Dingolfing, up from 1,400 now.