
BMW Manufacturing in Spartanburg, South Carolina, has opened a press shop as it prepares to assemble the redesigned X3.
The press shop is stamping sheet metal parts for the new SUV including hang-on parts such as the doors, fenders, lift gate and exterior body sides.
BMW production chief Milan Nedeljkovic said: “This is a further step towards strengthening our global resilience.”
By 2030, BMW will assemble at least six fully electric models in the US. Their high voltage batteries will come from nearby Woodruff where the automaker is building an assembly plant for sixth generation batteries.
Robert Engelhorn, president and CEO of BMW Manufacturing, said: “Having this press shop on site fits the group’s local for local strategy where we produce major parts at the location where we need them.”
The group spent US$200m to construct the 219,000 square foot press shop which took two years from site preparation to stamping the first part.
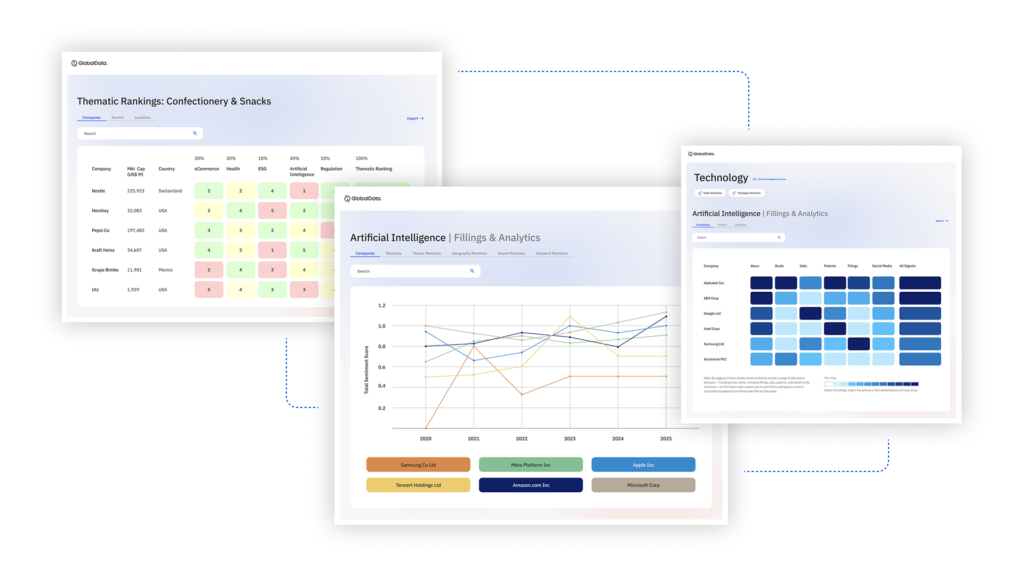
US Tariffs are shifting - will you react or anticipate?
Don’t let policy changes catch you off guard. Stay proactive with real-time data and expert analysis.
By GlobalDataThe spend also included 200 new jobs for tool and die technicians plus electrical and mechanical maintenance for automated machinery.
Workers trained at group press shops in Swindon, UK and Leipzig, Germany which export panels as part of the CKD kits assembled in the US.
Spartanburg has assembled 1.7m X3s since the model was introduced in 2010. The new model goes on sale in autumn 2024.
The first X5 was assembled in 1999 and 3m have since been built.
In the new press shop, large steel coils are unloaded from trucks using a large overhead crane inside the shop. The coils are then fed into the coil line where the steel is cut into individual blanks at up to 70 strokes per minute and these are fed into the press line which consists of five stamping stations.
The line is equipped with servo technology which “significantly” increases the output performance of the presses.
An overhead crane moves the correct die into each station and the blank is fed in and transferred from one station to the next by robot like automation, referred to as the crossbar feeder” for additional forming and trimming operations. The line can run up to 18 strokes per minute stamping out up to 10,000 parts each day.
After the parts are stamped, they go to quality control for inspection; quality inspectors use special lighting that mimics natural daylight. Parts are then stacked into racks ready for delivery to the body shop.
Up to 50 tons of scrap are accumulated each day at full volume; a long conveyor moves the scrap, and it is loaded onto 53-foot trailers. All this material is taken off site to be recycled.
This year, BMW Manufacturing celebrates 30 years of assembly and 6.7m vehicles. It started by building 3-series sedans and now employs 11,000 people.
The 1,150 acre, 8m square foot campus houses three body shops with 2,600 robots, two paint shops and two assembly halls. The plant generates about 20 percent of its own power from methane gas and uses hydrogen fuel cells to power about 800 pieces of material handling equipment.