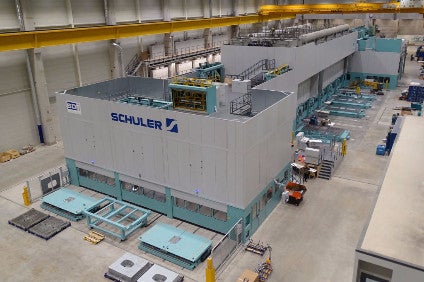
A new six-stage body press line has gone into operation at Daimler's Kuppenheim press shop. The new press line supplies the nearby Mercedes-Benz plant in Rastatt with outer skin components made from diverse materials for compact cars.
Daimler said the new line boosts Kuppenheim's expertise in lightweight body construction and supports the growth of the current compact car generation. It is part of a network of closely integrated production facilities in Baden-Wuerttemberg's Murgtal region in Germany which produces parts, components and modules as well as assembling compact vehicles.
Mercedes-Benz is spending EUR170m expanding Kuppenheim, creating 200 additional jobs in the process.
"Kuppenheim II is part of the Mercedes-Benz Cars growth strategy. In expanding Kuppenheim and integrating the facility into our global press shop network, we are bundling the stamping production for the Mercedes-Benz plant in Rastatt. This paves the way for future growth of our current generation of compact cars. Top priority of the expansion was the efficiency and flexibility of the equipment," said production and supply chain chief Markus Schäfer. "This enables us to respond flexibly to customers' demand and market requirements and boosts our international competitiveness."
The new facility supplies car factories in Rastatt, Germany, Kecskemét, Poland and Finnish contract manufacturer Valmet Automotive with body stampings made of various different steel and aluminium types. The press shop in Kuppenheim is part of an integrated network which includes facilities in Sindelfingen, Bremen, Hamburg and Kecskemét. The press shop network forms part of the Mercedes-Benz Cars Technology Factory.
"We will continue to invest in the Kuppenheim plant. In the next step, we will add a body shell shop which will produce modules and components for the next generation of compact cars," Schäfer said.
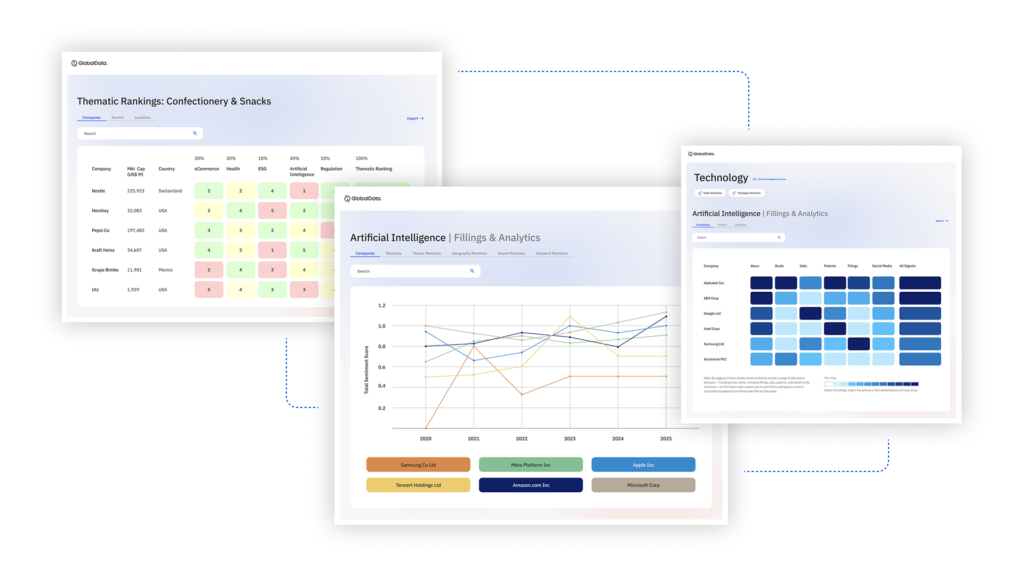
US Tariffs are shifting - will you react or anticipate?
Don’t let policy changes catch you off guard. Stay proactive with real-time data and expert analysis.
By GlobalDataSince 2011, the Kuppenheim press shop has produced body components for compact vehicles and Daimler Trucks in a facility covering 92,000 square metres of floor space. With the new press line, the existing press shop has been expanded by an additional 25,000 square metres of production and storage space.
Centrepiece of the expansion is a six-stage XL servo press with a total pressing force of 9,100 tonnes. It is 120m long, 12m high and weighs 3,850 tonnes. Vibration dampers consisting of giant steel springs on the foundation ensure that the vibrations resulting from the operation of such vast presses are completely absorbed. Large and complex outer skin components such as side walls, bonnets and doors for the compact vehicles will be formed on this press in the future. A new try-out press in the same building serves to prepare new or reworked tools for production.
The goods management system works 100% paperless. All processes are electronically documented and forwarded, from orders by the Rastatt plant through production and logistics processes to delivery to the Rastatt body shell shop. A servo drive on the press reduces power consumption per produced part and increases output. The new automatic front-of-line area in front of the press ensures a smooth supply of pre-cut sheet-metal blanks. Efficiency also characterises the end-of-line area, thanks to finely coordinated operations between man and machine. A prime example is the computer-assisted quality control. First of all, a robot equipped with a special camera system and special software examines all produced parts. Afterwards, workers refer to the results of this inspection when carrying out their final appraisal of the parts. This computerised support for the personnel in performing their responsible work was first introduced at the Bremen plant in 2014 and has since contributed to the consistently high quality of produced components.
A new stacking system for finished parts in Kuppenheim also takes the strain off workers by automatically placing the sometimes bulky parts in the waiting special load carriers. A barcode on the load carrier then indicates the transfer location to the logistics workers.
The laser blanking line is a completely new development. This machine cuts the aluminium and steel sheet metal parts to size before they are formed into plates in the press. The special feature of this process is the cutting of the blanks by laser, and that the material is continuously fed into the plant. This completely eliminates the complex process of producing the previously required large cutting tools – another significant contribution to efficient and flexible production.