Alfa Romeo has revealed details of how the new 4C is built at Maserati’s Modena works using a mix of lightweight materials. The model weighs just 895kg, making it one of the world’s lightest cars.
Carbon fibre parts and processes
Carbon fibre was chosen for the structural function monocoque that makes up the central, load-bearing cell of the 4C’s chassis. The monocoque, which weighs just 65kg, is manufactured by Adler Plastic.
So-called ‘pre-preg’ technology, which Alfa Romeo says was inspired by Formula 1, allows production of over 1,000 pieces per year. With pre-preg, the fibres are arranged in an optimum structural direction, thus producing a result which metal would only yield if layers were overlaid, shims differentiated, and reinforcements added.
In addition, the autoclave polymerisation makes it possible to manufacture box-section structures in one phase, whereas normally the production and assembly of various components often made of different materials is required. One example would be the door post. In its standard steel version, the door pillar is comprised of approximately six pieces attached to one another and to the car body at different stages of the manufacturing process. If autoclave polymerisation is used, the door post is a one-piece component included in the load-bearing structure.
Aluminium
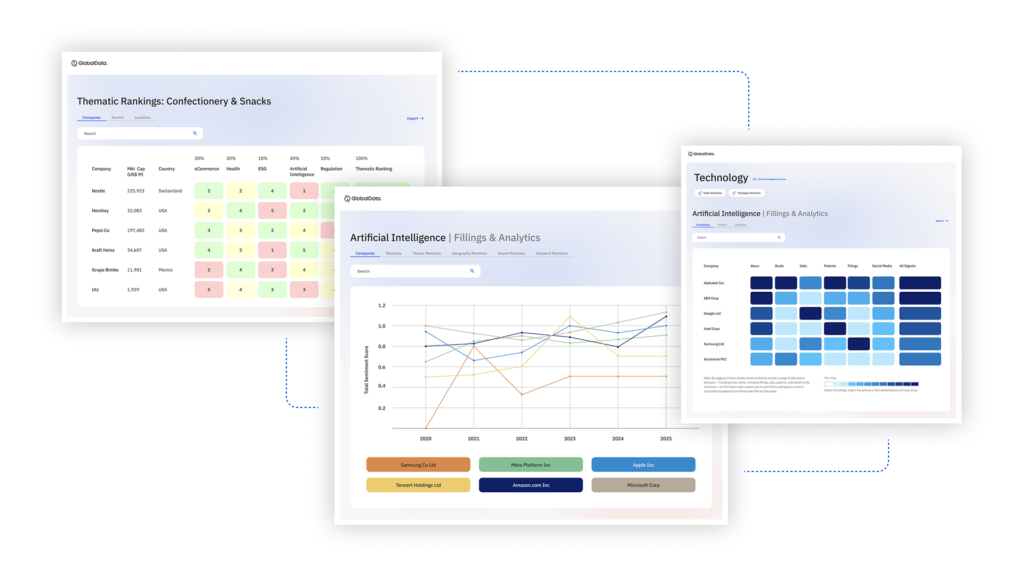
US Tariffs are shifting - will you react or anticipate?
Don’t let policy changes catch you off guard. Stay proactive with real-time data and expert analysis.
By GlobalDataAluminium is used for the roof reinforcement cage and the front and rear frameworks. Designers replaced the traditional rectangular strut section with a newly designed section. In this way, they obtained lighter and, at the same time, safer frameworks, according to Alfa Romeo. Frameworks are manufactured using the innovative ‘Cobapress’ process. Cobapress joins the advantages of fusion and the benefits of forging under press by compressing the aluminium alloy even further, thus removing any residual porosity.
Thanks to the use of seam welding processes, welding is said to be extremely precise, while the components are not deformed and the filling of the gaps is said to be excellent.
