Kobe Steel has developed galvanised steel sheet (1500 MPa class after hardening) for hot stamping.
The supplier has started mass production of the coated steel sheet for use in automotive body frame parts.
In 2017, Kobe Steel developed cold-rolled steel sheet for high-productivity hot stamping and began mass production. In comparison to conventional cold-rolled steel sheet for hot stamping, Kobe Steel maintains its material has improved hardenability.
“Productivity during pressing by the customer has improved as much as six times, compared with conventional hot stamping steel sheet,” noted a Kobe statement. “The cold-rolled steel sheet is noted for its lower occurrence of strength deficiency from uneven quenching.
“Moreover, it offers greater flexibility in pressed part shapes. As the cold-rolled steel sheet can be trimmed during the pressing process, laser cutting after pressing, which is traditionally required in the conventional process, is unnecessary.”
Kobe Steel has also developed cold-rolled steel sheet treated with a galvanised coating for hot stamping. In addition to having the same characteristics as cold-rolled steel sheet, the new galvanised steel sheet offers corrosion resistance. This makes it possible to expand use of the coated steel sheet in automotive parts.
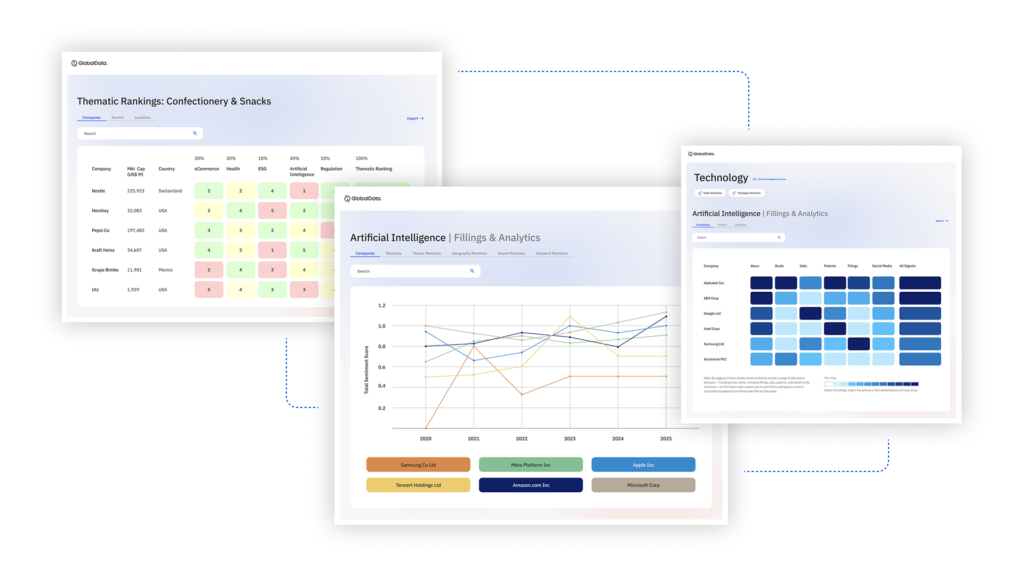
US Tariffs are shifting - will you react or anticipate?
Don’t let policy changes catch you off guard. Stay proactive with real-time data and expert analysis.
By GlobalDataNow in mass production, the coated steel sheet is supplied to Spain’s Gestamp, which processes the coated steel sheet into parts for supply to an unnamed European car manufacturer.
Adding galvanised steel sheet for high-productivity hot stamping to its product line-up, Kobe Steel also offers its ultra high-strength steel sheets with tensile strengths of 780 MPa and higher, as well as cold-rolled steel sheet for high-productivity hot stamping.