As vehicle makers come under tighter CO2 emission limit rules, Johnson Controls says it sees a further opportunity to take weight out of seats. Johnson Controls says it has made lightweight construction a priority in its research and development.
"By using a wide range of technologies, we have been able to reduce the overall weight of our seats by a total of 20-30 percent over the past 10 years," said Dr. Detlef Jürss, group vice president and general manager Product Group Seating Components at Johnson Controls. "As recently as 2010, a front seat structure weighed 14 kilograms; in 2015, we were able to reduce it to around 10 kilograms. Our express goal is to reduce the weight to well under 10 kilograms by 2020, while simultaneously making the automotive seat more and more like a multifunctional element with diverse electronic adjustment options and technical features. Our designers are faced with the challenge of combining this with the need for a reduction in weight. And, of course, with ensuring that these seats also meet the highest safety and quality standards."
Johnson Controls says it already has concrete seating solutions for the lightweight construction megatrend and for emissions reduction. "Experts have come to the conclusion that automakers need to more than double the number of lightweight components by 2030 to two thirds in total if they are to comply with the EU's CO2 specifications," said Jürss. "For us as a supplier, this means that the standards for the next decade have clearly been set: The greatest expertise in processing lightweight materials will determine who will become the leading suppliers in the decades to come."
Johnson Controls says its expertise can already be seen in many of its current development projects, such as CAMISMA (Carbon-Amide-Metal-based Interior Structure using a Multi-material system Approach), Tailored Hybrid Tubes and the RECARO Sport Seat Platform (RSSP), which is ready for series production. In order to realise future seat models, the company is combining the use of lightweight materials with innovative seat concepts and proprietary manufacturing processes. Besides maintaining at least the same safety and comfort features, the aim is not only to reduce the weight of the seats, but also to produce them as cost-effectively as possible.
The focus of the multi-material approach is on increasing the amount of lightweight materials, such as fiberglass-reinforced plastic (FRP), carbon or aluminum, in the finished seat. "For example, in the CAMISMA project, subsidized by the German Federal Ministry of Education and Research, we are working on a lightweight backrest structure for use in large-scale production, for which we combine steel, FRP, carbon-fiber nonwoven material and thermoplastic tapes made of carbon filaments in a multi-layer design," said Jürss. "According to the current project status, the CAMISMA backrest is more than 40 percent lighter than conventional backrests made of metal, with equivalent performance in terms of safety. Also, carbon can be processed far more efficiently than before – reducing waste from 50 percent to less than 5 percent."
Besides using lightweight materials, Johnson Controls also manages to reduce weight with new seat concepts featuring integrated functions that require less material. While offering the same range of features, today's seats require far fewer components, with each component performing multiple functions. Johnson Controls managed to decrease the amount of parts for a backrest structure by about 50 percent. As less parts are required, far fewer assembly and production steps are needed, which in turn reduces costs.
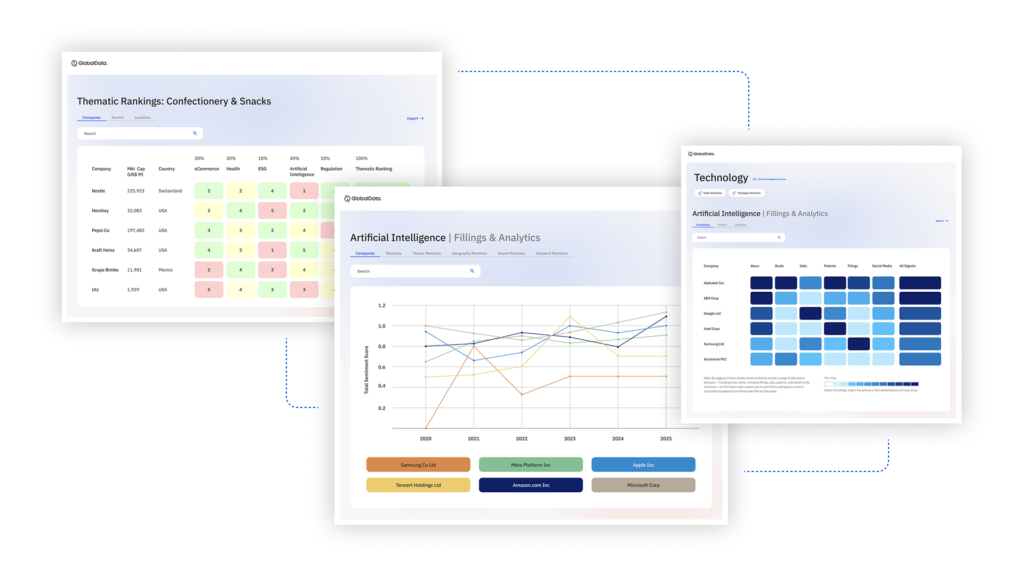
US Tariffs are shifting - will you react or anticipate?
Don’t let policy changes catch you off guard. Stay proactive with real-time data and expert analysis.
By GlobalData"As with all new developments, the cost factor must always be borne in mind", explained Jürss. "After all, our long-term goal is to use the new technologies to equip mass produced, and not just premium segment, passenger vehicles with our seats. This is also the aim of our Tailored Hybrid Tubes lightweight construction project for which we employ a combination of steel and aluminum. Because the tubes for the respective seat model are 'tailor made,' this generates huge material savings."