Aluminium also plays the main role in the hybrid-type front brake discs with aluminium bell and cast iron ring gear. This patented technology developed by SHW guarantees up to 2kg of weight reduction per disc in addition to better braking. Furthermore, the sophisticated surface finishing technology by brushing increases grip and pedal feel, whereas the innovative release system between disc and bell is claimed to guarantee more comfortable and safer braking. The difference in the thermal expansion coefficients of cast iron and aluminium is compensated by specific steel radial pins which accurately transmit the braking action.
SMC (Sheet Moulding Compound)
Using SMC, a low-density and high resistance composite material, for the body has allowed a 20% weight reduction in comparison with traditional sheet steel. The 4C is said to be the first standard production car to achieve such a high percentage of low-density SMC: with a weight of 1.5g/cm³ this material is decidedly lighter than steel (~7.8 g/cm³) and aluminium (~2.7 g/cm³), besides being more malleable. Moreover SMC is a stable material which, unlike aluminium, does not strain in the event of minor impacts, has high resistance to chemicals and atmospheric agents, and also disperses noise very well to the advantage of acoustic comfort.
Finally, low-density SMC guarantees a good functional integration of the parts; this in turn entails a reduction in the number of components and operations, and requires shorter assembly times, thus lowering production costs.
PUR-RIM (injected polyurethane)
PUR-RIM was chosen for bumpers and wings for the same reasons described above. It is a lightweight material (weighing 20% less than steel) suitable for creating very complex design elements, such as the 4C wing, and for keeping an ideal cost/production volume ratio.
Windows
In the case of glass, lower weight was obtained by adopting a real silhouette-thinning approach: all the windows are on average around 10% thinner than the glass normally fitted on cars; this allows for an average weight reduction of 15%. The windscreen in particular is only 4mm thick. Alfa claims this to be an extraordinary result, considering this “particularly aerodynamic shape is difficult to obtain” on such thin glass.
Manufacturing
The minimum takt time (the manufacturing speed needed to guarantee delivery) for the new 4C is 20 minutes. Maserati and Alfa claim that in most mass production plants, the shortest takt time is approximately 50 seconds.
Production takes place in dedicated 4C workshops: there are areas for body fitting and assembly operations, whereas the testing and finishing areas are shared with those for Maserati production.
The 4C primary structure is assembled in the body fitting area: here the first skins are applied to the newly created body in white. At station 10, operators fit the carbon monocoque on the front and rear chassis and on the crossmembers.
A little further down the line, on station 30, the vehicle cell is closed using the windscreen frame and the roof: this operation requires the use of special masks that ensure what the company terms “the exact passenger compartment geometry”. Finally, couplings are produced with state-of-the-art polymers and reinforced with mechanical joints.
Once the body is fitted, the 4C body in white undergoes a quality assurance check in the measuring room. Every day several sample bodies are subjected to high precision measurements. The dedicated team checks up to 400 measurement points in order to ascertain that the body is perfect from a geometric and dimensional standpoint.
The next step is painting, the only process performed outside the Maserati plant. After they have been painted, the bodies in white return to the plant.
It is claimed that the supercar is the only vehicle starting its assembly sequence with a ‘disassembly’ operation. Before the internal components can be assembled on station 1, the car is brought back to its primary structure by removing some of the parts that have already been painted, such as the bonnet and the doors, and some structural parts, such as the rear frameworks and the turret bar. At this point, the car is attached to a rotating hook.
After production, delivery
In Europe the first cars are scheduled to be delivered in the second half of September, whereas the US version will be launched in November in Los Angeles, with the first deliveries scheduled for the end of 2013.
Fiat will build an initial 1,000 units of the 4C ‘Launch Edition’: 400 for Europe, Africa and the Middle East, 500 for North America and 100 for the rest of the world. In most European markets, the Launch Edition is priced at 60,000 euro.
After this first batch of cars is produced, availability will be limited to 3,500 cars per annum, 1,000 of which will be for European markets.
Author: Glenn Brooks